
complete wood pellet plant for sale
RICHI specializes in complete wood pellet plant for sale, our wood pellet plant comes with everything you need to process just about any agricultural and forestry waste, including Straw, sawdust, wood chips, tree trunks, branches, leaves, building formwork, wooden pallets, wood scraps, palm waste, rice husks, peanut shells, coconut shells, olive waste, sunflower seed shells, vines, brewing waste, hay, cassava, beet pulp, etc. Coal, bentonite, waste paper, cartons, etc. can also be used as raw materials. The pellets processed by the wood pelleting plant can be used for many purposes such as fuel, feed, cat litter, etc.
It can be used to produce pellets of all kinds, allowing you to speed up your production process and improve your bottom line. (You can use a single raw material or multiple raw materials, but the design of the process will be different.)
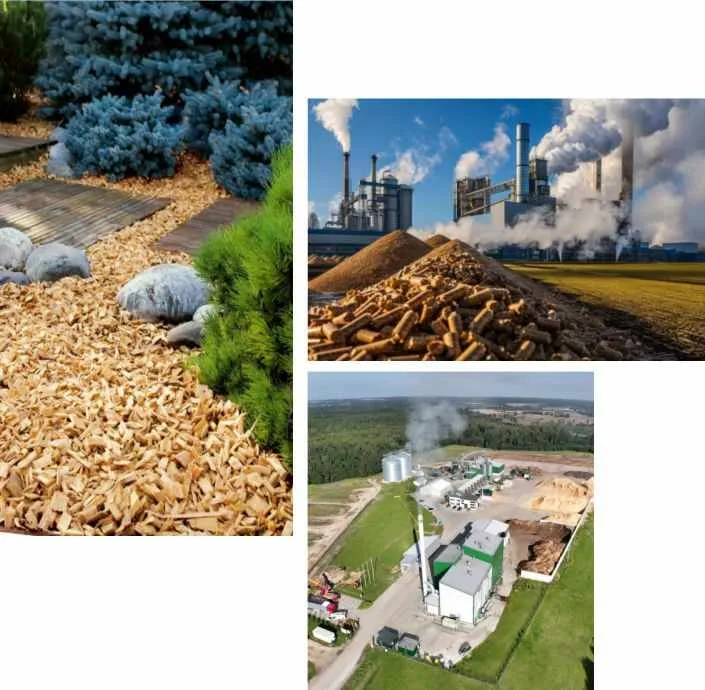
complete wood pellet plant solution
RICHI Machinery is mainly engaged in complete wood pellet plant for sale, our comprehensive wood pellets plant for making wood waste pellets, it comes with everything you need. It has seven main parts: a wood chipper, heating stove, wood pellet mill, packing machine, cooler, hammer mill, and dryer. It’s truly a one-of-a-kind line that will allow you to make wood chips, wood board, log, trunk, branch and more.
The wood pellet machines and the wood pellet line solutions, specifically designed and conceived according to the raw materials involved, are fit to turn the following into high-output fuel:
- Forest waste: waste from wood processing, from pruning and also material from purposefully grown plantations.
- Agricultural waste: cereals straw and the like, alfalfa, hay, miscanthus, etc.
- Industrial waste, basically waste from certain alimentary productions, such as sansa, residues from juice productions, etc.
● RICHI MACHINERY
Raw material requirements
Our customized complete wood pellet plant are suitable for any material, regardless of size, moisture content, purity or not. However, there are requirements for raw materials before granulation. This requires a series of treatments before the materials enter the granulation system, such as crushing, cleaning, drying, etc. For different raw materials, the pre-treatment process and equipment are different.

Different types of raw materials
In one pellet plant, you can use a single raw material, such as sawdust, wood chips, logs, straw, or you can use multiple raw materials at the same time, even if they are of different types, sizes and material properties.
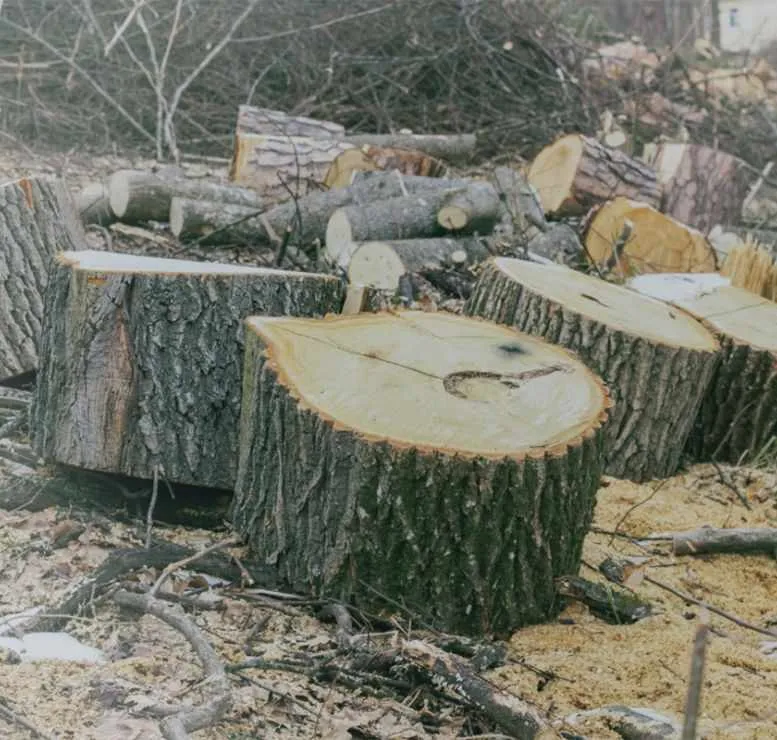
Different raw material moisture
If the moisture content of your material is ≤ 20%, then there is no need to configure a drying system in the wood pellet production line. If the moisture content of the material is > 20%, a drying system needs to be added.

Different raw material sizes
Logs, branches, wood chips, templates, straw, efb, peanut shells, leaves, bamboo, olive pomace, cartons, waste paper, coffee shells, sunflower shells, sugar cane, hay, hemp, haystacks or any other materials, you can choose one raw material or different raw materials. The crushing process and crushing equipment for different raw materials may be different. A flexible combination of different crushing equipment is required to crush the material to about 3mm.
RICHI MACHINERY
video Of complete wood pellet plant engineering
We have a lot of complete wood pellet plant operation site videos to share with you. Below are some of our latest project videos. If you are interested in our projects, feel free to contact us for detailed information!
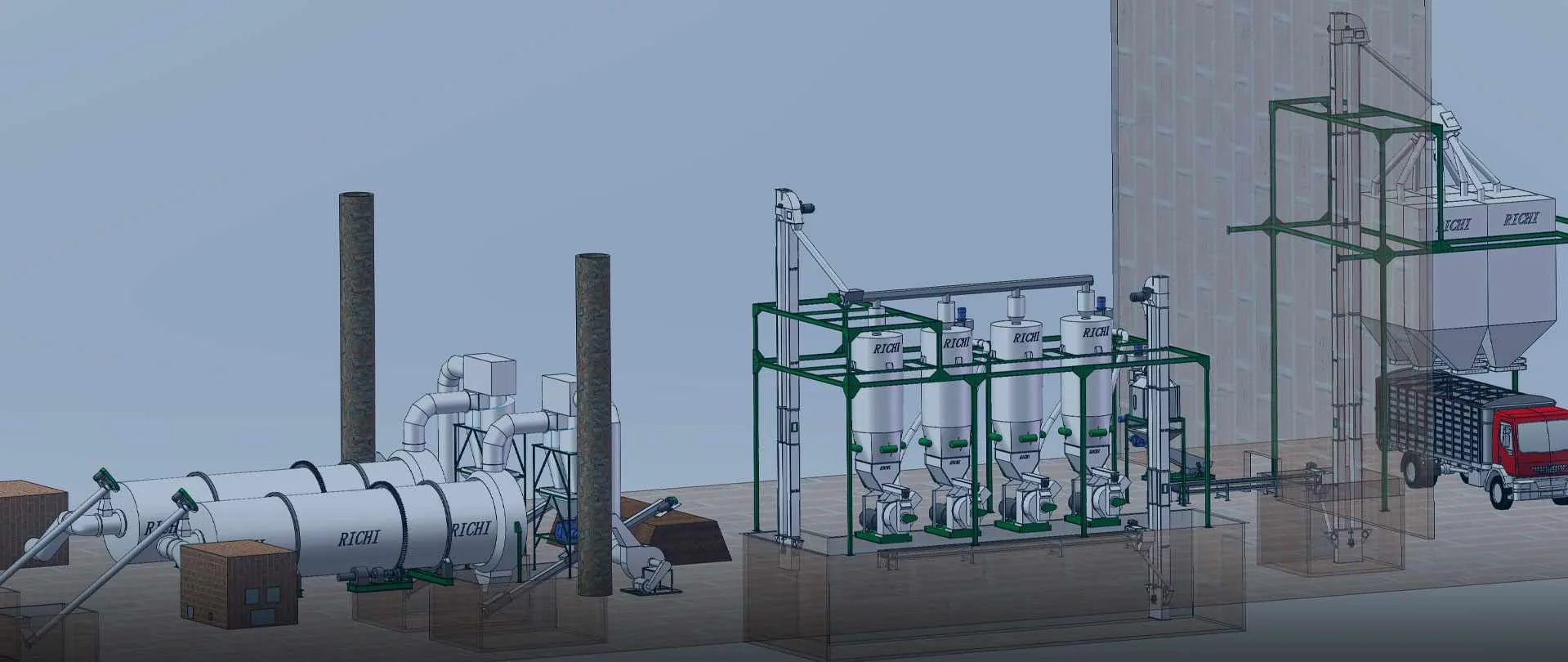
wood pellet production process
The wood pellet processing process usually includes cleaning, crushing, drying, granulation, cooling, screening, packaging, etc., and is also equipped with necessary configurations such as electronic control system, conveying and conveying, dust removal system, etc. Depending on the needs, silo system, mixing system, etc. are sometimes also configured.
Cleaning section
Magnetically separate and screen logs, branches, wood chips and other wood materials to remove impurities and obtain clean wood materials.
Crushing section
Crush the clean wood raw materials to 3-5mm through a hammer mill or chipper to obtain fine wood particles.
Drying process
The fine wood particles are passed through a drum dryer or airflow dryer to reduce the moisture content to below 12% to obtain dry wood particles.
Granulation section
The dried wood raw materials are pressed into cylindrical pellets with a diameter of 6-14mm and a length of 10-30mm through a wood pellet mill machine.
Cooling section
The prepared wood pellets are cooled to near room temperature through a countercurrent cooler.
Screening section
The cooled pellets are passed through a vibrating screen to remove unqualified pellets and powder, and qualified wood pellets are obtained.
Packaging section
The screened qualified wood pellets are packaged into 15kg, 20kg, 25kg and other specifications by automatic packaging machines.
Electrical control system
Control the operation of the complete wood pellet plant and realize automation.
Auxiliary system
In the actual wood pellet processing process, dust removal system, steam system, silo system, conveying system, etc. are also required.
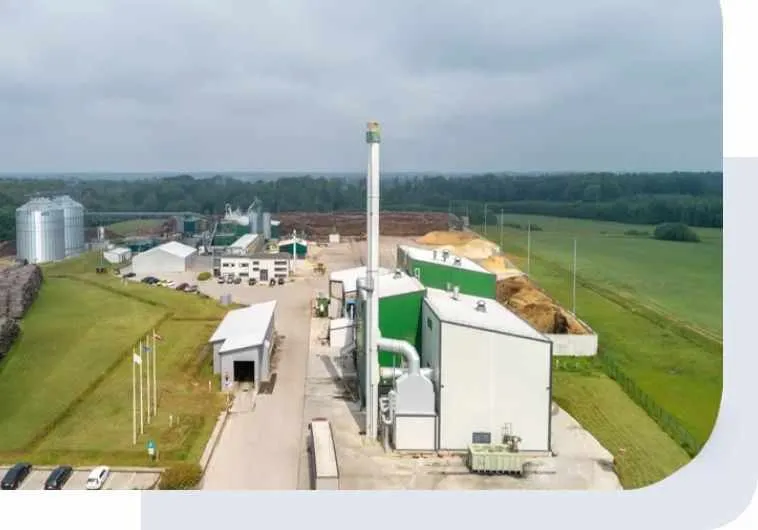
complete wood pellet plant construction
Depending on the raw materials, production scale, and plant conditions, the process design and configured equipment will be different.
You can count on extensive support in realising your idea, obtaining the official building permission, planning, engineering and commissioning.
Our after-sales service includes spare parts, repair service, maintenance and servicing of your wood pelleting plant.
Customized Complete wood pellet plant design
— Richi Machinery —
The process of the wood pellet plant needs to be customized. Cleaning – crushing – drying – granulation – cooling – screening – packaging, this process is just a relatively standard processing flow, but in the actual process, according to customer needs, the final process of many projects is different from the standard process. Below, RICHI will show you some customized wood pellet processing process flow charts we have done.
0.3-0.5 t/H complete wood pellet plant design
Raw Materials: dry wood chips
Process flow: Iron removal – crushing – air transport & dust removal system – granulation – manual packaging
Main wood pellet plant equipment:Wood hammer mill, cyclone dust collector, wood pelletizer, belt conveyor.
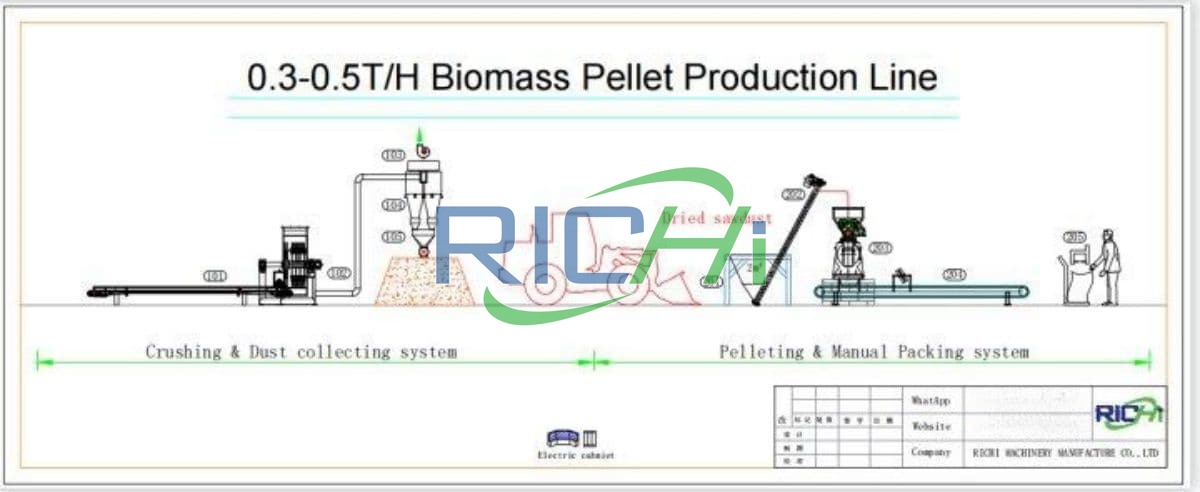
0.5-0.7 ton per hour complete wood pellet plant design
Raw Materials: Wet wood chips
Process flow: Iron removal – crushing – stockpiling – drying – granulation – cooling – screening
Main wood pellet plant equipment: Wood hammer mill, cyclone dust collector, sawdust drying drum, pelletizer, cooler, vibrating screen, crimping conveyor.
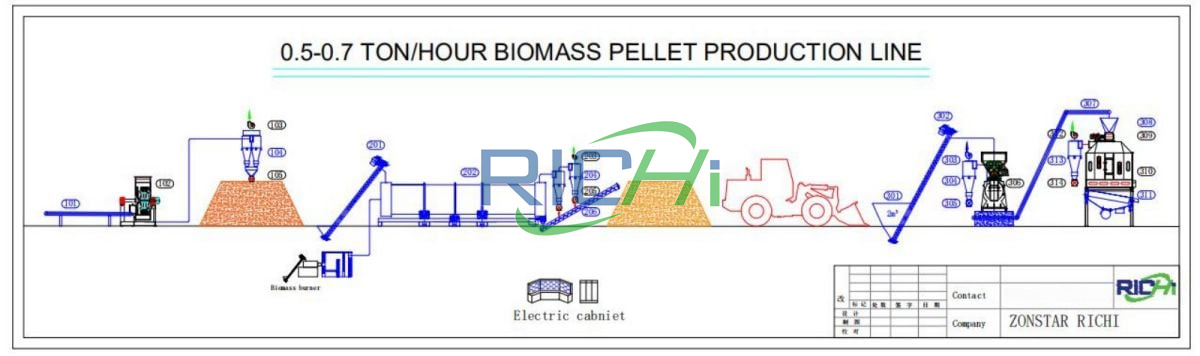
1-1.2T/H complete wood pellet plant design
Raw Materials: Logs, blocks, strips, planks
Process flow: Slicing – crushing – iron removal and cleaning – storage – drying – storage – granulation – cooling – screening – packaging
Main wood pellet plant equipment: Slicer, wood hammer mill, drum screen, dryer, sawdust silo, pelletizer, cooler, vibrating screen, baler, conveyor, bucket elevator, etc.
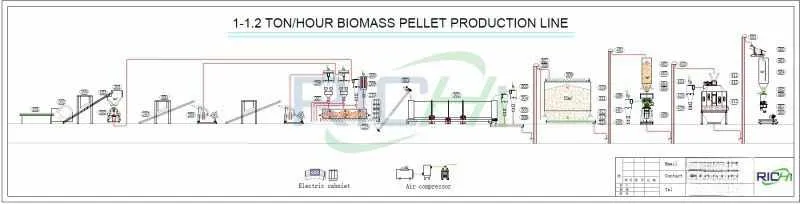
2-2.5 T/H complete wood pellet plant design
Raw Materials: Logs, blocks, strips, planks, tree stump, branches
Process flow: chipping——crushing——storage——drying——silo storage——granulation——cooling——screening——packaging
Main wood pellet plant equipment: Slicers, grinders, drying drums, silos, pelletizers, coolers, vibrating screen, ton bag scale, bucket elevator, scraper conveyor, etc.
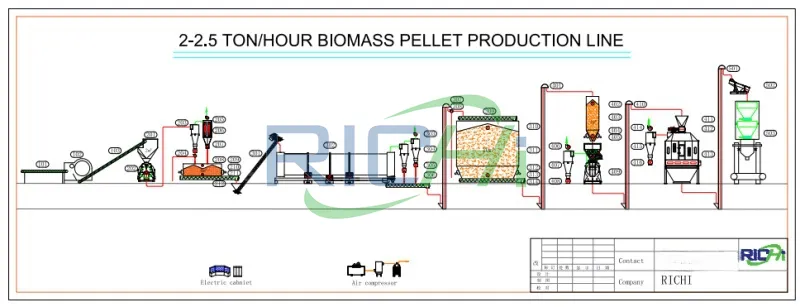
4-5 T/H complete wood pellet plant design
Raw Materials: Logs, trunks, branches, planks, etc.
Process flow: chipping——crushing——storage——granulation——cooling——screening——packaging
Main wood pellet plant equipment: Slicers, crushers, buffer bins, pelletizers, coolers, screeners, wood pellet packaging machines, bucket elevators, etc.
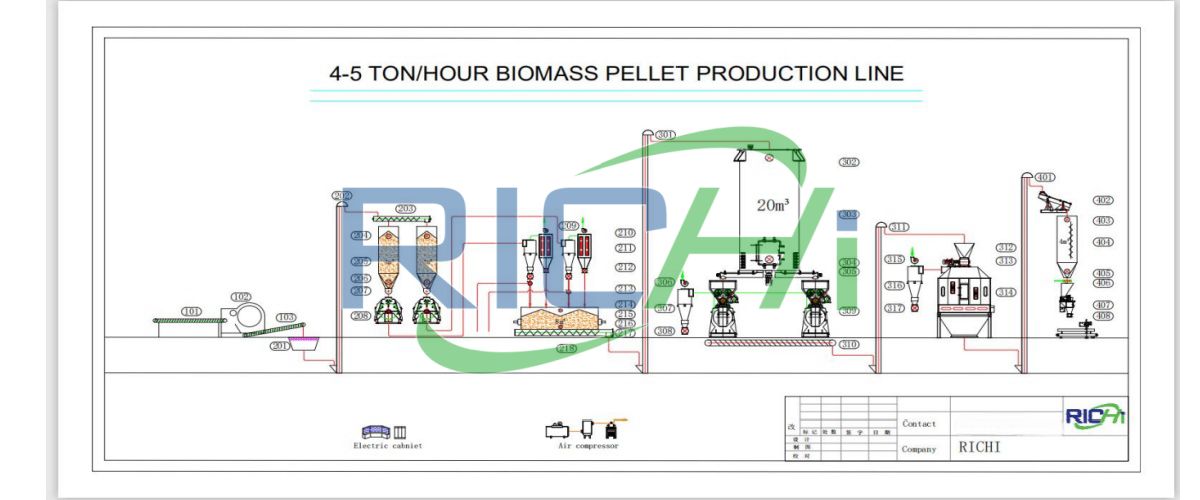
8-10 T/H complete wood pellet plant design
Raw Materials: Clean wet wood chips and dry wood chips with impurities
Process flow: Clean wet wood chips crushing – drying – cleaning of dry wood chips with impurities – crushing – silo storage – pelletizing – cooling – finished product transportation – container
Main wood pellet plant equipment: Crusher, dryer, drum screen – silo – wood chip pellet machine – cooler – vibrating screen – finished product conveyor
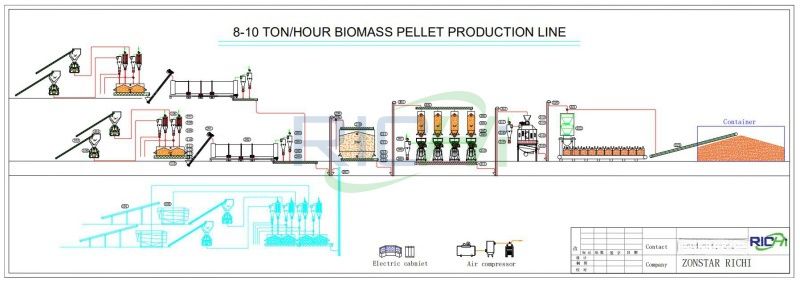
10-12 T/H complete wood pellet plant design
Raw Materials: Dry sawdust, dry wood chips
Process flow: Crushing – conveying & iron removal – raw material cleaning and screening – granulation – cooling – particle screening – storage
Main wood pellet plant equipment: Crusher, conveyor, drum screen, granulator, cooler, vibrating screen, bucket elevator, Z-type bucket elevator, belt conveyor, etc.
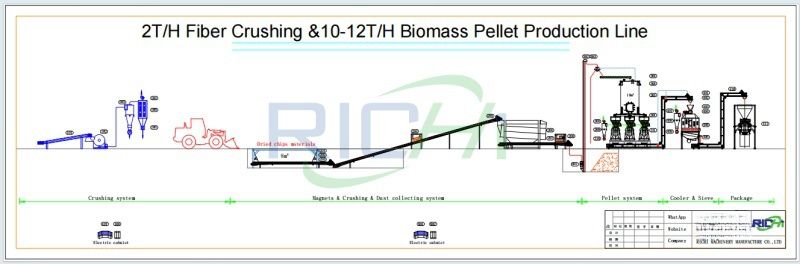
16-20 T/H complete wood pellet plant design
Raw Materials: Logs, wood chips
Process flow: chipping——crushing——drying——granulation——cooling——screening——packaging
Main wood pellet plant equipment: Chipper, hammer mill crushers, wood dryers, pelletizers, coolers, screeners, wood pellet packaging machines, conveyors, etc.

supporting equipment for complete wood pellet plant
— Richi Machinery —
Our high-quality and long-lasting complete wood pellet plants consist of various processing machines that meet the wishes and requirements of our customers regarding wood pellets. You can find equipment for all aspects of wood particle processing, crushing, drying, storage, etc. at RICHI MACHIENRY.
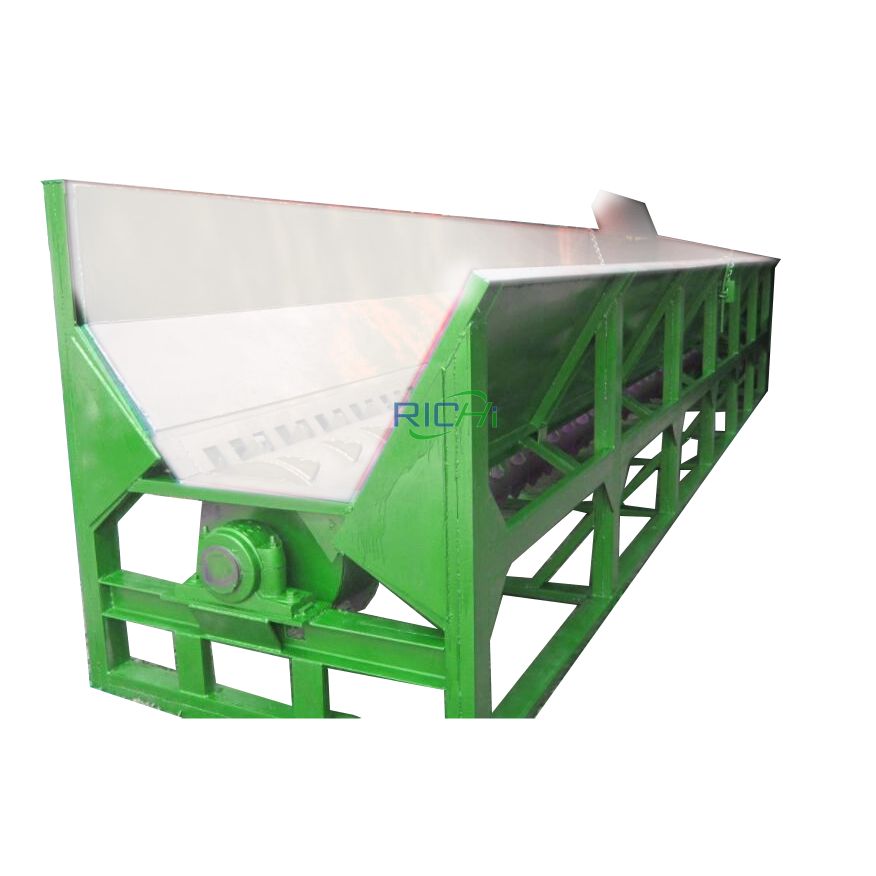
debarking machine
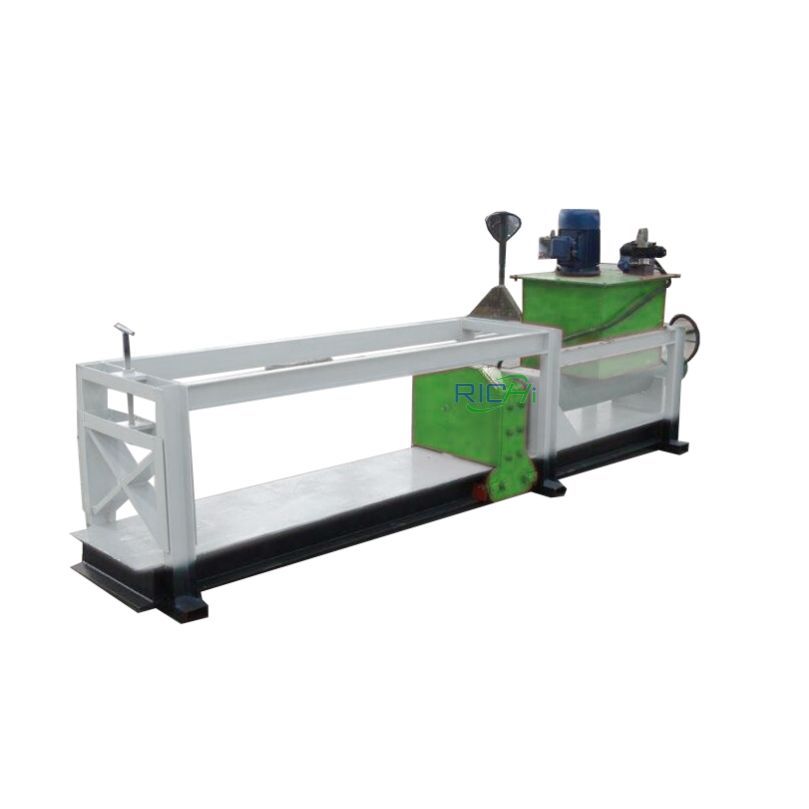
Wood splitter machine
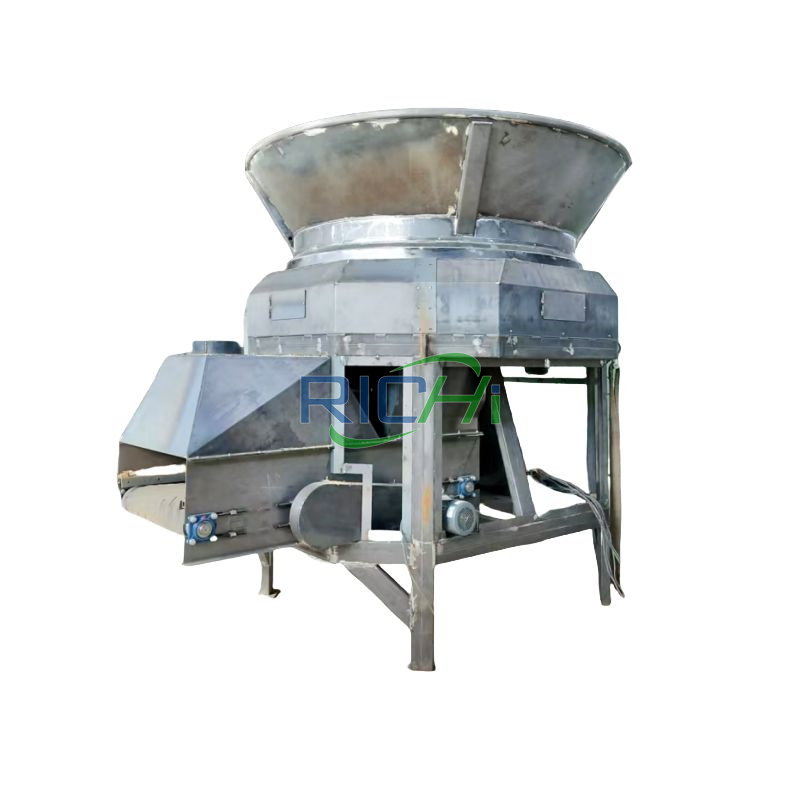
wood Shredder
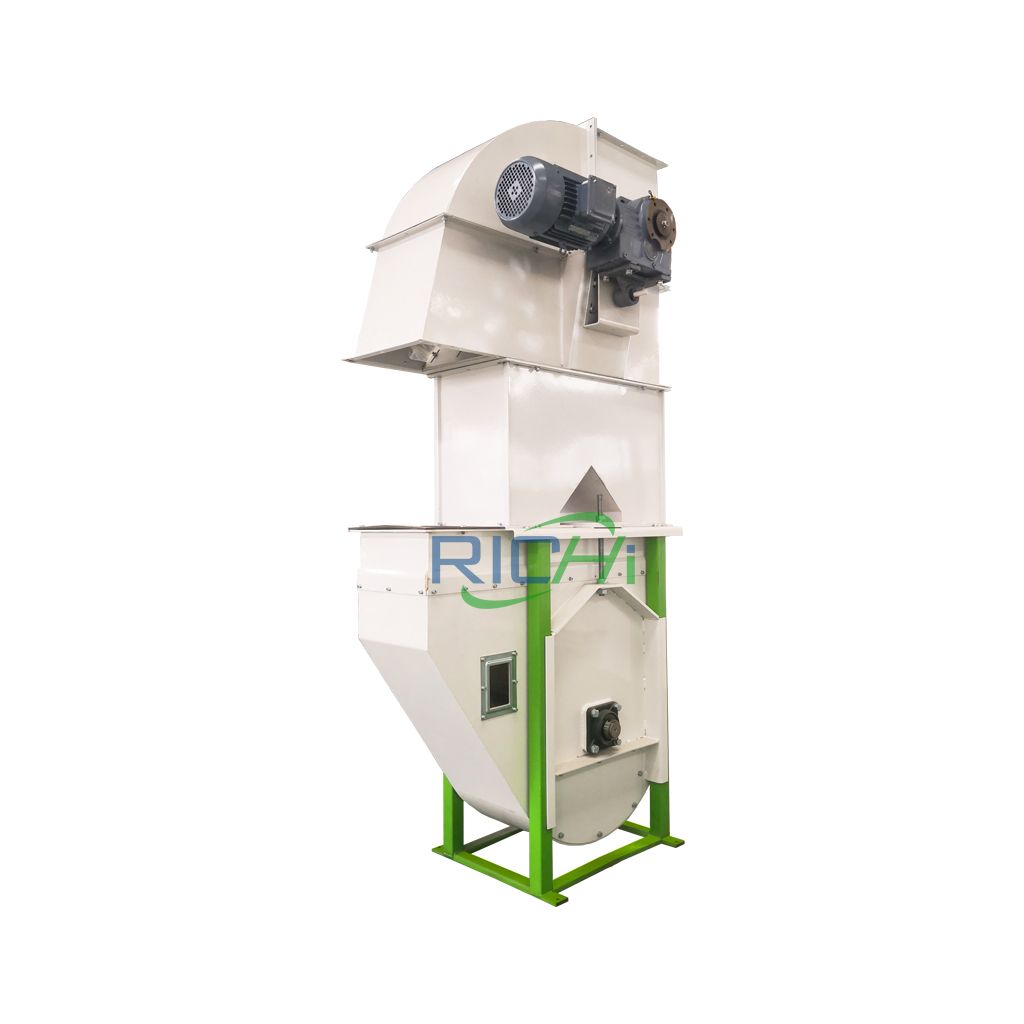
Bucket Elevator
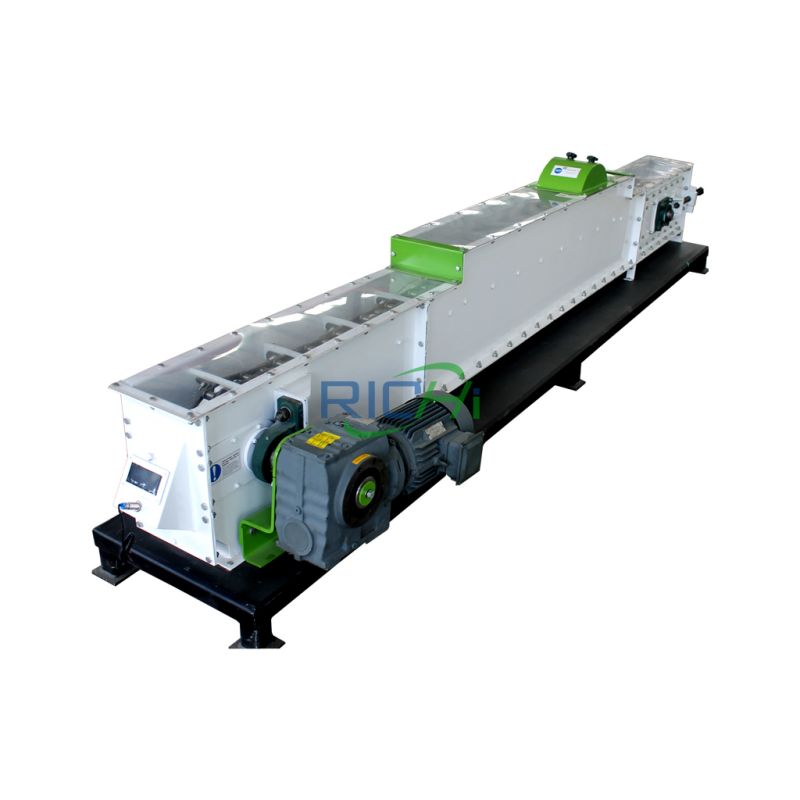
Scraper conveyor

Belt conveyor
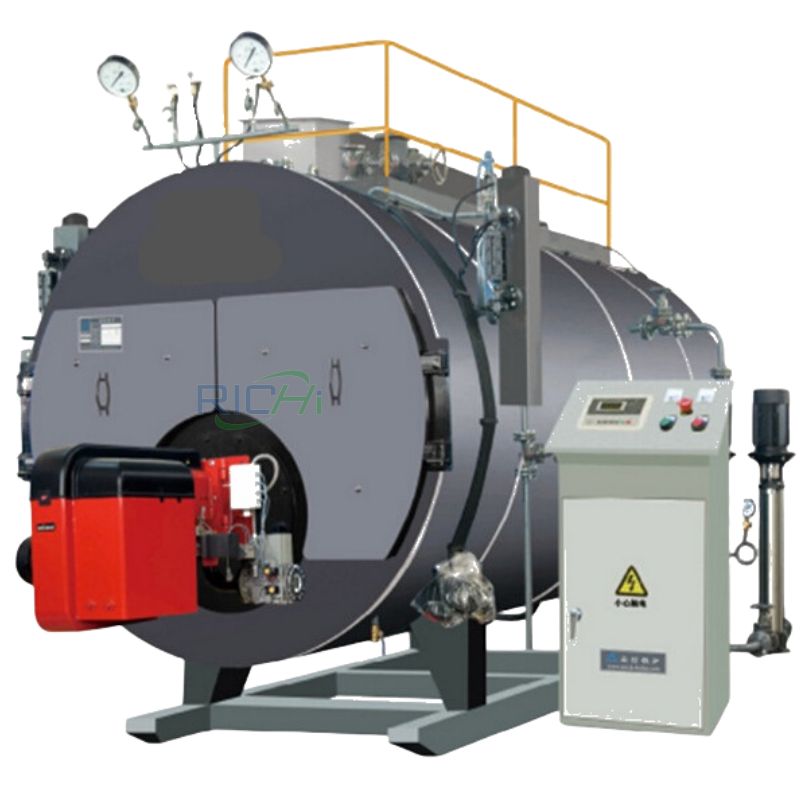
Steam Boiler
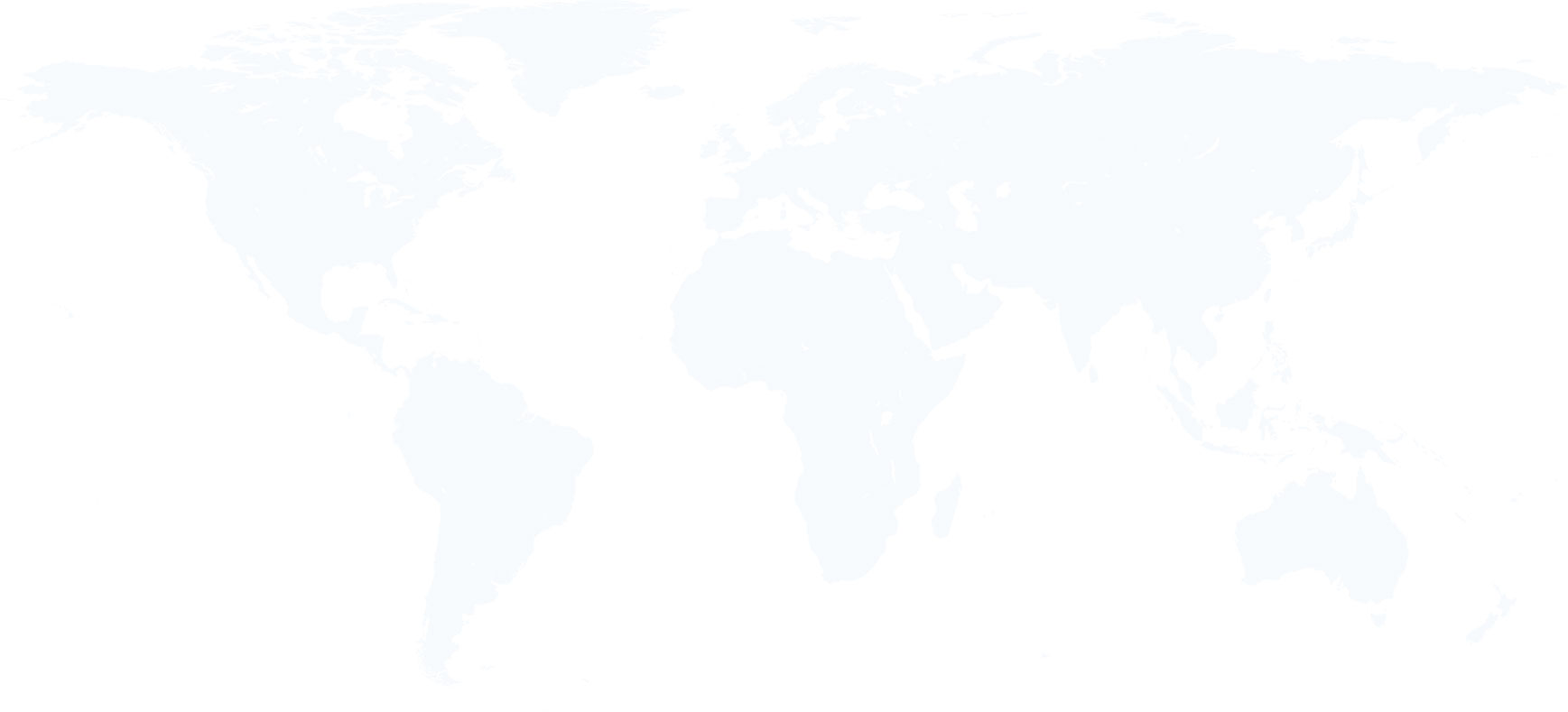
1-1.2T/H wood pellets plant equipment list
Here is a list of main equipment needed for a standard 1-1.2 t/h complete wood pellet plant.
NAME | MODEL | QTY |
Wood chipper | XPJ500x230 | 1 |
Wood crusher | SFSP 66*60 | 1 |
Drying machine | ф1200*120000 | 1 |
Anti-caking equipment | MZLH 420 | 1 |
Wood pelletizer | 1 | |
Cooling machine | SKLN11*11 | 1 |
Vibrating screener | TDZS63 | 1 |
Packing machine | DCS-50 | 1 |
Belt and sewing machine | 1 | |
MCC Control Center ;Mimic control panel (power range from 22 kw to 55 kw for star triangle start, main electric components are delixi brand) |
NAME | MODEL | QTY |
Wood chipper | XPJ680x300 | 1 |
Wood crusher | SFSP 66*80 | 1 |
Drying machine | ф1500*150000 | 1 |
Anti-caking equipment | MZLH678 | 1 |
Wood pelletizer | 1 | |
Cooling machine | SKLN14*14 | 1 |
Vibrating screener | TDZS63 | 1 |
Packing machine | DCS-50 | 1 |
Belt and sewing machine | 1 | |
MCC Control Center ;Mimic control panel (power range from 22 kw to 55 kw for star triangle start, main electric components are delixi brand) |
2-2.5T/H wood pellets plant equipment list
Here is a list of main equipment needed for a standard 2-2.5 t/h complete wood pellet plant.
4-5T/H wood pelleting plant equipment list
Here is a list of main equipment needed for a standard 4-5 t/h complete wood pellet plant.
NAME | MODEL | QTY |
Wood chipper | XPJ500*500 | 1 |
Wood crusher | SFSP66*80 | 2 |
Drum dryer | ф2400*100000 *3 Layer | 1 |
Anti-caking equipment | MZLH520 | 2 |
Wood pelletizer | 2 | |
Cooling machine | SKLN17*17 | 1 |
Vibrating screener | TDZS63 | 1 |
Packing machine | DCS-50 | 1 |
Belt and sewing machine | 1 | |
MCC Control Center ;Mimic control panel (power range from 22 kw to 55 kw for star triangle start, main electric components are delixi brand) |
NAME | MODEL | QTY |
Wood chipper | XPJ850*500 | 1 |
Wood crusher | SFSP66*60 | 2 |
Wood crusher | SFSP66*80 | 2 |
Drying machine | ф1800*180000 | 2 |
Anti-caking equipment | MZLH520 | 3 |
Wood pelletizer | 3 | |
Cooling machine | SKLN17*17 | 1 |
Vibrating screener | TDZS63 | 1 |
Packing machine | DCS-50 | 2 |
Belt and sewing machine | 1 | |
MCC Control Center ;Mimic control panel (power range from 22 kw to 55 kw for star triangle start, main electric components are delixi brand) |
6-7T/H wood pellet plant equipment list
Here is a list of main equipment needed for a standard 6-7t/h complete wood pellet plant.
8-10T/H wood pelletizing plant equipment list
Here is a list of main equipment needed for a standard 8-10 t/h complete wood pellet plant.
NAME | MODEL | QTY |
Wood chipper | XPJ850*600 | 2 |
Wood crusher | SFSP66*80 | 4 |
Drum dryer | ф2400*100000 *3 Layer | 2 |
Anti-caking equipment | MZLH768 | 3 |
Wood pelletizer | 3 | |
Cooling machine | SKLN20*20 | 1 |
Vibrating screener | TDZS80 | 1 |
Packing machine | DCS-50 | 1 |
Belt and sewing machine | 1 | |
MCC Control Center ;Mimic control panel (power range from 22 kw to 55 kw for star triangle start, main electric components are delixi brand) |
Reasons to invest in complete wood pellet plant
High profit & quick payback
- Low-cost raw materials: Using cheap biomass such as waste wood and straw, the cost of raw materials is 30%-50% lower than fossil fuels.
- High added value: Industrial-grade pellets are sold at $120-180/ton, and high-end certified pellets (such as EN Plus) can reach $300/ton.
- Fast payback: Medium-sized production lines (2-5 tons/hour) usually pay back in 2-3 years (calculated based on full-load production).
Global market demand explodes
- Rigid demand in Europe: EU’s renewable energy target for 2030 is 32%, and wood pellet imports are increasing by 10% annually.
- Asia policy drive: China, Japan, and South Korea subsidize biomass energy to replace coal-fired boilers.
- Household heating growth: North American/European household pellet fireplaces are popular, and small-package pellets are more profitable.
Environmental policy dividends
- Carbon tax benefits: The EU Carbon Border Tax (CBAM) has driven companies to turn to biomass energy.
- Government subsidies: For example, China provides electricity price subsidies for biomass projects, and the US Department of Agriculture has a REAP funding program.
- ESG investment hotspots: In line with the global trend of carbon neutrality, it attracts cooperation from green funds.
Flexible adaptation to a variety of raw materials
- Not picky about materials: compatible with sawdust, branches, straw, fruit shells and even bamboo (differentiated competitive point).
- Low threshold: no complicated pretreatment is required, and raw materials with a moisture content of ≤20% can be directly processed. Customized formula: The mold can be adjusted to produce particles of different specifications from 6mm to 14mm.
Automation & Low Operation Pressure
- 24-hour continuous production: automated feeding, pelletizing, and packaging, requiring only 2-3 people in shifts.
- Low failure rate: mature ring die technology (such as Germany’s Bühler) has a lifespan of more than 10 years.
- Energy consumption optimization: 1 ton of pellets consumes only 100-150kWh of electricity, and some models support solar auxiliary power supply.
One-stop support service
- Turnkey project: Provide all-inclusive services including complete wood plant design, equipment installation and technical training.
- Certification assistance: Assist in passing international certifications such as EN Plus and FSC, and open up export channels.
- After-sales guarantee: Remote monitoring + local engineer team, 24-hour response to failures.

RICHI MACHINERY
complete wood pellet plant for sale worldwide
The wood pellet plant equipment we design and manufacture is currently operating in more than 100 countries around the world. These are the results of our decades of strength and experience. We are lucky because our customers choose us. Customers are also lucky because they choose RICHI MACHINERY and get systems and equipment that can create sustainable value.
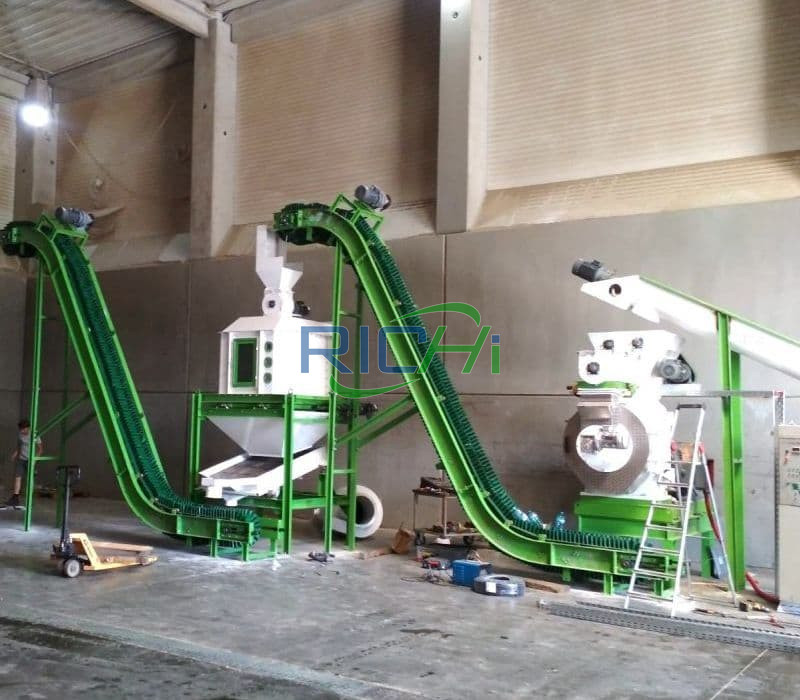
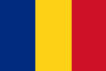
complete wood pellet plant for sale Romania
This project uses sawdust as raw material, with an output of 2-2.5 tons per hour. The project investment is approximately US$80,000.
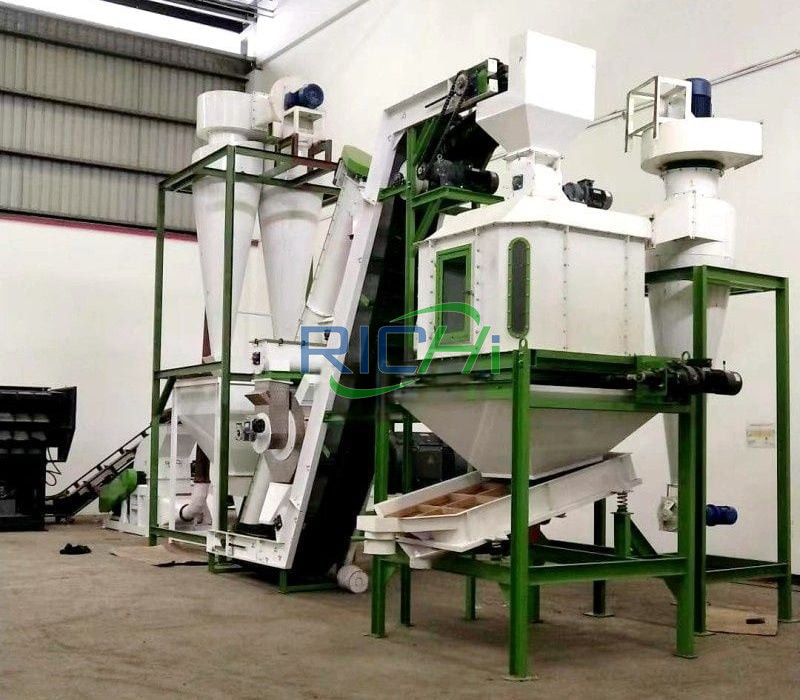
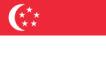
complete wood pellet plant for sale Singapore
The project uses thin wood strips as raw materials, with an output of 2 tons per hour. The project investment is about 110,000 US dollars.
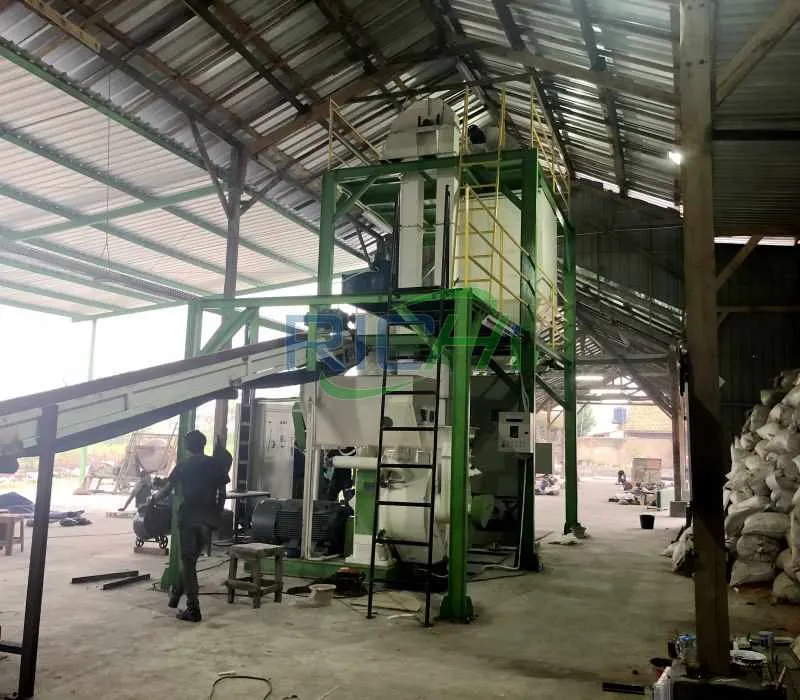
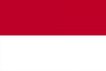
complete wood pellet plant for sale indonesia
This project uses logs as raw materials, with an output of 4 tons per hour. The project investment is approximately US$320,000.
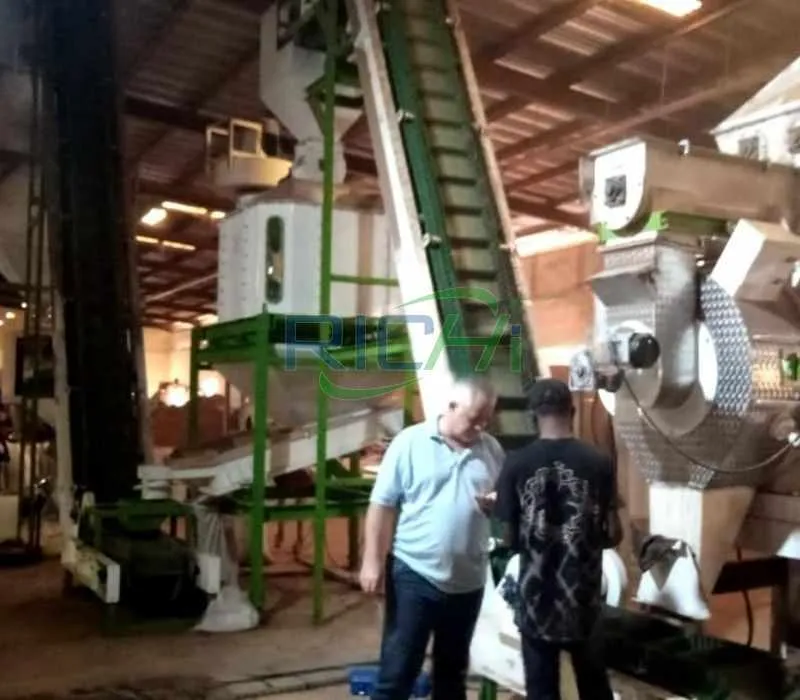
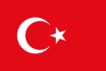
complete wood pellet plant for sale turkey
This project uses various wood waste as raw materials, with an output of 3 tons per hour. The project investment is approximately US$220,000.

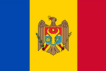
complete wood pellet plant for sale Moldova
The project uses logs and branches as raw materials, with an output of 5 tons per hour. The project investment is approximately US$360,000.
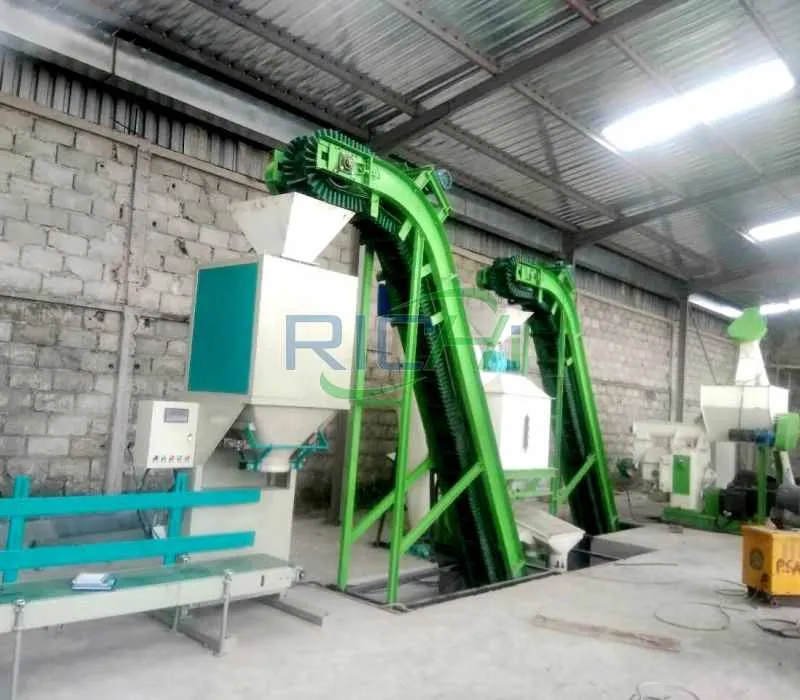
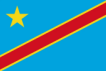
complete wood pellet plant for sale congo
This project uses wood chips and sawdust as raw materials, with an output of 1-2 t/h. The investment is approximately US$120,000.
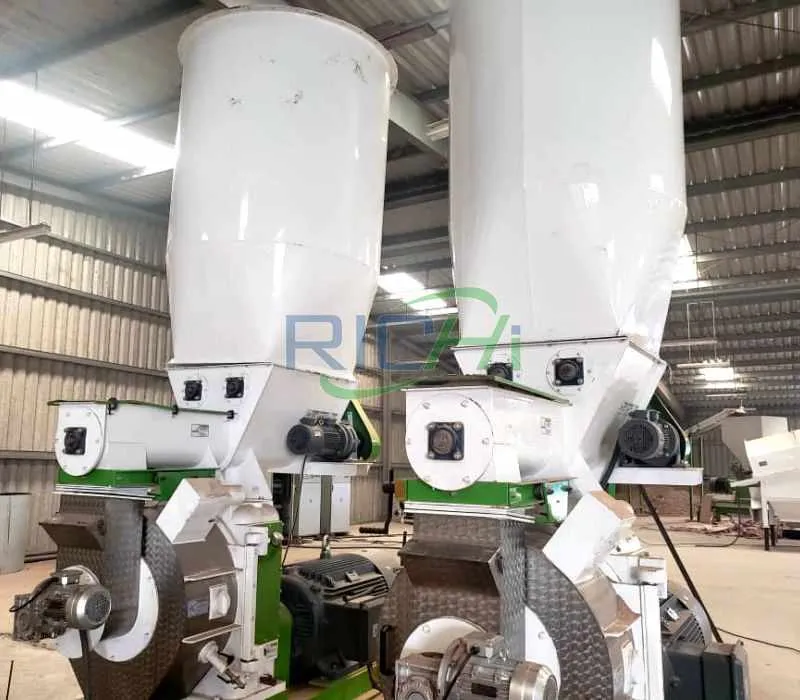
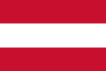
complete wood pellet plant for sale austria
This project uses a variety of wood waste as raw materials, with an output of 5 tons per hour. The project investment is approximately US$390,000.
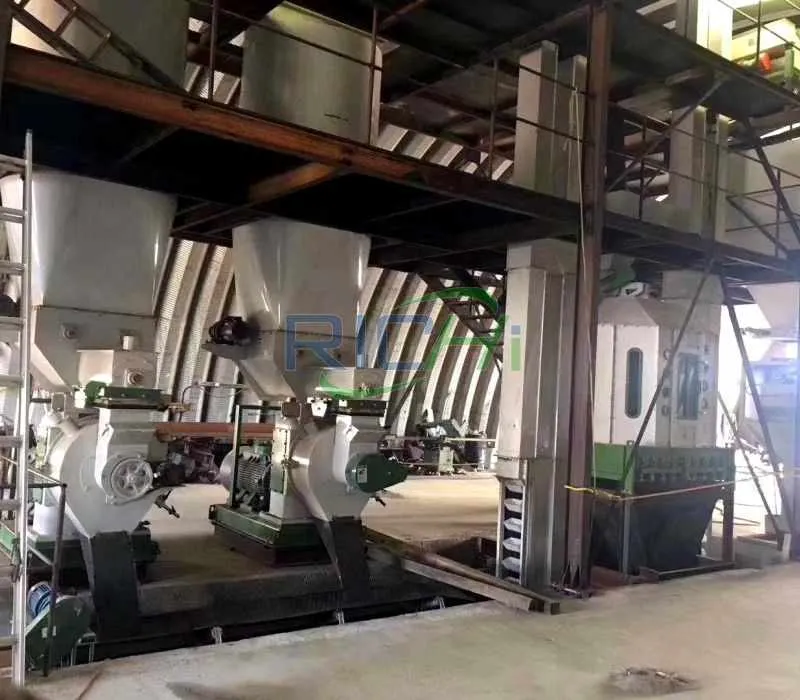
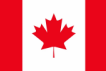
complete wood pellet plant for sale canada
This project uses tree trunks as raw materials, with an output of 6-8 tons per hour. The project investment is approximately US$450,000.
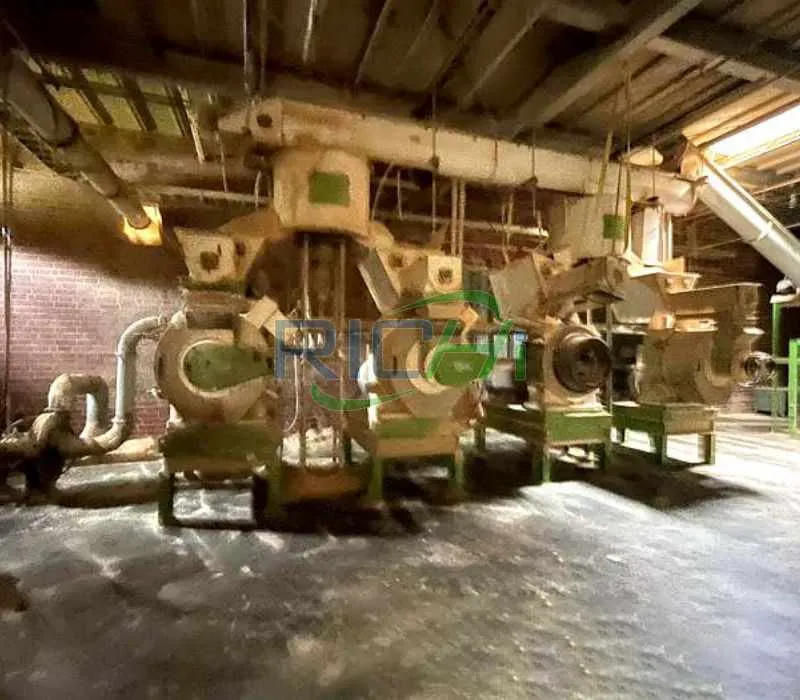
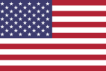
wood pelleting plant for sale USA
The project uses logs and planks as raw materials, with an output of 8-10 tons per hour. The project investment is approximately US$1.4 million.
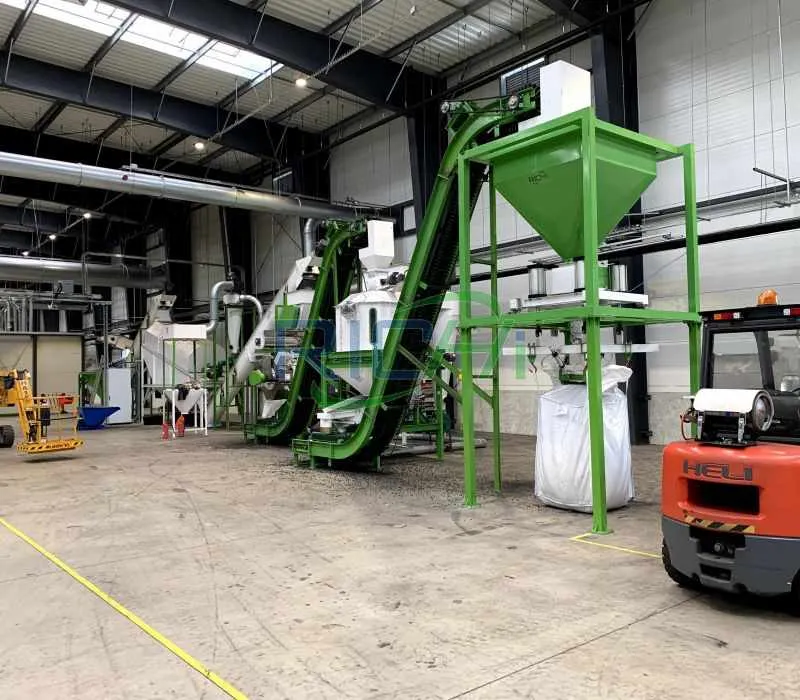

wood pellets plant for sale Poland
This project uses wood chips as raw materials, with an output of 4-5 tons per hour. The project investment is approximately US$360,000.
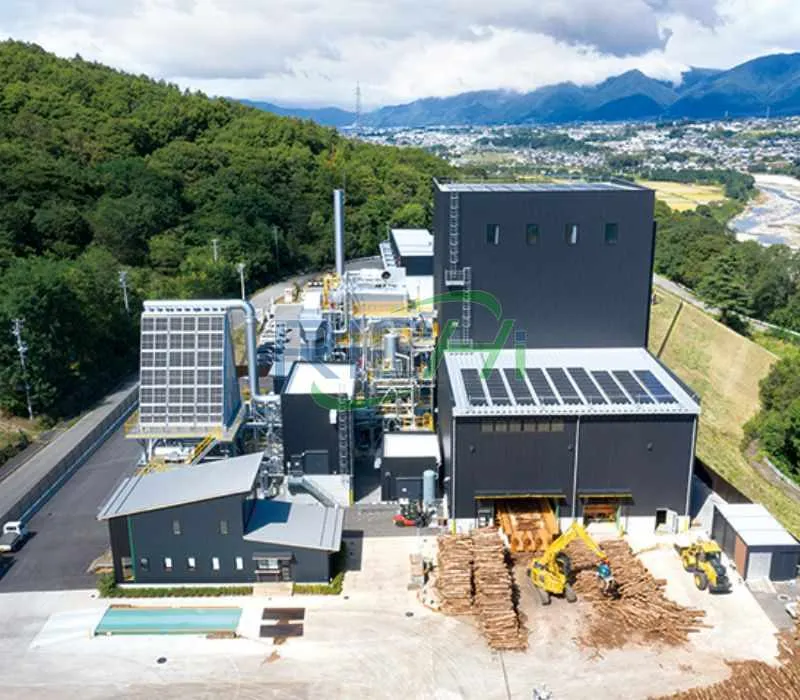
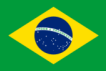
wood pelletizing plant for sale Brazil
This project uses logs as raw materials, with an output of 8 tons per hour. The project investment is approximately US$610,000.
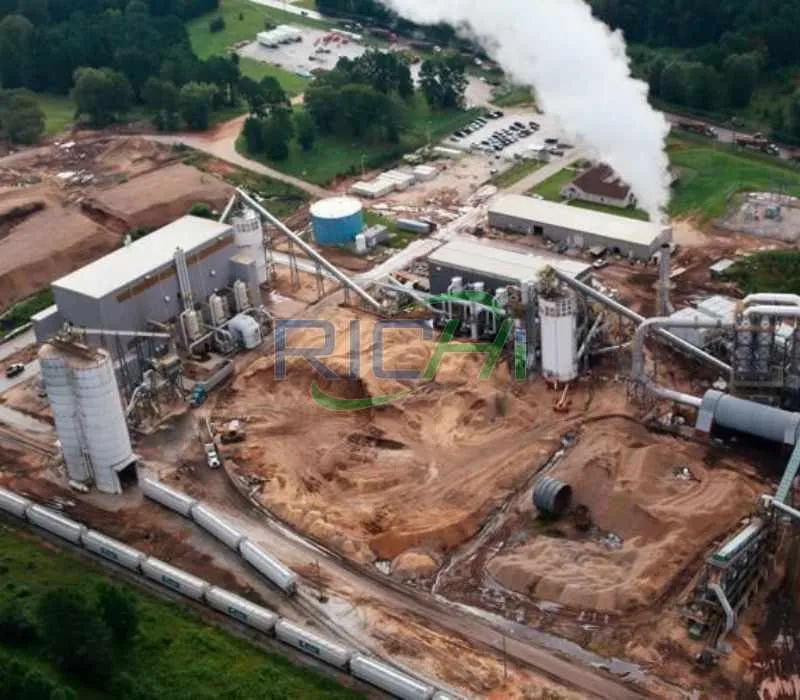
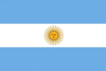
wood pellet plant for sale Argentina
The project uses logs as raw materials, with an output of 12-15 tons per hour. The project investment is approximately US$1.53 million.

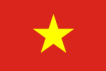
complete wood pellet plant for sale vietnam
The project uses wood chips as raw material, with an output of 15 tons per hour. The project investment is approximately US$1.14 million.
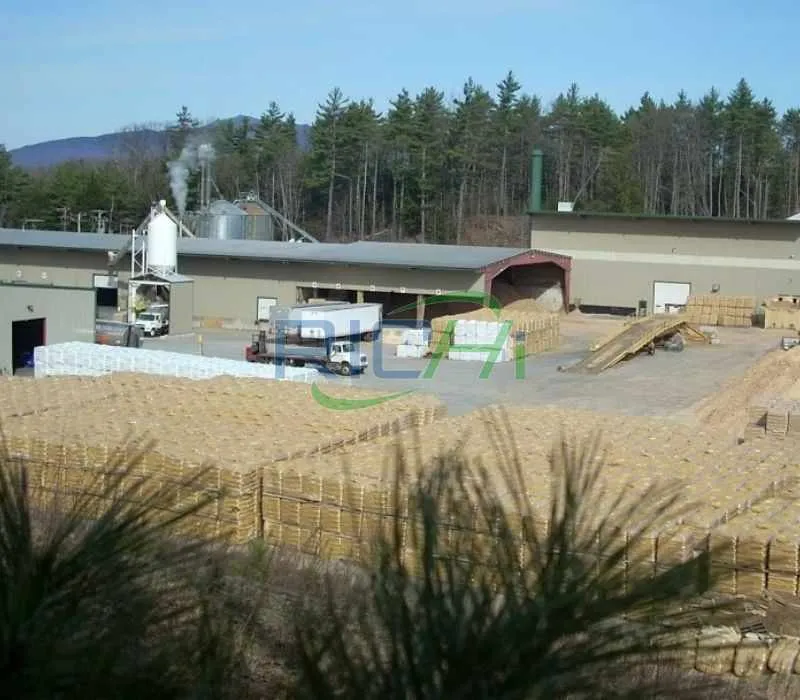
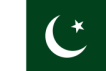
complete wood pellet plant for sale Pakistan
The project uses wood scraps as raw materials, with an output of 10 tons per hour. The project investment is approximately US$480,000.

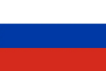
complete wood pellet plant for sale Russia
The project uses logs and wood chips as raw materials, with an output of 15-20 tons per hour. The project investment is approximately US$1.78 million.

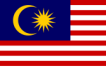
complete wood pellet plant for sale Malaysia
The project uses logs as raw materials, with an output of 10 tons per hour. The project investment is approximately US$720,000.
case studies
From customizing production lines to streamlining entire operations, our solutions have made a tangible impact on our customer’s bottom line. Explore our case studies to see how we’ve solved businesses unique challenges.

【case 1】complete wood pellet plant for sale South Africa
This is a South African biomass pellet fuel project. The main construction content includes biomass pellet fuel production facilities, auxiliary facilities and public works, and all existing production workshops and offices are used.
The total investment of the project is US$110,000, with a total area of 3,000m2 and a total construction area of 2,071m2. After the project is put into production, it will have an annual production scale of 20,000 tons of biomass pellet fuel.
The complete wood pellet plant project has a staff of 10 people, 300 days of production time throughout the year, 7,200 hours throughout the year, and an investment payback period of 2.5 years. The economic and technical indicators of the project are shown in the table below.
No. | Item | QTY |
1 | Production scale | |
(1) | Biomass pellet fuel | 20,000t/a |
2 | Operation days per year | 300d/7200h |
3 | Main raw and auxiliary materials | |
(1) | Miscellaneous wood | 16610t/a |
(2) | Peanut shell | 2300t/a |
(3) | Straw | 1150t/a |
4 | Consumption of public works | |
(1) | Water | 150m3/a |
(2) | Electricity | 2.8 million kW·h/a |
5 | Total factory staff | 10 people |
6 | Plant area | 3000m2 |
7 | Total building area | 2071m2 |
construction content
The composition of this complete wood pellet plant project is shown in the table below.
Engineering Category | Engineering Name | Engineering Content |
Main Engineering | Production Workshop | 1, 1F, building area 2000m2. 1 crusher (chipper), 1 pulverizer, 3 granulators, 4 belt conveyors are installed. Mainly used for crushing (chipping), pulverizing, granulating and other processes. |
Supporting Engineering | Raw Material Area | This project sets up a raw material area in the southwest corner of the production workshop, covering an area of 200m2. |
Finished Product Area | This project sets up a finished product area in the southeast corner of the production workshop, covering an area of 200m2. | |
Office | The office is located on the west side of the production workshop, covers an area of 50m2, and is mainly used for production and operation management. |
General layout
Layout plan
The plant area of this project covers an area of about 3000m2, including 2000m2 of production workshop, 50m2 of office, 21m2 of power distribution room, and 929m2 of other roads and greening. The production workshop is located on the north side of the plant area, and the office is located on the west side of the production workshop.
The finished product area and raw material area are set up inside the production workshop, and no structures are required. The total length of the production workshop is 50m and the width is 40m. The terrain of the project site is flat.
This project has made a relatively reasonable distribution of the plant buildings based on the geographical location characteristics, topography, and meteorological conditions of the project.
The plant area of this complete wood pellet plant project is divided into production area and living area according to function, and the specific distribution is as follows:
- (1) Production workshop: one workshop, with an area of 2000m2, located on the north side of the plant area.
- (2) Office and living area: mainly one office, located on the west side of the production workshop, with an area of 50m2, used for production and operation management.
- (3) Road system planning: Based on the requirements of convenient transportation, the internal roads of the factory area are reasonably arranged to form a complete road system. Due to the small flow of people and goods, the existing roads and entrances and exits can meet the production needs of this project.
Rationality analysis
- (1) The dominant wind direction in the area where this project is located is S (south wind), the living area is not downwind of its dominant wind direction, and the exhaust gas generated during the production process is small, which has little impact on the office and living area.
- (2) The main noise of this project comes from the noise generated by the operation of crushers, grinders, granulators, belt conveyors, etc. Since the noise sources are all arranged in the production workshop and all noise sources have taken certain shock absorption and sound insulation measures, the impact on the surrounding environment is small.
- (3) The various facilities in the production area of this project are reasonably arranged according to the process flow, and the material transportation is short, which can meet the needs of the material flow and the purpose of fast material transportation.
- (4) The functional areas of this project area are clearly divided into functional areas to meet the requirements of non-production and unrelated personnel entering the production area.
- (5) The layout of this project is compact and can meet the requirements of saving land.
The project has clear divisions, and the general layout meets the smoothness of the process flow, reflects the convenience of material transportation, simplifies the transportation of materials within the factory area, and facilitates production.
After taking effective control measures, the impact of production dust and equipment operation noise on the office and living areas is relatively small; the general layout is basically reasonable. The main buildings of this project are shown in the table below.
No. | EngineeringName | Length×Width×Height | Building Area (m2) | Structure | QTY |
1 | Production Workshop | 50m×40m×8.0m, 1F | 2000 | Steel Structure | 1 |
2 | Office | 10m×5m×3.5m, 1F | 50 | Steel structure | 1 |
3 | Power distribution room | 7m×3m×3.5m, 1F | 21 | Steel structure | 1 |
Total | 2071 |
Main raw and auxiliary materials and power consumption
The main raw and auxiliary materials and power consumption of this complete wood pellet plant project are shown in the table below.
No. | Name | Annual Consumption |
I. Raw Materials | ||
1 | Miscellaneous Wood | 16610t/a |
2 | Peanut Shell | 2300t/a |
3 | Straw | 1150t/a |
2. Power | ||
1 | Water | 150m3/a |
2 | Electricity | 2.8 million Kw·h/a |
Main equipment
The main equipment of this project is shown in the table below.
No. | Equipment Name | Model | QTY | Purpose |
1 | Crusher (chipper) | PDJ50*4 | 1 | Crushing (chipping) |
2 | Crusher | PDJ65*6 | 1 | Crushing |
3 | Pelletizer | JL-Ø319*5 | 1 | Pelletizer |
4 | Belt Conveyor | / | 4 | Conveyor |
5 | Dust Collector | / | 2 | Waste Gas Treatment |
Public works
(1) Power supply:
The power supply for this project is provided by the local power supply station. The annual power consumption of this project is about 2.8 million kW·h. A new 250KVA transformer is installed to meet the production and living needs.
(2) Water supply:
The water for this project is provided by the local water supply network. Relying on the existing workshop water supply network system, it can meet the production and living needs. The water used in this project is mainly domestic water, with a total water consumption of 150m3/a. The project has a staff of 10 people, and the water quota is calculated at 50L/person·d, so the annual water consumption is 150m3/a.
Brief description of the process
This complete wood pellet plant project purchases miscellaneous wood, peanut shells, and straw, which can be stored after crushing, pulverizing, and granulating. The main process flow of this project is as follows:
- Chipping process: Use a wood chipper to cut large pieces of miscellaneous wood into small pieces;
- Crushing process: After the large pieces of raw materials are crushed to 600mm by a crusher, they are directly transported to the granulator;
- Granulation process: The crushed raw materials are put into the granulator for extrusion molding;
- Finished products: The finished products are collected in the finished product area.
【case 2】4T/H complete wood pellet plant for sale Ecuador
This is an Ecuadorian biomass pellet fuel construction project with an annual output of 10,000 tons. The project covers a total area of 9933.33m2, and a new 4t/h biomass pellet production line will be built. After completion, it will produce 10,000 tons of biomass pellets annually.
The total investment of the project is US$370,000. The labor quota of this project is 12 people (including management personnel), and food and accommodation are provided. 330 working days per year and 8 working hours per day.
Construction content and scale
The total area of this project is 9933.33m2, and the total construction area is 4868.3m2. Among them, a new production workshop of 900m2, a raw material yard of 3333.3m2, a finished product warehouse of 420m2, and an office and living area of 200m2 are built.
The project site is fully hardened and equipped with corresponding power equipment and auxiliary production equipment.
The project will build a new 1.5t/h biomass pellet production line, which will produce 10,000 tons of biomass pellets annually after completion. The main construction content of the project is shown in the table below:
Engineering category | Construction content | Scale |
Main Engineering | Production workshop | 1F, 2 rooms, color steel structure, 1 1.5t/h production line, fully enclosed, building area 900m2 |
Storage Engineering | Raw material yard | Occupies an area of 3333.3m2, open-air stacking |
Finished product warehouse | 1F, color steel structure, fully enclosed, building area 420m2 | |
Auxiliary Engineering | Office and living area | 1F, brick-concrete structure, total construction area of 200m2, including office, dormitory, canteen |
Toilet | Dry toilet, brick-concrete structure, construction area of 15m2 | |
Fire water tank | 2 sets, Φ4.5m×3.5m, horizontal section is circular | |
Floor scale | Located at the entrance of the factory, specification 50t | |
Hot air furnace | 1 set, biomass hot air furnace, 900,000 kcal, external dimensions 2.5 m×2 m×1.78m, installed in the production workshop |
Economic and technical indicators of this project
No. | Item | QTY |
1 | Total land area | 9933.33m2 |
2 | Total building area | 4868.3m2 |
(1) | Production workshop | 900 m2 |
(2) | Raw material yard | 3333.3m2 |
(3) | Finished product warehouse | 420 m2 |
(4) | Office and living area | 200m2 |
(5) | Toilet | 15 m2 |
3 | Building density | 49.00% |
4 | Greening rate | 2.01% |
5 | Finished product yield | 85%-90% |
6 | Finished product moisture content | <10% |
Product plan
The product plan for this project is shown in the table below.
Product Name | Output |
Biomass Fuel Pellets | 10000t/a |
Biomass fuel pellets use agricultural and forestry waste (such as straw, sawdust and other crops containing wood fiber) as the main raw materials.
After crushing, mixing, extrusion, drying and other processes, they are made into various shapes (such as blocks, pellets, etc.). They are new clean fuels that can be directly burned. Its physical and chemical properties and combustion performance indicators are shown in the table below.
(1) Product physical and chemical properties and combustion performance indicators
Diameter | Length | Moisture | Ash | Heat value |
3-8mm | 6-30mm | <8% | <1.5% | 4500-4900 kcal/kg |
Specific gravity | Sulfur content | Chlorine content | Nitrogen content | / |
1100-1300kg/m3 | <0.01% | <0.004% | <0.0082% | / |
(2) Basic performance requirements of biomass solid briquette fuel
Item | Pellet fuel | Rod (block) fuel | ||
Herbaceous | Woody | Herbaceous | Woody | |
Diameter or maximum cross-sectional dimension D, mm | ≤25 | >25 | ||
Length, mm | ≤4D | ≤4D | ||
Molding fuel density, kg/m3 | ≥1000 | ≥800 | ||
Moisture content, % | ≤13 | ≤16 | ||
Ash content, % | ≤10 | ≤6 | ≤12 | ≤6 |
Low calorific value, MJ/kg | ≥13.4 | ≥16.9 | ≥13.4 | ≥16.9 |
Crushing rate, % | ≤5 |
(3) Requirements for auxiliary performance indicators of biomass solid briquette fuel
Item | Performance requirements | Item | Performance requirements |
Sulfur content, % | ≤0.2 | Chlorine content, % | ≤0.8 |
Potassium content, % | ≤1 | Additive content, % | Non-toxic, tasteless, harmless, content ≤2 |
Raw and auxiliary materials
Based on the location advantages, the raw materials for the production of biomass fuel in this project are mainly straw, sawdust and other organic matter containing wood fiber from agricultural resources purchased from nearby towns. The main raw and auxiliary material consumption during the operation period of this project is shown in the table below.
No. | Type | Amount | Remarks |
Raw and auxiliary materials | |||
1 | Sawdust, straw | 8000t/a | Moisture content about 16% |
2 | Waste wood | 2000t/a | Mature fruit wood materials shall not be used |
3 | Packaging materials | 400,000 pieces/year | / |
Energy consumption | |||
1 | Water | 292.8m3/a | / |
2 | Electricity | 400,000KWh/a | / |
Main equipment
The main equipment of this project is listed in the table below.
No. | Equipment Name | Main Model or Parameters |
Slicing and crushing section | ||
1 | Slicing and crushing machine | BX116A, blade diameter 630mm, cutting diameter 300mm, production capacity 1.5t/h |
2 | Crusher | MFSP50*60, made of steel plate, widened crushing chamber, thickened blade |
3 | Motorized cabinet | Slicing and crushing integrated motorized cabinet |
4 | Gasoline-powered saw | / |
5 | Circular saw | / |
Pelletizing section | ||
6 | Elevator | TD20/50*10000, wood chips 5t/h, shell made of 2mm carbon steel plate |
7 | Grain level meter | Damping type |
8 | Pellets to be made | 4M3, made of 2mm carbon steel plate, assembled with screws |
9 | Permanent magnet | SDTM50, stainless steel |
10 | Wood pelletizer | MZLH420, gear drive clamp type, stainless steel material = |
11 | Starting cabinet | Pelletizer starting cabinet |
12 | Bucket elevator | Made of 2mm carbon steel plate, production capacity 2-3t/h |
13 | Blower | / |
14 | Hot air furnace | 2.5 m×2 m×1.78m, biomass hot air furnace |
15 | Cyclone dust collector | 2mm carbon plate welding |
16 | Screw conveyor | The shell is 3mm carbon steel plate, the top cover is 2mm steel plate |
17 | Dust removal air network pipe | Made of 1mm carbon steel plate |
Finished product packaging section | ||
18 | Bucket elevator | Production capacity 2.0t/h, shell made of 2mm carbon steel plate |
19 | Finished product warehouse | Made of 2mm carbon steel plate |
20 | Material level device | / |
21 | Automatic bag sewing machine | Gravity type |
22 | Belt conveyor | / |
Reasonable layout
The project is adjacent to a temporary garbage storage point on the north side. The overall layout of the plant is “L” shaped. The area on the north side of the plant is reserved for employee living areas.
The raw material storage area, production workshop, warehouse, and living area are all located in the south side of the site. From west to east, they are arranged as raw material storage area, reserved factory building, production workshop, warehouse, and living area.
- The west side of the project is a ravine.
- The raw material storage area is located at the westernmost side of the south side of the site, far away from the living area, which reduces the incidence of accidental fire accidents and is easy to control after an accident occurs.
- The living area is located at the easternmost side of the south side of the site, in the crosswind direction of the production workshop, reducing the impact of production dust on the living area.
- There are 2 fire water pools in the site, one on the southeast side and one on the northwest side, which can prevent accidents in time.
- The distance between the workshops and the reserved roads on the north and south sides meet the requirements of fire protection distance and sanitary protection, and meet the width requirements for raw materials and finished products entering and leaving the factory.
Therefore, the layout of this project is very reasonable.
Process flow
The construction process of this project can be divided into four stages: preliminary preparation, construction, completion acceptance and completion operation. The construction stage of the project mainly includes the demolition of the original buildings in the factory area, site leveling, foundation engineering, main engineering, site hardening and equipment installation.
This project is a biomass pellet fuel construction project. The main process flow during the project operation period is:
- Put the raw materials in the yard, such as sawdust, straw, etc., into the crusher for crushing, screen and mix, and then enter the crusher for crushing.
- After that, the raw materials are transported to the fully enclosed drum dryer, and the hot flue gas of the biomass hot air furnace is introduced into the induced draft fan for drying.
- The induced draft fan introduces all the sawdust and hot flue gas in the drum dryer into the drying moisture separator. The dryer end facility of this project is processed by the drying moisture separator.
- The dried sawdust is discharged from the drying silo discharge port and sent to the pelletizer, and finally enters the separator to separate the dust and package the finished product.
The drying products of this project use hot air furnaces burning biomass materials. The general characteristics of biomass fuels are high moisture, low ash, high volatile matter, low calorific value, and irregular shape.
At present, the combustion devices developed for the characteristics of biomass fuels are: biomass fuel layered combustion device, biomass fuel fluidized bed combustion device, and biomass fuel diffusion combustion device. In order to meet the requirements of grain drying and ensure good performance, the following general principles should be followed when designing straw burning furnaces:
Simple structure, easy to manufacture, low cost; less labor required, easy operation and maintenance; complete combustion, good flue gas quality, high thermal efficiency; taking into account various uses other than drying and the adaptability of different fuels. The combustion quality depends on the following factors: furnace temperature, combustion time, turbulence and mixing degree in the furnace, air-fuel ratio, and the physical properties of the fuel itself.
Recommended values of main design parameters:
Grate area: 70 pounds of fuel/square foot (70bf/in2-6894.76Pa); furnace volume: 10×grate area; theoretical air volume for corn straw combustion: 505kg air/kg fuel dry weight; excess air coefficient is greater than 0.5, and the optimal value is 1~4.
Some design experience: When the moisture content of the straw is high, the feed rate cannot be too large; if the feed is too much, it cannot be dehydrated, volatilized and burned in time, which will cause incomplete combustion.
The inner wall of the furnace should be made of a material with high reflectivity so that the radiant heat energy reached can be emitted back to the center of the flame to promote combustion.
When the furnace temperature is higher than 800℃, the slag produced after the fuel combustion will melt back, and after melting, it is easy to adhere to the grate, block the ventilation holes, and worsen the combustion condition.
To avoid the above situation, the temperature of the slag before discharge should be controlled below 800℃; the air intake should be sufficient to ensure complete combustion on the one hand and avoid slag melting on the other hand; when possible, it is best to process the fuel, such as flattening and chopping, to expand the contact area between air and fuel and make combustion faster.
【case 3】8T/H complete wood pellet plant for sale New Zealand
Biomass energy is the use of biomass to produce energy. Currently, biomass used as energy is mainly crop straw, forestry and wood processing waste. With the continuous development of my country’s economy, the problem of energy shortage has become increasingly prominent.
Since biomass energy has the significant characteristics of being pollution-free and renewable, the development and utilization of biomass energy is particularly important. In this context, the client of this project, an investor from New Zealand, uses the existing factory building to build a project with an annual output of 20,000 tons of biomass pellets.
The labor quota is 5 people, none of whom are boarded and lodged in the factory area. Work 300 days a year and 8 hours a day.
Main construction content
This complete wood pellet plant project uses the existing factory building for construction. The basic situation is shown in the table below.
Category | Name | Building area/volume | Remarks |
Main engineering | Production workshop | 2500m2 | Use existing factory buildings, including raw material area, production area, transfer material room, finished product silo |
Auxiliary engineering | Office | 60m2 | Use existing |
Product plan and scale
After the implementation of this project, its specific products and production scale are detailed in the table below:
Product Name | Annual Output (tons) | Specifications |
Biomass Pellets | 20000 | Cylinder, length: 30-60mm; particle size: 8mm; density: 0.9-1.1g/cm3; moisture content: less than 8% |
Main raw and auxiliary materials and energy consumption
The main raw and auxiliary materials and energy consumption of this complete wood pellet plant project are shown in the table below.
Type | No. | Material Name | Consumption | Remarks |
Raw and Auxiliary Materials | 1 | Waste Firewood | 15000t/a | Purchased, the moisture content of raw materials is controlled below 20% when purchased |
2 | Forestry Three Residues | 1300t/a | Purchased, including broken branches, etc. | |
3 | Furniture factory scraps | 200t/a | Purchased from outside | |
4 | Straw | 2252t/a | Purchased from outside, including peanut shells, etc. | |
5 | Wood chips | 1250t/a | Purchased from outside, including sawdust, etc. | |
Energy consumption | 8 | Electricity | 1.6 million kWh/a | Local power grid |
9 | Water | 60t/a | Water supply network |
Main production equipment
The main equipment used in this project is detailed in the table below.
No. | Equipment Name | QTY |
1 | Waste Wood Chipper | 1 |
2 | Waste Wood Crusher | 1 |
3 | Wood Granulator | 6 |
4 | Large Angle Conveyor | 12 |
5 | Loader | 1 |
6 | Packaging Machine | 1 |
Process flow
The raw materials of this complete wood pellet plant project are waste firewood, forestry residues, furniture factory scraps, straw, and sawdust. The moisture content of the raw materials will be controlled during the purchase.
- Chipping: After the raw materials enter the site, they are stored in the raw material warehouse. The loader is used to move the waste firewood, wood veneer, thin branches, and furniture factory scraps to the conveyor belt, and then sent to the chipper through the closed belt to be crushed into small pieces of wood. The crushed wood blocks enter the closed material transfer room with the conveyor belt.
- Crushing: Use a loader to move the crushed wood blocks, straw, and sawdust to the conveyor belt and send them to the crusher for crushing. The crushed materials enter the closed material transfer room through the conveyor belt.
- Granulation: Use a loader to add the materials to the auger screw conveyor, and send them to the pelletizer through the conveyor, and press them into shape in the pelletizer. During the extrusion process, the friction between the machine and the biomass raw materials will generate heat, which softens the lignin contained in the raw materials and acts as a binder.
- Cooling: The formed materials are transported to the finished product warehouse via a conveyor belt for natural cooling. The cooled finished products are packaged according to customer needs, and unqualified products can be returned to production as raw materials.
【case 4】12.5T/H complete wood pellet plant for sale Thailand
This is a Thai wood pellet project with an annual output of 30,000 tons. The total investment of the project is US$580,000, covering an area of 5,000 square meters and a construction area of 5,000 square meters.
The main equipment used in the project includes pelletizers, crushers, pulverizers and other equipment. The project has 5 employees, working 8 hours a day and 300 days a year. The electricity used in the project is all supplied by the local municipal power grid, and no generators are required.
Construction Content
The main construction content of the project is detailed in the table below:
No. | Engineering Name | Engineering Content | Scale and Purpose |
1 | Main Engineering | Production Workshop | Located on the north side of the project, with a construction area of about 1500m2, it is mainly a production workshop, mainly for crushing and granulation processes. |
2 | Auxiliary, Storage and Transportation Engineering | Raw Material Stacking Area | Located on the southeast side of the project, with a construction area of about 800m2, it is mainly used for raw material stacking. |
Finished Product Warehouse | Located on the southwest side of the project, with a construction area of about 800m2, it is mainly used for finished product stacking. | ||
Office Area | Located in the southeast of the project, it is mainly used for staff offices and covers an area of about 30m2. |
Product output
This project has a total of 5 wood pellet machines, each with a production capacity of 2.5t/h and a production time of 2400 hours/year. After calculation, the production equipment of this project can meet the production capacity requirements of this project.
In the actual production process, the product output is adjusted according to the impact of orders. Therefore, the production equipment of this complete wood pellet plant project is matched with the production capacity.
No. | Product Name | Specifications | Annual Output | Maximum Reserves |
1 | Biomass Molding Pellets | Φ8mm | 30,000 tons | 10,000 tons |
Main raw materials/auxiliary materials
No. | Raw material name | Form | Annual usage | Usage process | Maximum storage capacity |
1 | Wooden scraps | Solid | 20,000 tons | Raw material | 10,000 tons |
2 | Bamboo waste | Solid | 10,000 tons | Raw material | 5,000 tons |
Material balance
Input (tons/year) | Output (tons/year) | ||
Wooden scraps | 20000 | Biomass pellets | 30000 |
Bamboo waste | 10000 | ||
Total | 30000 | 30000 |
Main production equipment or facilities
No. | Equipment Name | QTY | Remarks |
1 | Wood Granulator | 5 | Granulating (Pressing Forming) |
2 | Shredder | 1 | Crushing |
3 | Crusher | 2 | Crushing |
4 | Bag dust collector | 3 | Dust collection |
5 | Feeder | 3 | Feeder |
6 | Conveyor belt | 6 | Conveyor |
7 | Automatic packaging machine | 1 | Packaging |
Process description
- Crushing: Use a forklift to put the materials temporarily stored in the raw material storage area into the hopper, and the materials enter the crusher for crushing to obtain crushed materials with a particle size of less than 5mm;
- Compression molding: The crushed materials are transported to the pellet machine through a closed conveyor belt. After being pressed by the pellet machine, a biomass pellet product with a diameter of 8mm and a length of about 20~40mm is obtained;
- Storage: The biomass pellet product is transported to the silo for storage through a closed conveyor belt;
- Packaging: The pellet product after compression molding is bagged and packaged after being discharged from the silo outlet.
Plant layout
The plant layout of this complete wood pellet plant project is based on the general principles of process requirements and overall layout, combined with the characteristics of terrain, and tries to save land as much as possible while meeting production and transportation conditions, and strives to be compact in layout and improve site utilization efficiency.
The production area, raw material area, and product area of this project are clearly distributed, which is convenient for production management and product storage.
The layout design of the plant and plant meets the design specifications, has convenient transportation, and reasonable layout, which can meet the project production and environmental protection requirements.
【case 5】25 t/h complete wood pellet plant for sale United States
Seizing the market opportunity, the project is for American customers to build an annual production of 60,000 tons of biomass fuel project.
The total investment of this project is 820,000 US dollars, covering an area of 2,576 m2, and the construction includes production workshops, warehouses and other supporting facilities. The project has 15 employees, one shift, 8 hours per shift, and 300 days of work per year.
Project construction content and scale:
The complete wood pellet plant project will build 2 production workshops, warehouses and other supporting facilities for biomass fuel production.
The construction content includes: the construction of 2 production workshops with a total area of 900 m2, 6 offices with a total area of 100 m2, a warehouse of 200 m2, and supporting facilities, and supporting the construction of environmental protection, water supply and drainage, power supply and other auxiliary facilities; purchase of crushers, pulverizers, pellet machines and other equipment.
The construction process mainly includes: foundation engineering, main engineering, equipment installation, decoration engineering, engineering acceptance to use, etc. After the completion of the project, the annual production capacity will reach 60,000 tons. The main engineering content is shown in the table below.
No. | Category | Engineering Name | Engineering Content and Scale |
1 | Main Engineering | Production Workshop | 2 buildings, each with a biomass fuel production line, a total of 2 production lines, building area of 900m2, installed with crushers, pulverizers, pellet machines, etc., production equipment, forming an annual production capacity of 60,000 tons of biomass fuel |
2 | Auxiliary Engineering | Office | 6 rooms, 1 floor, building area of about 100m2, used for office and staff rest |
3 | Storage and Transportation Engineering | Warehouse | Raw material area 100m2, finished product area 100m2 |
4 | Public Engineering | Water supply | From the local water supply network |
Drainage | Rainwater and sewage are separated, and rainwater is discharged into nearby ditches; domestic sewage is used for fertilizing surrounding farmland after passing through underground sewage treatment facilities, and is not discharged externally | ||
Power supply | Introduced from the local power grid | ||
5 | Environmental Protection Engineering | Wastewater treatment | The domestic sewage of the project is used for fertilizing the surrounding farmland after passing through the underground sewage treatment facilities, and is not discharged |
Waste gas treatment | The crushing and grinding dust is collected by the air collecting hood and treated by the bag dust collector and then discharged at high altitude through the 15m high 1# exhaust pipe | ||
Noise control | Prioritize the use of low-noise equipment, vibration reduction and noise reduction; strengthen the daily maintenance of equipment; take sound insulation measures in the production plant | ||
Solid waste treatment | Domestic garbage is collected by garbage bins and transported and handled by the village sanitation department; dust collected by dust collector is reused in production |
Product plan
The output of the main products of this complete wood pellet plant project is shown in the table below:
No. | Product Name | Designed Production Capacity | Annual Working Time |
1 | Biomass Fuel | 60,000 t/a | 300d |
Biomass fuel industry, elemental analysis list
Item | Indicator requirements |
Total moisture | ≤15% |
Ash | ≤10% |
Volatile matter | ≥60% |
Total sulfur | ≤0.1% |
Low calorific value | ≥13.4MJ/kg |
Raw and auxiliary materials
The raw and auxiliary materials and energy consumption of this project are shown in the table below:
No. | Name | Consumption | Remarks |
1 | Waste wood | 50010t/a | Purchased locally, mainly waste scraps and tree waste from furniture factories; maximum storage 500t, storage period 3 days |
2 | Straw | 10008t/a | Purchased crop straw from local farmers; maximum storage 100t storage, storage period is 3 days |
3 | Packaging bags | 60,000 pieces/a | Local purchase, maximum storage 6,000 pieces |
4 | Water | 330m3 | Local water supply |
5 | Electricity | 100,000Kw·h | Local power supply |
Main production equipment
The main equipment of this project is shown in the table below:
No. | Equipment Name | QTY |
1 | Crusher | 2 |
2 | Wood Grabber | 6 |
3 | Crusher | 2 |
4 | Pelletizer | 10 |
5 | Scale | 1 |
6 | Scissor machine | 2 |
7 | Transport vehicle | 10 |
8 | Transformer | 1 |
9 | Forklift | 3 |
Main process flow
The main raw materials of this project are waste wood and crop straw. There is no drying process or sawing process. The raw materials are purchased locally.
- Chipping: The raw materials are transported to the raw material warehouse of the project site by car for stacking. The raw materials are sent to the chipper crusher by a wood grabber for preliminary crushing into smaller block materials.
- Crushing: The crushed block materials are sent to the hammer mill crusher by a conveyor for crushing. The particle size after crushing is not more than 7mm.
- Granulation: The crushed materials are transported to the pellet machine and formed into finished products by extrusion. The extrusion process is a physical process. No adhesive is added and no chemical reaction occurs. Except for the connection of the feeding auger and the feed and discharge ports, they are all sealed.
- Packaging and storage: The formed biomass pellets are packaged and stored in the finished product warehouse for sale.
Public works and supporting facilities
(1) Water supply and drainage
Water supply: The water supply of this complete wood pellet plant project is supplied by the local water supply network.
Drainage: This project implements a drainage system with rainwater and sewage diversion. Rainwater is discharged to nearby ditches through the project rainwater pipe network; domestic sewage is used for fertilizing nearby farmland after passing through septic tanks and underground sewage treatment facilities.
(2) Power supply
The power supply for the factory area comes from the local power grid, and the annual power consumption of the equipment is about 100,000 Kw·h.
Plan layout
This project meets the regulations on fire prevention, environmental protection, safety, and sanitation while striving for compact layout and reasonable process.
At the same time, combined with the project composition and site conditions, the gate is located on the village road on the west side of the factory area, the office area is on the north side of the factory area.
The weighing scale is on the south side of the office area, the production workshop is on the south side of the factory area, the warehouse is between the production workshop and the office area, and the rest is cement site.
The flow of people and logistics inside the factory is clearly distributed and does not interfere with each other. The overall plan layout is reasonable.
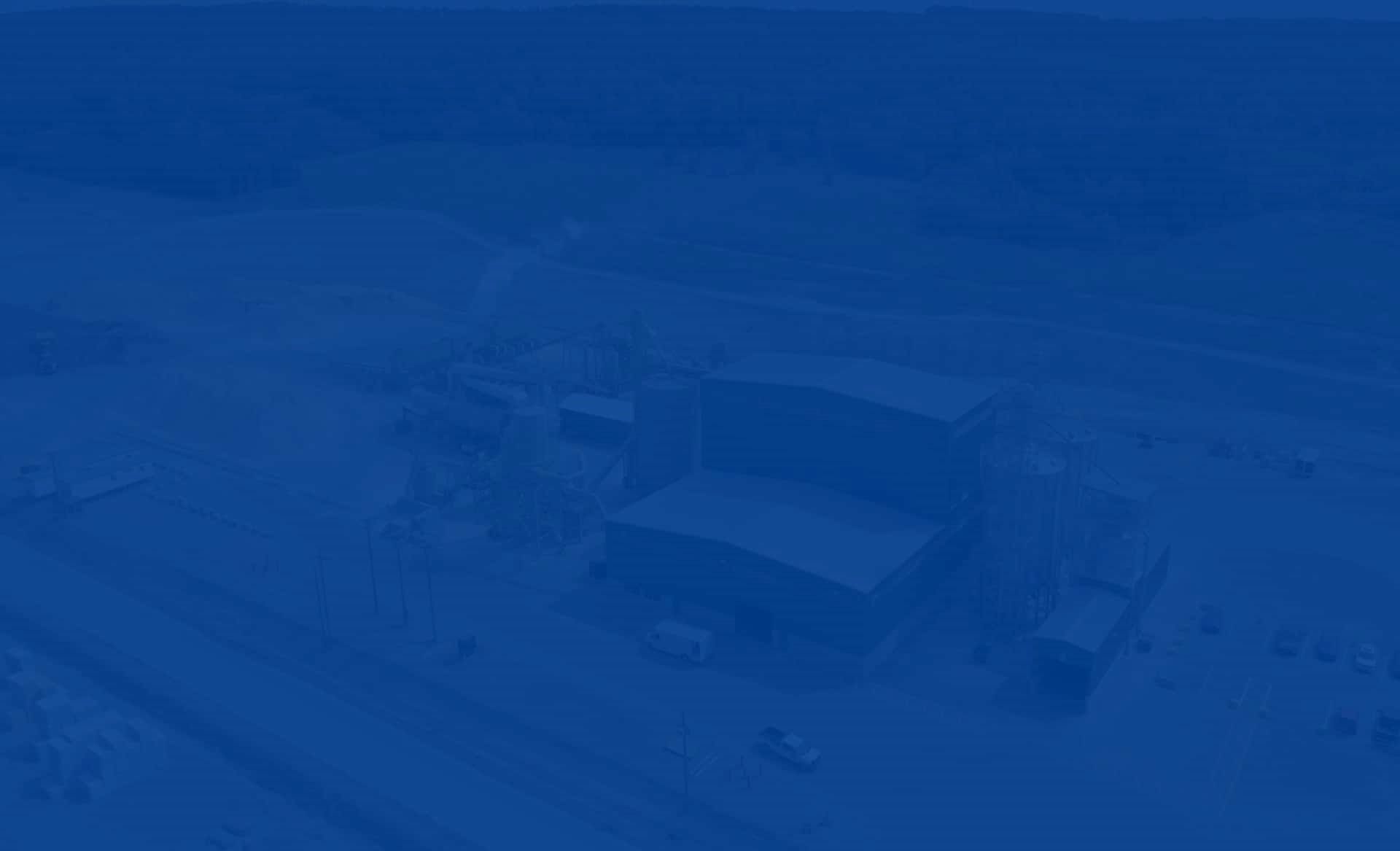
Production capacity of complete wood pellet plant
We provide customized solutions for global customers based on different production scales. Whether you want to build a simple wood pelletizing system or need a turnkey project, we can provide processes and equipment that exceed your expectations.
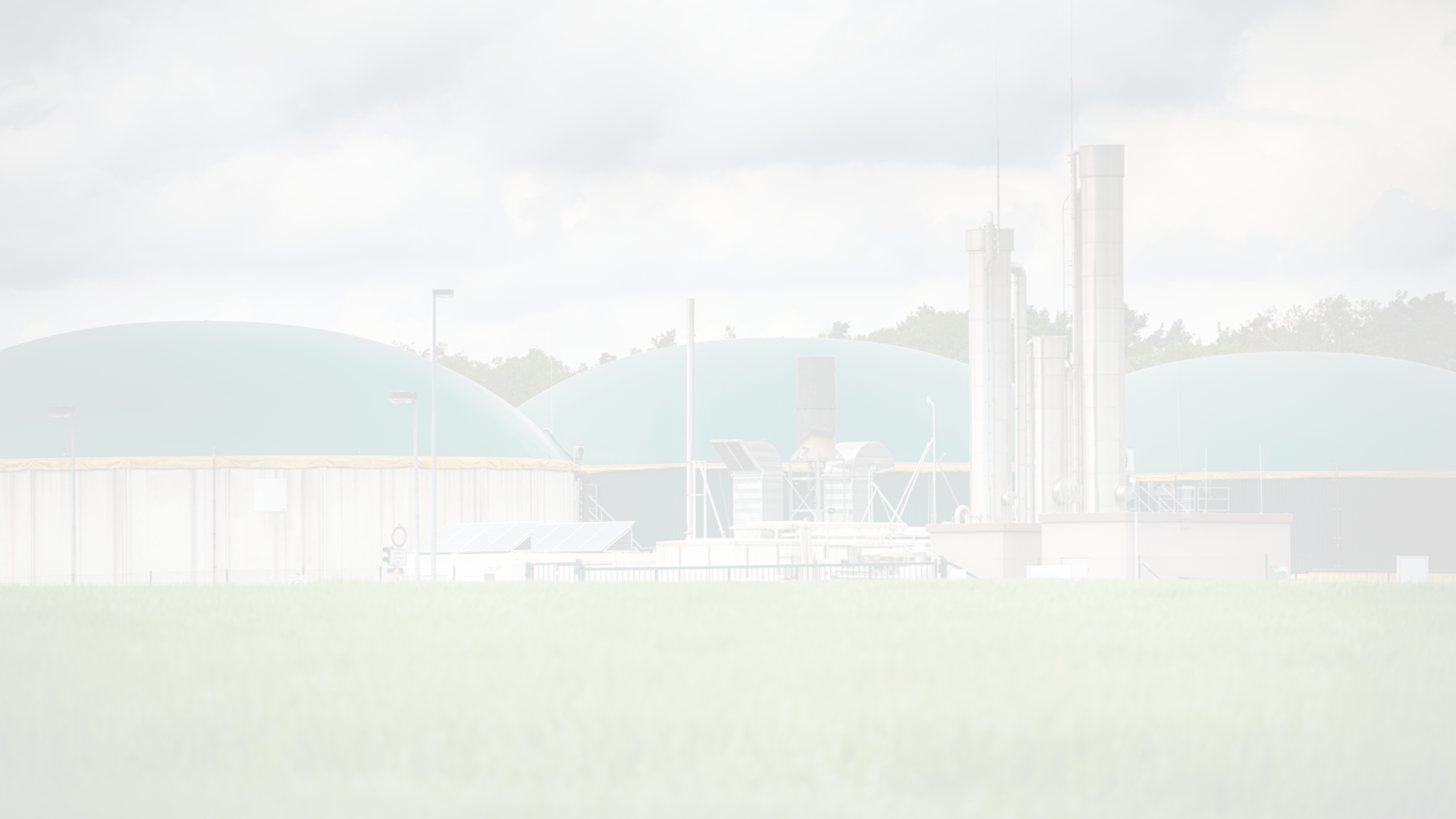
— Richi Machinery —
cost to build a wood pellet plant
The cost of wood pellet plant is usually between $20,000 and $3 million. This is the price of a complete set of wood pellet processing equipment. If you want to calculate the cost to build a wood pellet plant, you also need to add the civil engineering cost, plant cost, packaging cost, personnel cost, water, electricity cost, etc.
Capacity | wood pellet plant cost (USD) |
0.2-0.3 T/H | 20,000-140,000 |
0.3-0.5 T/H | 28,000-160,000 |
1.0-1.2 T/H | 39,000-220,000 |
1.5-2.0 T/H | 46,000-270,000 |
2.5-3.0 T/H | 58,000-350,000 |
3.0-4.0 T/H | 75,000-430,000 |
5.0-6.0 T/H | 130,000-570,000 |
6.0-8.0 T/H | 170,000-690,000 |
10-12 T/H | 240,000-1,100,000 |
12-15 T/H | 370,000-1,430,000 |
15-20 T/H | 430,000-1,850,000 |
20-24 T/H | 570,000-2,100,000 |
higher capacity… | … |

We care about what you need
As your partner, we guarantee highest process reliability and individual solutions that are specifically tailored to the respective requirements and needs of the wood pellet fuel, wood pellet cat litter and animal bedding industries.
We’re committed to helping businesses achieve success by providing reliable industrial wood pellet plant solutions tailored to their unique needs.
Who is suitable to invest in complete wood pellet plant?
Investors who are optimistic about the prospects of biomass energy, wood processing companies, furniture factories, wood recycling companies, traditional energy companies, biomass energy companies, large energy companies, investment institutions, etc. are all suitable for investing in and building wood pellet plants. As long as there are raw materials and budgets, and sufficient market research has been done on the sales area of wood pellets, you can try to invest in and build a wood pellet plant.
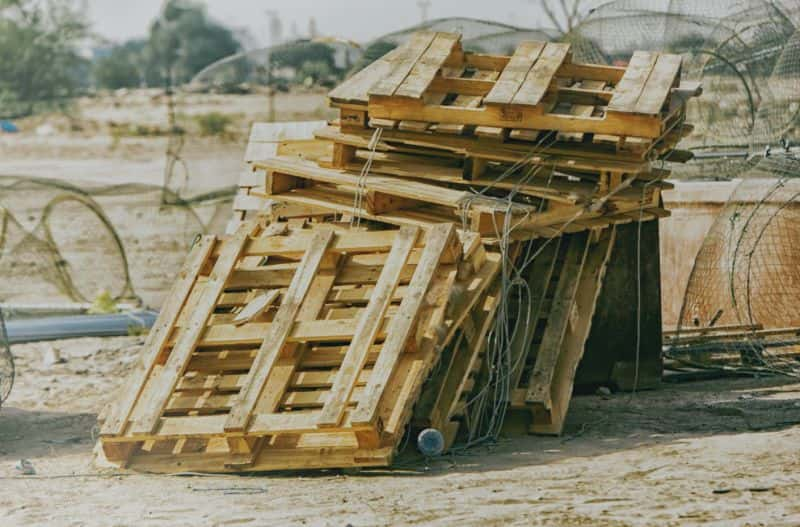
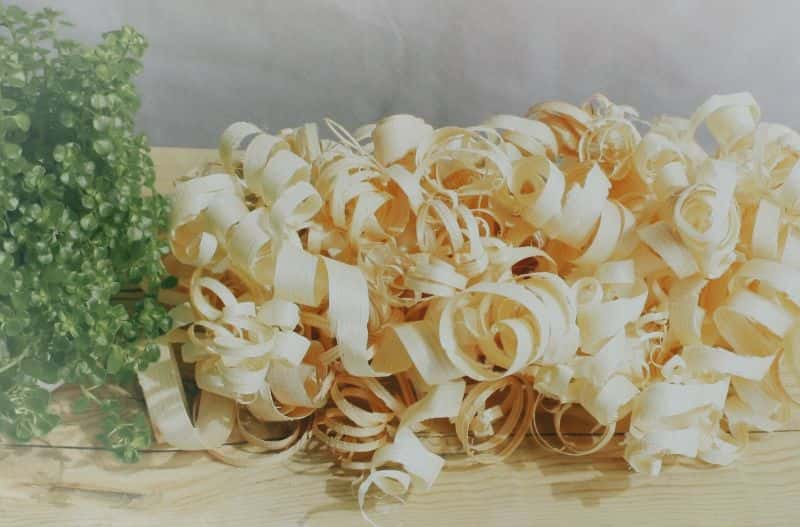
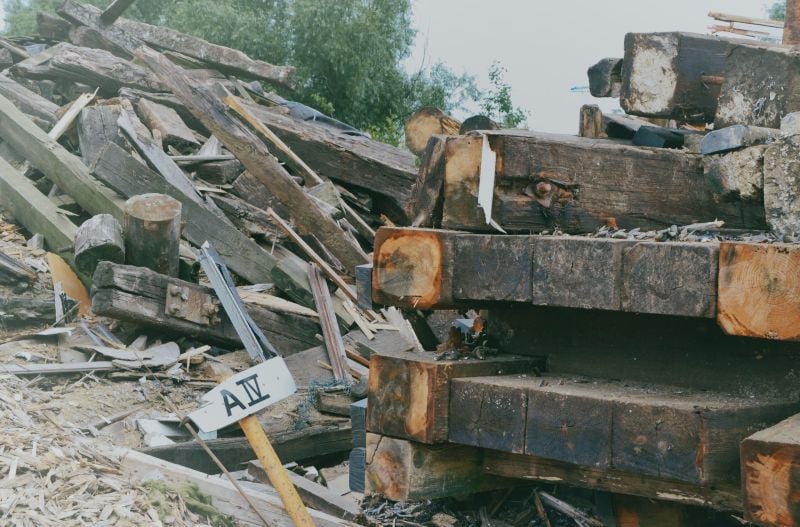
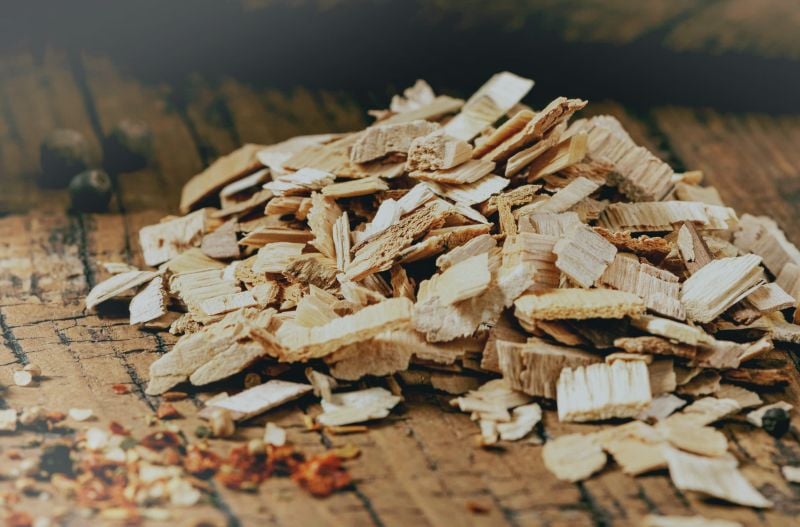

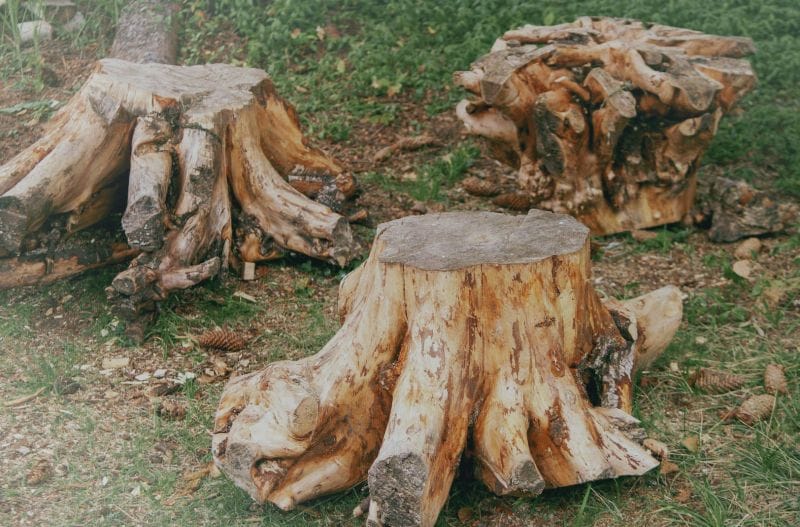
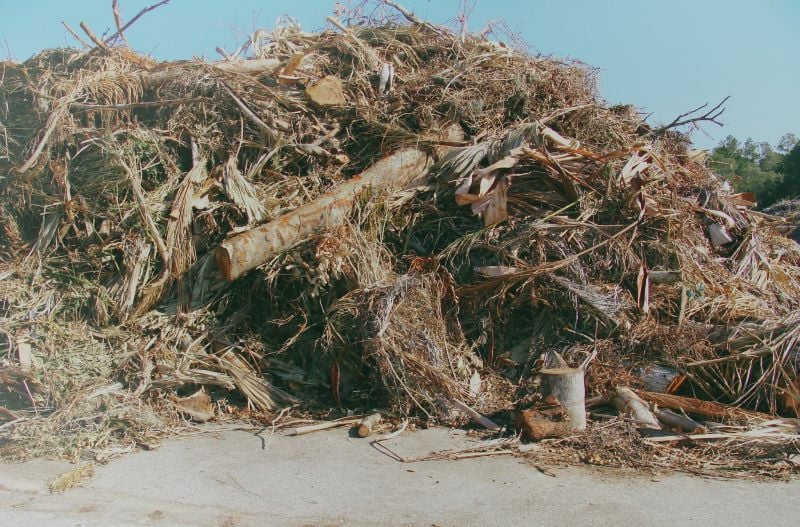
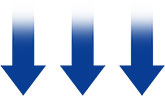
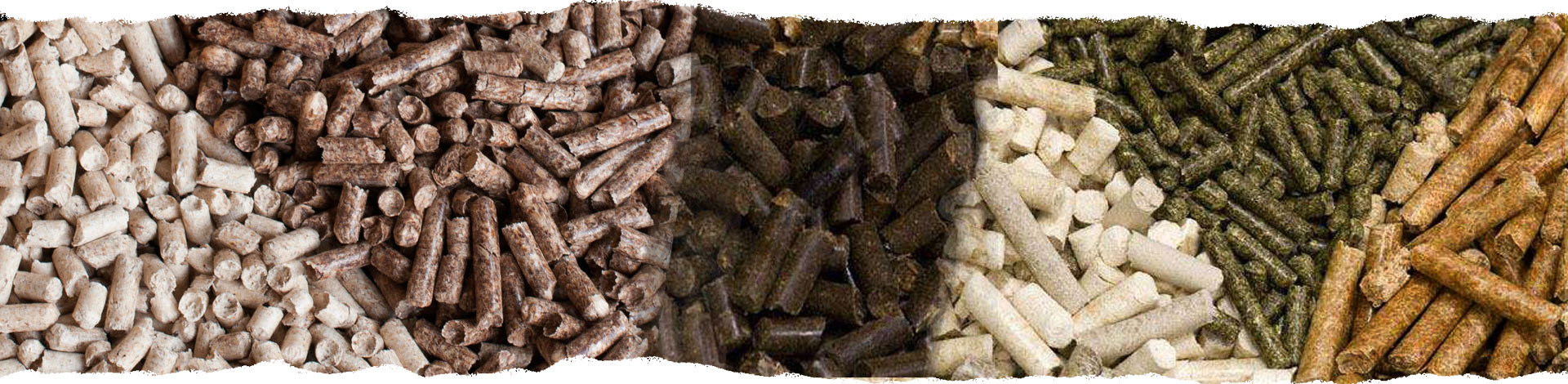
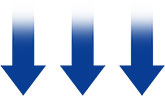
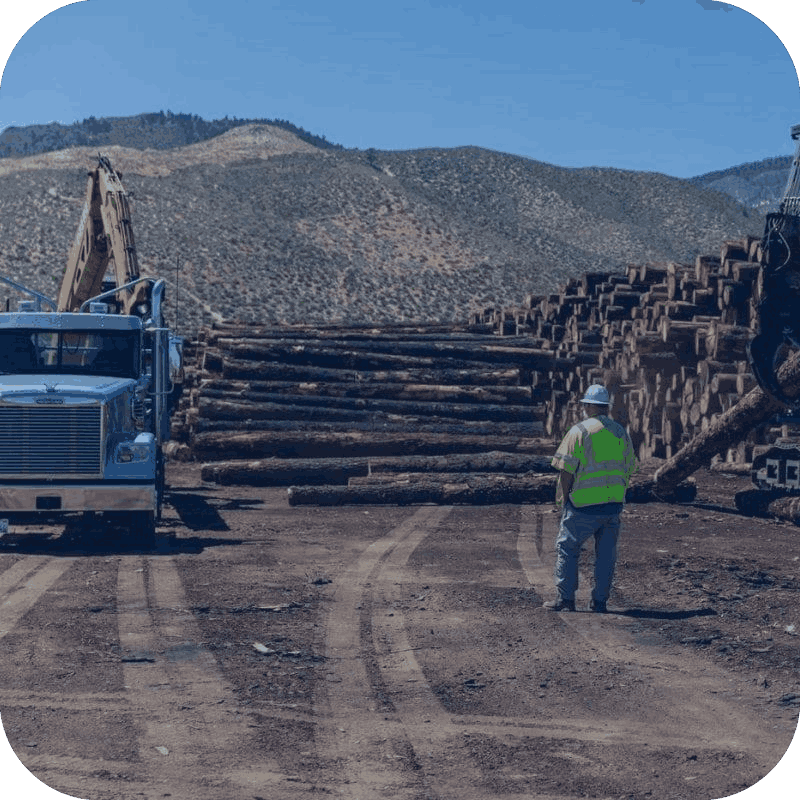
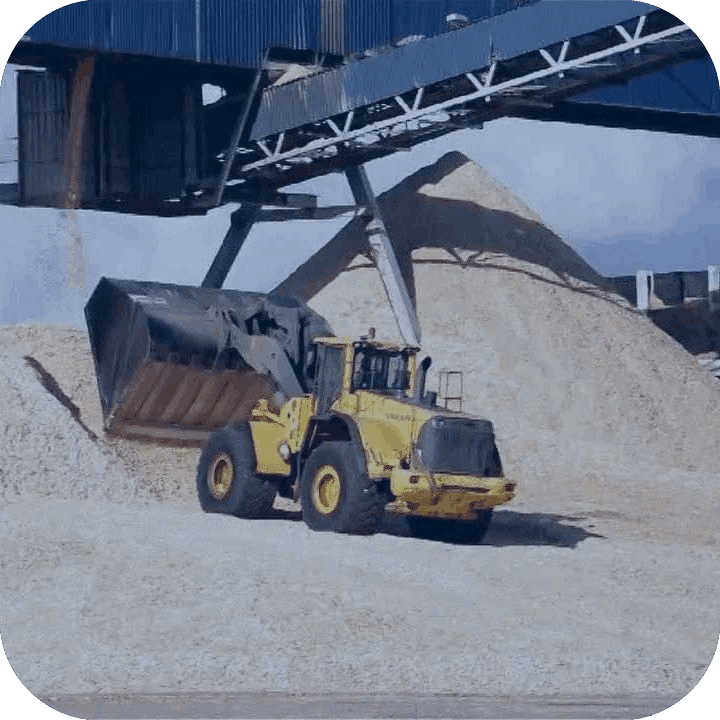
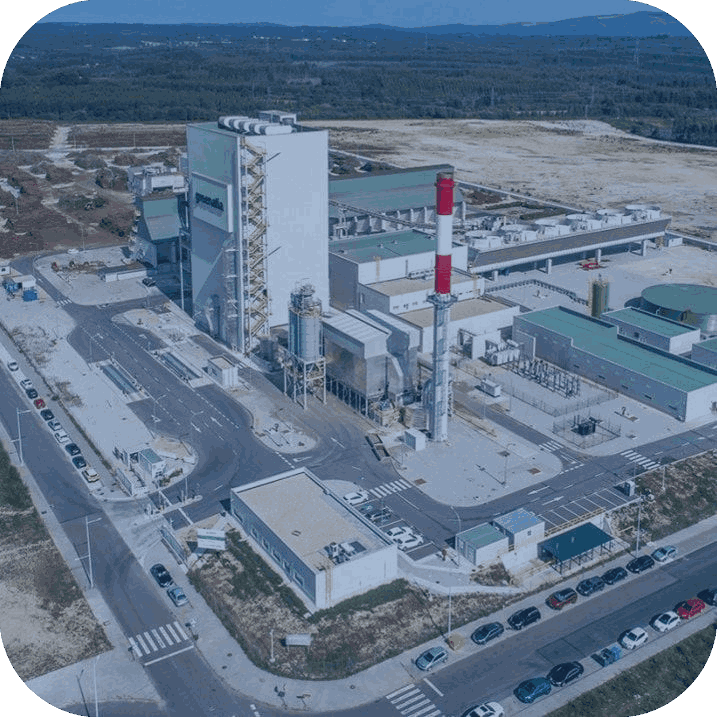
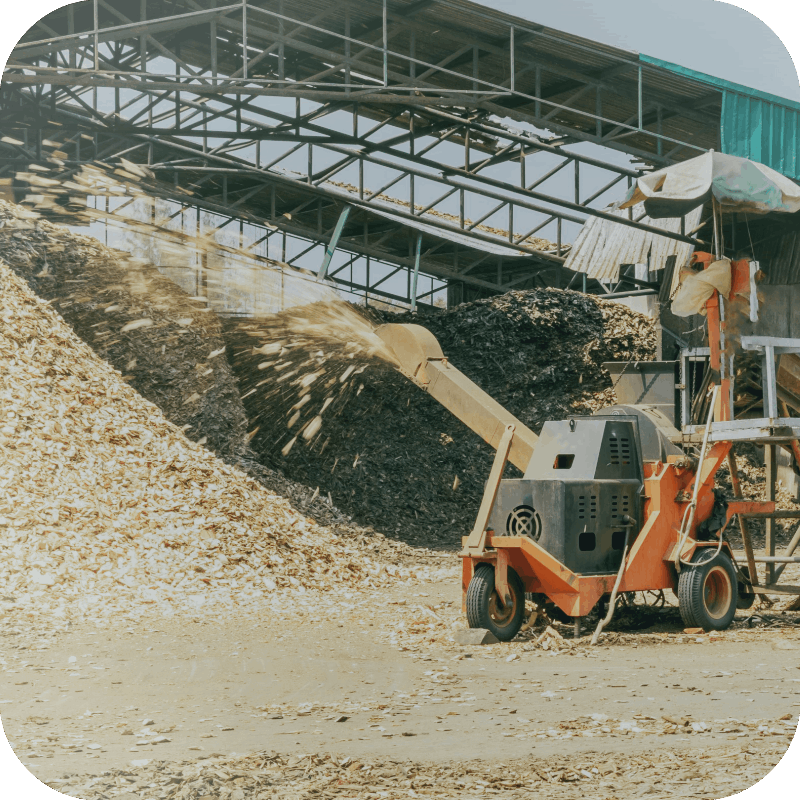
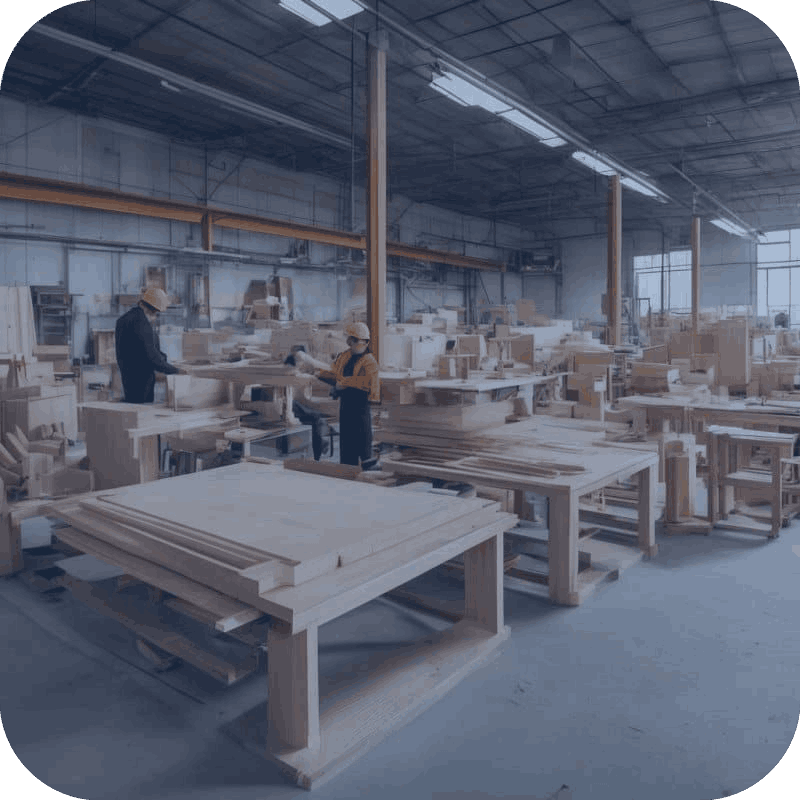
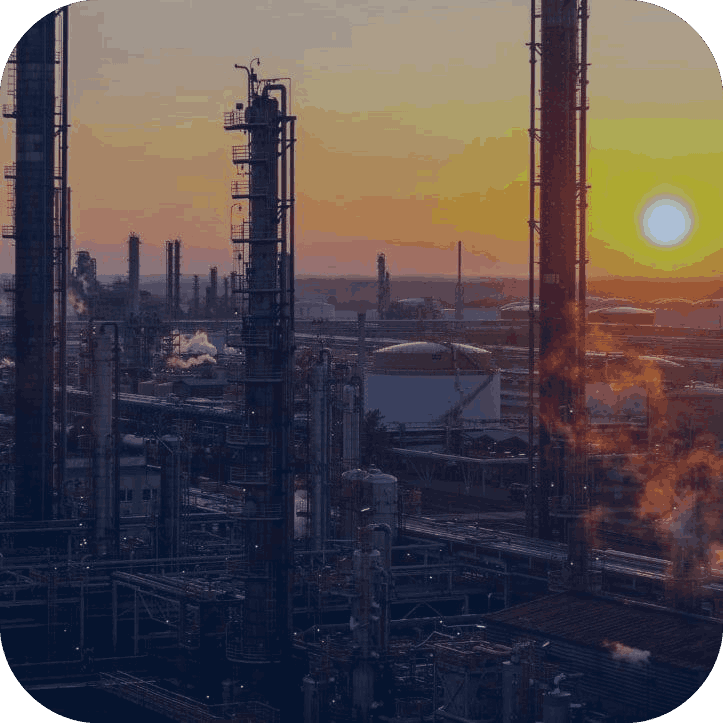
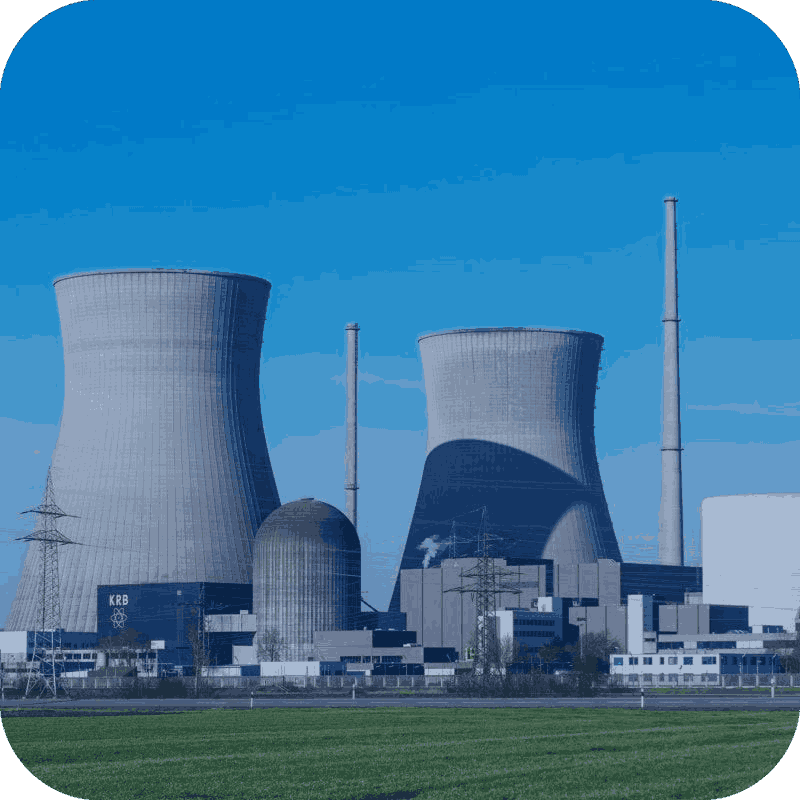
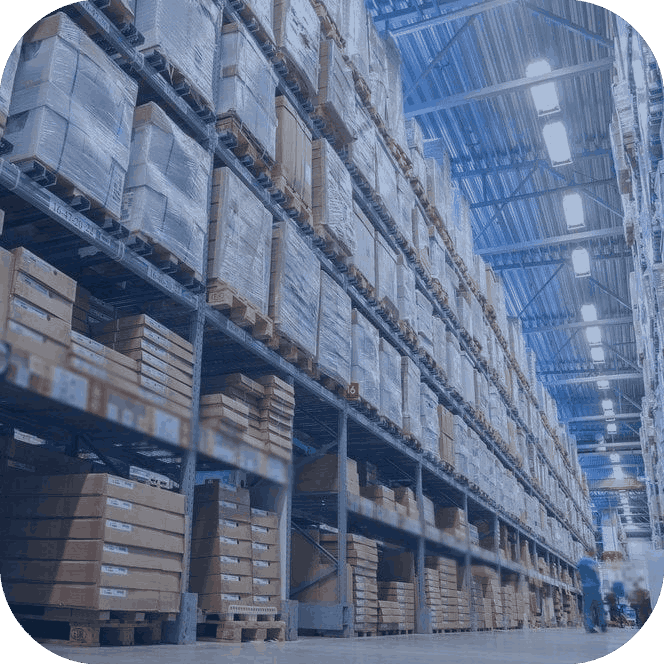
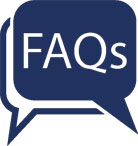
Frequently Asked Questions
What is the capacity of a complete wood pellet plant? Can it meet my needs?
The capacity of a wood pellet plant is usually calculated in tons/hour (0.5~3t/h for small lines, 4-8t/h for medium-sized lines, and more than 8t/h for large lines).
Key considerations: Choose matching capacity based on your raw material supply (such as 500 tons per month) and target market orders to avoid idle or overloaded equipment.
What is the total investment cost of the equipment? What parts are included?
Total cost composition:
Equipment costs (accounting for 60%~70%): crusher, dryer, pellet machine, cooling and packaging line, etc.
Auxiliary costs (accounting for 30%~40%): plant construction, power capacity expansion, environmental protection facilities (such as dust collector).
Example: A small production line of 1t/h costs about 20,000-300,000 US dollars, and a large automated line may exceed 1 million US dollars.
How are wood pellets made?
To create wood pellets, producers remove moisture from incoming wood fibre, grind the fibre into dust, and compress the dust into small cylinders. Heat is applied in this process which causes lignin—a natural polymer found in wood—to act as a glue to hold the compressed particles together. The result is a dry, highly compressed and high-energy-value product that can be easily handled and transported efficiently over very long distances.
What are the requirements for raw materials in wood pellet plants? Is pretreatment required?
Applicable raw materials: wood chips, sawdust, branches (need to be crushed to 3~5mm), some agricultural waste (such as rice husks).
Pretreatment requirements:
The moisture content needs to be adjusted to 12%~20% (too high requires drying, too low requires humidification).
Metal, stone and other impurities must be removed (magnetic separator is recommended).
How is the energy consumption of the complete wood pellet plant? What is the proportion of electricity cost?
Main power-consuming equipment: wood pellet machine (accounting for more than 50% of the total energy consumption), dryer (if necessary).
Electricity cost estimation: Producing 1 ton of pellets consumes about 80~120 degrees of electricity. (Electricity costs are estimated based on local electricity prices.)
Energy saving suggestions: If you want to save energy, you can choose variable frequency motors and waste heat recovery drying systems.
How automated is the complete wood pellet plant? How many workers are needed?
Automation level:
Semi-automatic line: 3~5 workers are needed (operation + inspection).
Fully automatic line: 1~2 workers (monitored by the central control room).
Intelligent functions: Automatic lubrication system and fault alarm can greatly reduce manual intervention.
How to Achieve Success in the Wood pellet plant?
We all know that starting a wood pellet plant requires careful planning and execution. So, in this column, we will cover the essential steps you need to take for a successful venture. From conducting feasibility studies and securing the necessary permits to selecting suitable locations and procuring the right pellet machinery, we will guide you through each stage of the process.
Researching the market and developing a plan
Learning the market demand, competition to determine the feasibility of the implementation of the plan is the basis for the subsequent steps.
Obtaining investment capital
Getting enough capital through self-financing, bank loans or co-operation in various ways.
Choosing the plant site and purchasing the pellet equipment
Finding a suitable location and purchasing the necessary pellet mill is another crucial step.
Obtaining production licenses from relevant authorities
Obtaining the required licenses and certifications is imperative to ensure regulatory compliance.
Developing a reliable supply chain
Addressing logistical and storage issues through supply chain is also crucial.
Conducting effective marketing
Identifying sales channels and establishing a brand image will help the business to succeed.
Is the process for processing wood pellets the same as that for processing other biomass pellets (such as efb, bamboo, Bagasse, Napier Grass)?
Wood Pellet Making Process: Wood→ Log Splitting (optional) → Wood Crushing (optional) → Drying → Pelletizing → Cooling & Sieving → Packaging
EFB Pellets Plant Process: Palm Fiber → Crushing → Drying (optional) → Crushing → Pelletizing → Cooling → Packaging
Bamboo Pellet Pduction Process: Bamboo Waste → Chipping → Crushing → Conveying → Pelletizing → Cooling → Packaging
Bagasse Pellet Plant Process: Bagasse Pretreatment → Drying → Grinding → Pelletizing → Cooling → Packaging
Napier Grass Pellet Production Process: Napier Grass Pretreatment → Drying→ Crushing → Pelleting→ Cooling → Packaging
Above the main pellet manufacturing process of common raw materials. For other biomass materials, we have professional technical team to provide custom-made pellet production plant. We have built a lots of smaple projects of complete biomass pellet line around the world.
As for the turnkey cost of a large wood pellet plant, different equipment selected has different price. Richi Machinery focuses on complete wood pellet plant for sale, and can provide customers with one-stop, complete set of professional solutions to solve the problems of customers. If you are interested in setting up your own pellet manufacturing plant, just tell us your requirements in details and then get your customized wood pellet production plan!
● RICHI MACHINERY
service for complete wood pellet plant
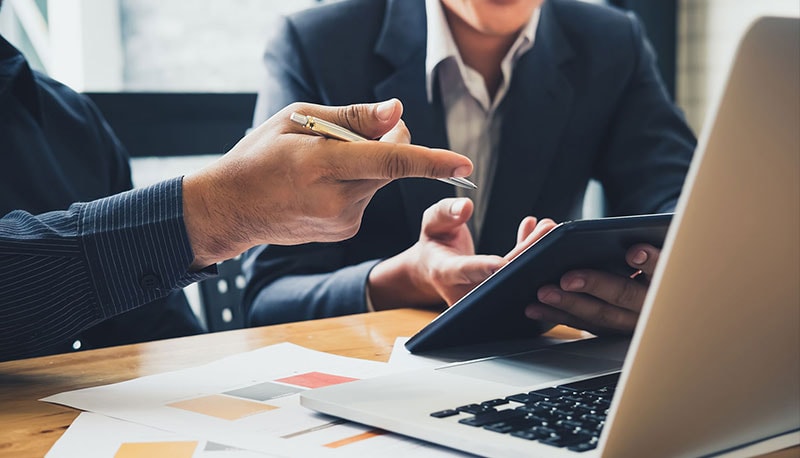
● Consulting
Customer Consultation
We want to have a deep understanding of your industrial process, to know your exact needs of feed, wood, biomass, fertilizer or other pellet processing.

● Design
wood Pellet Plant Design
Based on your unique situation and industrial process, we will tailor complete pellet plant you need, and inform you of every additional detail that could facilitate operation, minimize total cost.
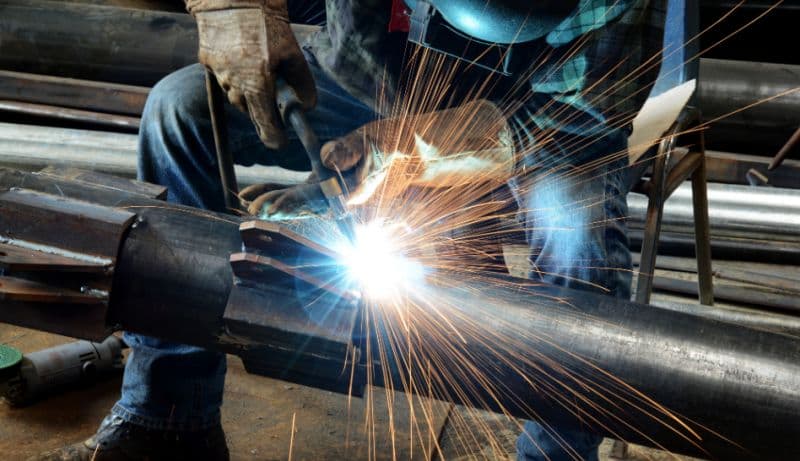
● Manufacturing
Equipment Manufacturing
The critical components of the of the complete pellet production line equipment are built in our own workshops in Asia. Additional equipment is manufactured by our worldwide network of reliable partners.
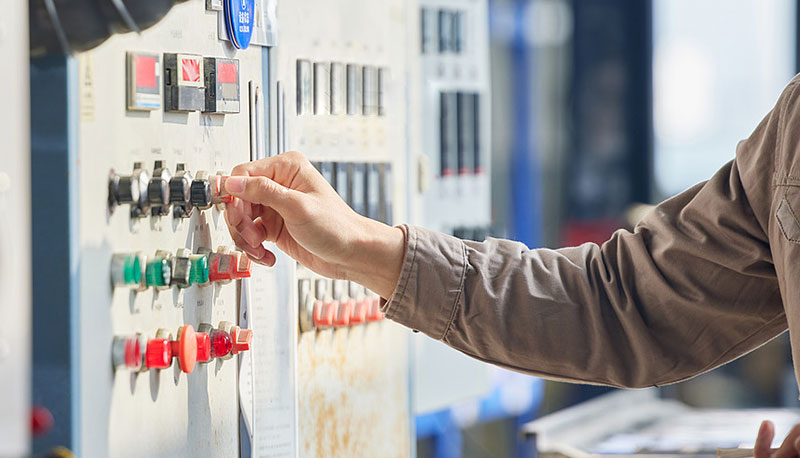
● Testing
Quality Inspection & Testing
Before leaving the factory, all equipment will be inspected by the quality inspection department. We can also provide customers with testing services from a single machine to a complete pellet plant system, and provide you with real actual data for “worry-free use.”
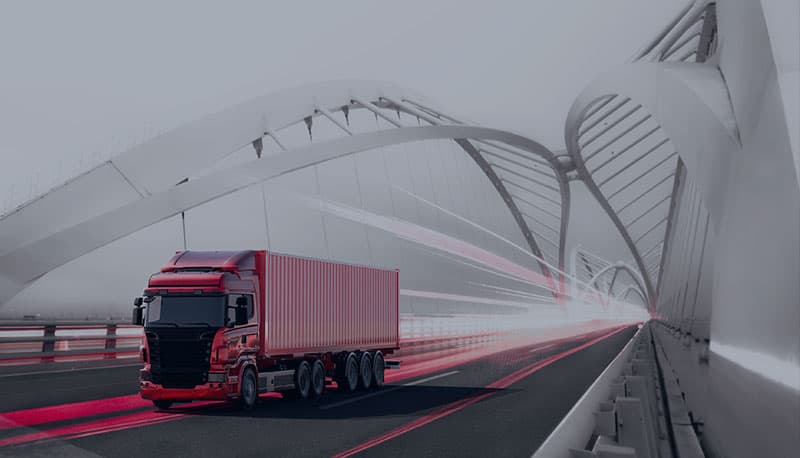
● Delivery
Equipment Delivery
In equipment boxing and packaging, we adopt professional packaging and modular solutions to ensure the safe and non-destructive delivery of wood pellet plant equipment.
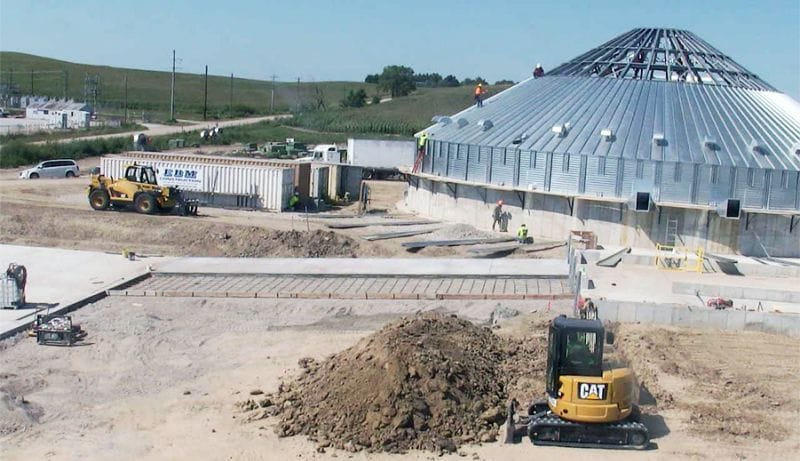
● Installation
Installation & Commissioning
Whether you choose your own subcontractor for the erection phase or you want to install everything together with us, a Richi supervisor will be around to make sure everything is mounted in a safe and thorough way.
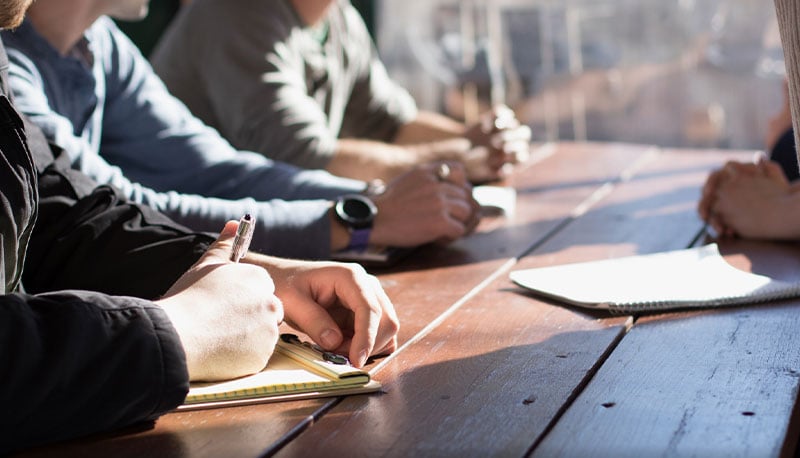
● Training
Staff Training
We provide comprehensive training for the technicians of each wood pellet plant project. We can also continue to provide support for the technicians during latter project operation.
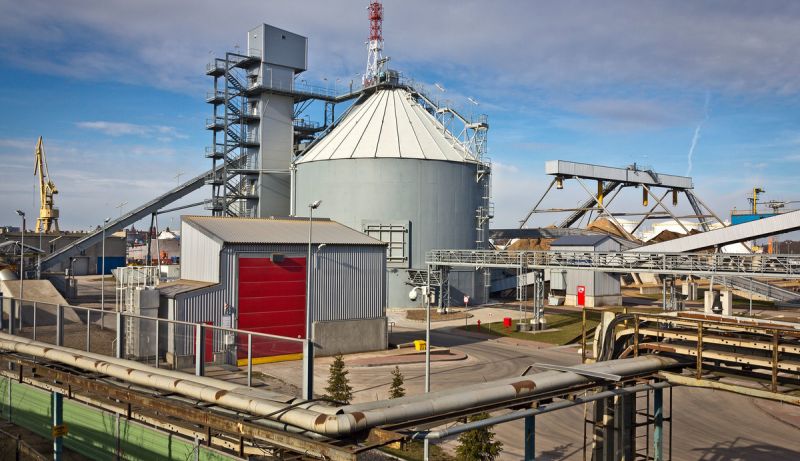
● After-sales
Project Follow-Up
When everything is up and running our Richiers will help you further whenever needed. We are ready to answer your call 24/7.We’ll also visit you regularly to learn about your needs.
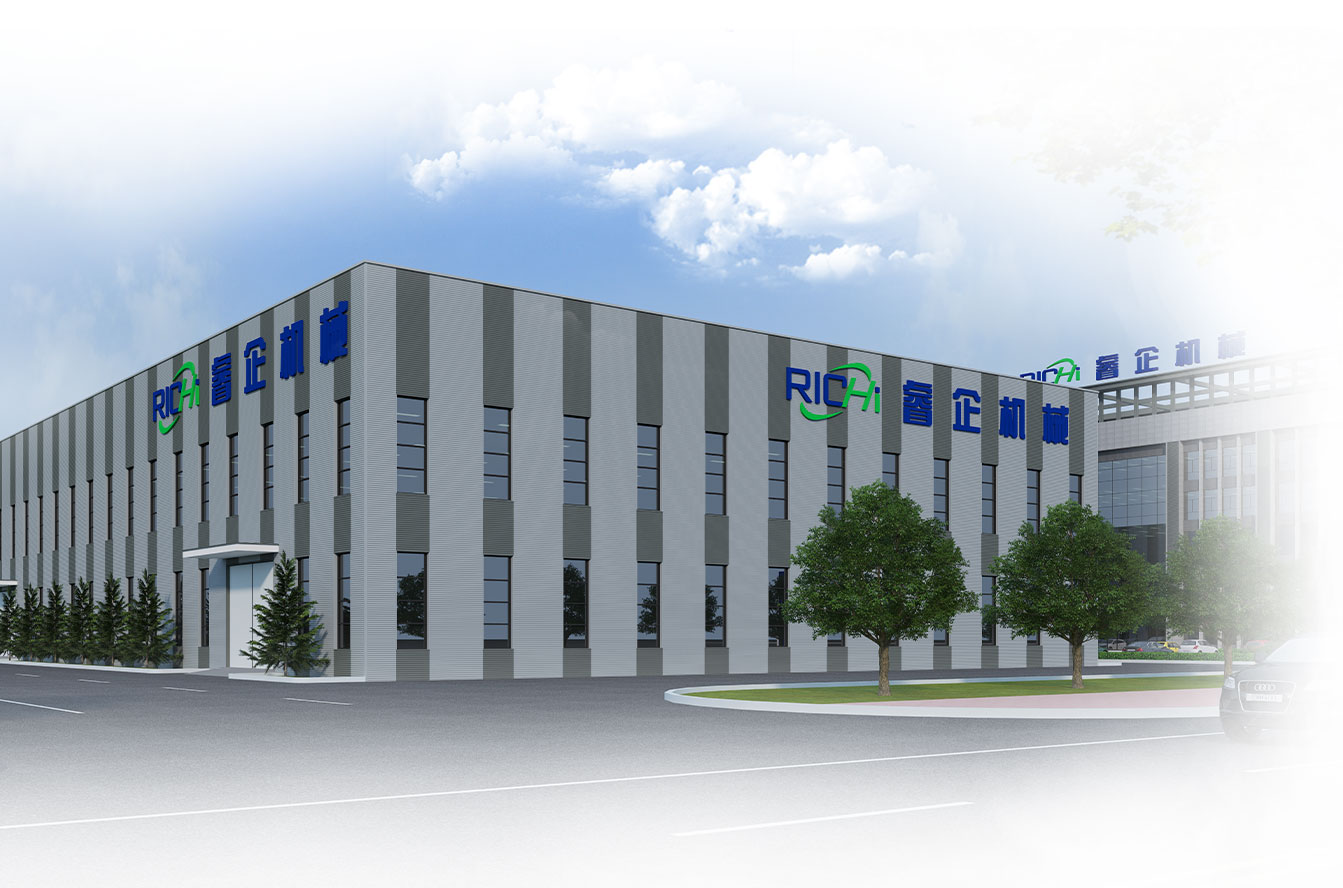
Who we are
RICHI Machinery is one of the world’s leading suppliers of technology and services for the animal feed, aqua feed and pet food industries, also the largest pellet production line manufacturer in China.
Since 1995, RICHI’s vision to build a first-class enterprise, to foster first-class employees, and to make first-class contributions to society has never wavered.
In the past three decades, we have expanded our business to a wide range of areas, including animal feed mill equipment, aqua feed equipment, pet feed equipment, biomass pellet equipment, fertilizer equipment, cat litter equipment, municipal solid waste pellets equipment, etc.

1995
RICHI Established

2000+
Serving More Than 2000 Customers

120+
RICHI Employees

140+
Exported To 140 Countries
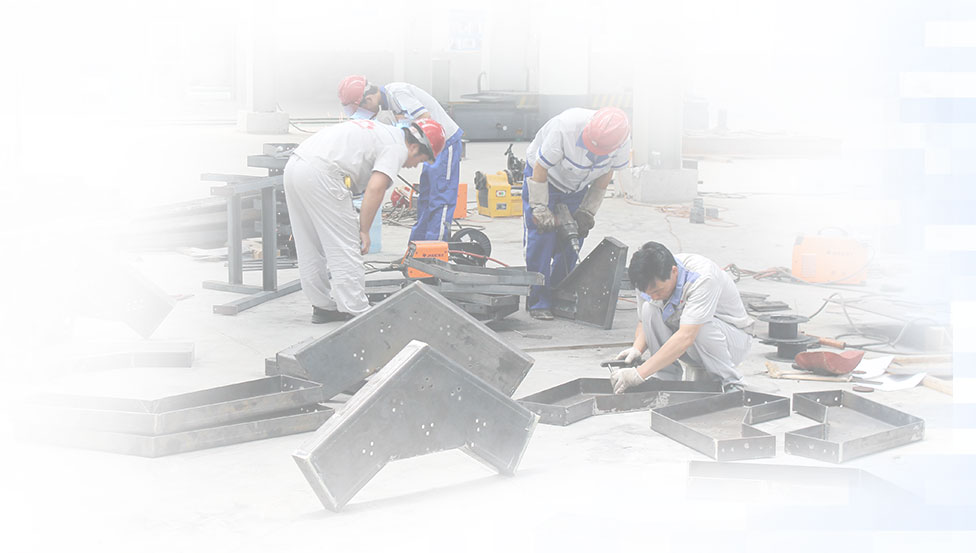