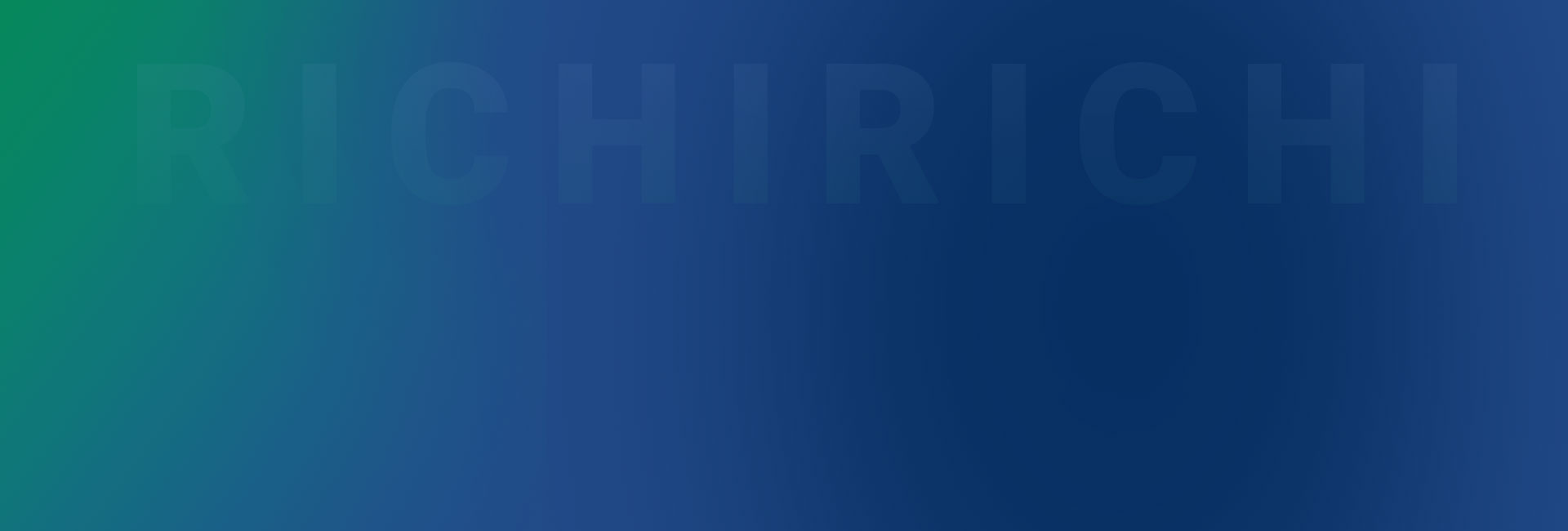
Wood Pellet Processing Plant solution
The wood pellet processing plant is suitable for pelletizing biomass raw materials such as sawdust, chips, shavings, logs, planks, other agricultural and forestry waste. The moisture content of the biomass wood pellets produced is below 10%, and the pellet molding rate is as high as 98%.
Cost: 80,000-500,000 USD
wood pellet processing plant solution
— Richi Machinery —
The low investment high return wood pellet processing plant consists of a variety of supporting systems, in addition to the crushing and pelletizing system, it also includes: conveying system, drying system, cooling system, dust removal system, packaging system, etc.
Our wood pellet fuel processing line can be customized according to user needs such as the characteristics and production capacity of different wood waste and other biomass waste!
- Processable pellet types: wood fuel, wood cat litter pellets, wood based animal bedding, wood based feed, wood based fertilizer, etc.
- Byproducts of wood pellet processing plant: In addition to pellets, our system can also process sawdust, wood chips, and biomass briquettes.
4-5
Production capacity(t/h)
2-14
Pellet size(MM)
RICHI MACHINERY
video Of wood pellet processing plant
application of wood pellet processing plant
If you are optimistic about the prospects of wood pellet processing, as long as you have sufficient wood raw materials and wood waste, no matter which industry you are in, you can choose to build a wood pellet plant. Depending on the production scale, process and equipment, the investment amount of a pellet plant is different. If the budget is not high, you can start with a small wood pellet line. If the budget is sufficient, you can build a wood pellet production line of more than 5t/h, which will be more profitable and have a shorter payback period.
Timber mill
Sawdust mill
Wood Recycling Plant
wood pellet factory
Building Materials Company
Furniture Factory
power plant
Requirements for raw materials
In the actual wood pellet processing process, there are requirements for the raw materials. Before entering the pelletizing process, they need to meet the three requirements of moisture, size and purity at the same time.
What is your Main/primary raw materials? (Aim to design crushing system)
You can choose one raw material or different raw materials. The crushing process and crushing equipment for different raw materials may be different.
Most are wood log? most are wood chips? most are wood sawdust? most are irregular shape’s waste of wood ? or others , such as EFB ? or crop such as straw, husk, shell, leaves, grass …. ?
What is the moisture of your Main/primary raw materials?
- Dry type moisture =< 20% ? if yes , dont need drying system in your wood pellet processing plant.
- Wet type moisture > 20%, if yes , need drying system in your wood pellet processing plant.
Are your raw materials clean? Do they contain impurities?
Some customers’ raw materials are pure sawdust, but most customers’ raw materials contain various impurities such as nails and cigarette butts, and they need to be equipped with screening and cleaning equipment, iron removers, permanent magnet cylinders and other equipment to remove impurities from the raw materials.
RICHI MACHINERY
composition of wood pellet processing plant
A wood pellet processing plant is mainly composed of a cleaning system, a crushing system, a drying system, a pelletizing system, a cooling system, a screening system, and a packaging system. It also includes a dust removal system, a boiler steam system, an electronic control system, etc. Depending on the customer’s raw material and process requirements, a mixing system, a silo system, etc. are sometimes configured.
Richi Machinery can provide customers with complete tailor-made production solutions. By pursuing perfect quality control and after-sales service, we can precisely customize solutions to meet customers’ needs and have earned a reputation worldwide. We are always ready to serve you!
Cleaning section
This is the first process of the production plant and is crucial. The raw materials may contain impurities such as stones, metals, and plastics. If they are not cleaned up, they will damage subsequent equipment and affect the quality of the pellets. The cleaning section usually uses magnetic separation, screening and other methods to remove impurities.
Crushing section
The cleaned raw materials need to be crushed to a particle size of 3-5mm to meet the pelletizing requirements. The crushing section usually uses a hammer mill or chipper to crush the raw materials into fine particles, increase the specific surface area of the raw materials, and improve the pelletizing efficiency.
Drying section
Too high moisture content in the raw materials will affect the pelletizing effect, resulting in loose and brittle pellets. The drying section uses hot air drying to reduce the moisture content of the raw materials to less than 20%, thereby increasing the particle density and combustion efficiency. Commonly used drying equipment includes drum dryers, belt dryers, etc.
Granulation section
This is the core process of the wood pellet processing plant, which presses the crushed and dried raw materials into high-density pellet fuel. The wood granulator machine uses the strong pressure between the roller and the die to extrude the raw materials into cylindrical granules with a diameter of 2-14mm and a length of 10-30mm.
Cooling section
The wood pellets just out of the wood pellet mill are at a high temperature and need to be cooled before packaging. The cooling section usually uses a countercurrent cooler to use cold air to reduce the temperature of the pellets to near room temperature to prevent the granules from agglomerating and mildewing.
Screening section
The cooled wood pellets need to be screened to remove unqualified granules and powder. The screening section usually uses a vibrating screen to grade the granules by size to ensure uniform granule size and improve product quality.
Packaging section
Qualified wood pellets after screening need to be packaged for easy storage, transportation and sales. The packaging section usually uses an automatic packaging machine to pack the granules into bags according to a certain weight. Common packaging specifications are 15kg, 20kg, 25kg, etc.
Auxiliary system
Auxiliary system is an important guarantee for the normal operation of the production line, including dust removal system, electrical control system, steam system, silo system, etc. Some are required and some are optional. According to customer needs, we will configure suitable equipment for customers.
RICHI MACHINERY
equipment needed to start wood pellet processing plant
The equipment required for the wood pellet processing plant is determined by the process flow. First determine your wood pellet processing process, then determine the corresponding equipment. Like the process, the configuration of the equipment is also flexible and optional. According to your needs and investment budget, RICHI engineers will configure the most suitable combination of wood pellet processing equipment for you. Below is a list of common equipment used to process wood pellets.
The following are some common equipment for processing wood pellets. Since there are many equipment, they are not listed here one by one(For example, shredders, thermoplastic sealers, palletizers, etc.). What you need to know is that as long as it is equipment for wood pellets production plant, RICHI can definitely provide it.
debarking machine
The raw material required is tree trunks, and a debarking machine is required to ensure the quality of the raw material and particles.
Wood splitter
This device is used to reduce the diameter of a tree trunk. It is usually used for tree trunks with a very large diameter.
wood chipper machine
This is one of the most widely used wood processing equipment, mainly used to process tree trunks, branches, wood strips, etc. into wood chips.
wood pallet Crusher
This is equipment specially used for crushing wooden pallets and formwork, and also processing these raw materials into wood chips.
sawdust making machine
This is a multifunctional crushing equipment that can process both wood chips and sawdust. However, it is mainly used for small-scale processing.
wood pellet hammer mill
This equipment is mainly used to process wood chips into sawdust. It is not only used in pellet production lines, but can also be directly used to process horse beds and animal bedding.
wood pellet machine
Used to process crushed raw materials into wood particles.
wood chip dryer
Used for drying wood chips, sawdust and other high moisture materials of various sizes..
pellet cooler machine
Used to cool the prepared wood pellets to ensure the quality and hardness.
vibrating screening machine
Used to screen out qualified wood pellets.
Automatic Bagging Machine
Used for packaging various types of wood pellet products.
Jumbo Bag Filling Machine
For wood pellet packaging of 500 kg and above.
mixing machine
When using different raw materials, a mixer is needed to ensure uniformity of particle quality.
Drum screening machine
Mainly used to screen out impurities such as nails, stones, etc. from wood chips, sawdust and shavings.
Pulse dust collector
According to the process requirements, single-point dust removal and centralized dust removal systems can be set up to purify the production environment.
Scraper conveyor
Used for material transportation between different systems.
belt conveyor machine
It is also a part of the conveying system. It can be customized to be mobile.
bucket elevator conveyor
Used in process design for longitudinal conveying.
Electric control cabinet
Used to control the automated production and operation of the entire small wood pellet plant.
Storage silo
It is used to temporarily store sawdust, wood chips and other materials in the production line. It can also be used to store wood particles.
Boiler
It delivers steam and provides heat source for the entire small wood pellet plant.
Features of Wood Pellet processing Plant
Durable Parts
This wood pellet plant machine comes with seven core components – the wood chipper, heating stove, pellet mill, packing machine, cooler, dryer, and hammer mill. All are made out of strong, durable materials. These materials are wear-resistant and made according to the latest technology. These parts experience low-wear and therefore can reduce our consumption.
Multi-Function plant
This wood pellet processing plant can be widely used in many kinds of industries, including chemical production, organic fertilizer, electricity, biofuels, waste tire, cat litter, animal bedding and more.
Low Energy Consumption
The wood pellet processing plant offers exceptionally low energy consumption. It reduces up to 50% of your energy needs, produces minimal vibration, and has more than 40% heating efficiency. This can save you money while also helping to save the planet.
Easy to Install and Operate
The wood pellet processing plant is easy to install and operate, especially compared to other options on the market. You’ll have access to a one-stop service that can meet the needs of any customer, from large international companies down to individuals. Your questions will be answered in 24 hours or less with onsite visits available.
Versatile and Adjustable
The wood pellet processing plant can crush and process all kinds of materials into pellets, including PVC foam board, wood, weeds, straw, and even waste scrubber. Its high-strength steel grinding chamber is durable and offers greater overall efficiency regardless so the type of material you are processing.
Automatically Packs and Cools the Pellets
Not all wood pellet production plants come with coolers and packers, but this one does. It can save you money by bundling all the features you need into one pellet plant.
We care about what you need
Our focus is to bring your performance forward. Our expertise in sustainable energy production is at your disposal.
Get in touch with our specialists through our website or the link below.
RICHI MACHINERY
customized wood pellet processing plant design
The process flow of the wood pellet processing plant is customized according to the customer’s raw materials, plant structure and process requirements. Some customers’ raw materials contain a lot of waste, while others’ raw materials are just sawdust; some customers’ plants are 20 meters high, while others are only 7 meters high; some customers need manual packaging, while others need a fully automatic palletizing system… If you have a need, we can definitely make it happen. This is the promise from RICHI MACHIENRY.
01
4-5T/H wood pellet processing plant design
This is a process flow chart from one of our US projects. As can be seen from the figure, the customer uses two kinds of raw materials, one is sawdust, which needs to be cleaned by a drum screen. The other is logs, which are crushed twice by a slicer and a hammer mill, and then enter the drying drum together with the cleaned sawdust for drying.
The dried materials will be sent to the wood pellet machine through a bucket elevator for pelletizing, and then enter the cooling and screening section one after another. This project does not have a packaging section, because the processed wood pellets will enter the finished product buffer bin, and then enter the truck and leave the factory in bulk.
02
4-5T/H wood pellet processing plant design
This is a process flow chart from one of our New Zealand projects. This project only uses logs as raw materials, and the moisture content is not high. The process flow of this project is: the raw materials are sliced by a slicer, and then enter the wood hammer mill through a bucket elevator for fine crushing. The crushed materials are sent to the storage bin for temporary storage. The storage process will also help reduce the moisture content of the materials. Subsequently, the materials enter the pelletizing section for pelletizing.
After pelletizing, they enter the cooling, screening and packaging sections one after another. The packaged pellets are stored in the finished product warehouse. This project has a distinct feature from the previous American project: the plant height is relatively high. Therefore, the main conveying method is bucket elevator.
03
4-5T/H wood pellet processing plant design
This is a process flow chart from one of our Argentina projects. This project also uses two kinds of raw materials, one is sawdust, which needs to be cleaned by a drum screen. The other is logs, which are crushed twice by a slicer and a hammer mill, and then enter the drying drum together with the cleaned sawdust for drying.
The dried materials are piled in place, and the dried materials are sent to the pelletizer by a forklift. Then they enter the cooling and screening section one after another. This project has two packaging equipment, one is a conventional fully automatic packaging scale, and the other is a ton bag scale. They are used to package products of different specifications. The height of the customer’s factory is limited, so the curling conveyor is used.
From small wood pellet plants to large turnkey wood pellet plants, view our wood pellet processing plant projects around the world.
RICHI MACHINERY
wood pellet processing plant projects
At present, our wood pellet processing plant has been exported to the United States, Canada, the Netherlands, Denmark, Germany, France, Indonesia, Romania, Colombia, Iceland, Malaysia, Brazil, Argentina, Ecuador, Pakistan, Thailand, Egypt, Peru, South Africa, Australia, Ghana, Angola, New Zealand, South Korea, Japan and other countries. If you want to know more about our projects, you can contact us directly, and our technical consultant will send you detailed information and operation videos of the project.
4T/H
wood pellet processing plant in Thailand
Overview
In the early stage of this project, wood chips and various wood wastes were used as the main raw materials. Due to the promotion of local policies, the project began to use palm shells, palm fruit bunches, bamboo, straw and other raw materials in June 2015.
4-5T/H
wood pellet processing plant in Brazil
Overview
The project uses logs as the main raw material. The project is divided into two phases. The first phase is a 4-5t/h wood pellet production line, and the second phase is an 8-10t/h agricultural waste pellet production line. Currently, the second phase is under construction.
5T/H
wood pellet processing plant in Austria
Overview
This project uses logs as raw materials. The customer selected two MZLH520 wood pellet machines, which can produce 5 tons per hour. The customer is currently planning to expand production, and RICH engineers are designing a plan.
5T/H
wood pellet processing plant in canada
Overview
This is our first wood pellet processing plant project in Canada. As of March 2025, we have built 16 biomass pellet production lines in Canada. The customer of this project mainly uses logs and wood blocks as the main raw materials.
5-6T/H
wood pellet processing plant in U.K.
Overview
This project is a supporting project for a power station in the UK. The customer uses wood chips as the main raw material and the project investment is US$320,000.
5T/H
wood pellet processing plant in Italy
Overview
This is our second wood pellet project in Italy, used to process fuel pellets. The raw material is sawdust. We have also built a wood cat litter production line in Italy.
wood pellet processing plant cost
— Richi Machinery —
Generally speaking, a 4-5 t/h wood pellet processing plant price is usually between 80,000-500,000 USD. In order to give you a better understanding of the purchase cost of different output wood pellet processing plants, RICHI will provide you with the corresponding price range below.
Complete wood pellet processing plant, FOB Price :
Note: Even if the capacity is the same,
- Different moisture content ( wet or dry ) of raw materials will affect the final design and price
- Different shapes ( log , chips, sawdust ….. ) of raw materials will affect the final design and price.
The prices given here refer only to the price of the complete set of production line equipment. As long as you have a factory building, electricity, operators, raw materials, and production line equipment, then your wood pellet processing business can be prepared.
Capacity | wood pellet processing plant cost (USD) |
0.2-0.3 T/H | 20,000-140,000 |
0.3-0.5 T/H | 28,000-160,000 |
1.0-1.2 T/H | 39,000-220,000 |
1.5-2.0 T/H | 46,000-270,000 |
2.5-3.0 T/H | 58,000-350,000 |
3.0-4.0 T/H | 75,000-430,000 |
5.0-6.0 T/H | 130,000-570,000 |
6.0-8.0 T/H | 170,000-690,000 |
10-12 T/H | 240,000-1,100,000 |
12-15 T/H | 370,000-1,430,000 |
15-20 T/H | 430,000-1,850,000 |
20-24 T/H | 570,000-2,100,000 |
higher capacity… | … |
case studies
【Case 1】: 4 t/h wood pellet processing plant project
This project mainly uses wood scraps from the wood carving industry and delumber factories as raw materials to process and produce biomass molding fuels, such as wood residues (referring to wood cutoffs, corner waste, etc.) and processing residues (referring to boards, slats, wood and bamboo cuts, sawdust, broken veneer, wood core, shavings, wood blocks and leftovers, etc.).
After the biomass is chipped, crushed and extruded, its volume is greatly reduced, which makes it easier to transport, store and use.
It is suitable for biomass power generation, clean energy transformation of industrial boilers, new cooking fuels in rural areas, and makes full use of the woodcarving industry and solutions. Timber waste and leftovers in wood mills, processing residues, etc.
To this end, the client rented an idle factory building and adjacent open space to build a biomass compact briquette fuel processing project. After the project is completed, the annual output of 10,000 tons of biomass wood pellet fuel will be produced. The project conforms to the industrial policy and has good environmental, economic and social benefits.
Overview
- Construction nature: newly built;
- Construction scale: The project covers an area of 2,000m², with a total construction area of about 800m², and the project is designed to produce 10,000 tons of biomass briquettes per year;
- Production process: Biomass molding fuel: raw material crushing→crushing→cyclone sorting→transmission→pelleting→packaging;
- Total investment: USD 270,000;
- Working system: 320 working days per year, the working system adopts a one-shift system, 10 h/shift;
- Number of employees: 5 people.
- Others: There are no canteens, dormitories, and bathrooms in the factory
Product and production scale
Product name | Yield | Where the product goes |
---|---|---|
Biomass pellet fuel | 10000t/a | Takeaway |
Product Specifications
Low calorific value (MJ/kg) | Density (kg/m³) | Moisture content (%) | Ash (%) | Broken rate |
---|---|---|---|---|
≥ 17 | ≥ 900 | ≤ 12 | ≤ 6 | ≤ 5 |
Consumption of raw and auxiliary materials
The raw materials of the 4t/h wood pellet processing plant project are wood residues, leftover materials, wood chips, etc., which are mainly purchased from the local wood carving industry and surrounding delumber factories, and the supply of raw materials is guaranteed.
The moisture content of wood residues purchased in the project is about 15% to 20%, and the moisture content of wood chips is about 9% to 10%. The main raw and auxiliary materials used in the project are shown in the table below.
Project | Name | Annual consumption (t) | Proportion | Remarks |
---|---|---|---|---|
Materials | Wood Remnants | 4220 | 40% | Wood carving industry and surrounding wood factory purchase |
Materials | Sawdust | 6330 | 60% | Wood carving industry and surrounding wood factory purchase |
Energy Consumption | Electricity | 15,000 kW·h | / | Municipal power supply |
Equipment for 4T/H Wood Pelleting system
Device name | Model/Remarks | QTY |
---|---|---|
Template breaker | / | 1 |
Wood shredder | ZS500—30 | 1 |
Wood shredder | ZS—800 | 1 |
Cyclone | 700mm diameter | 1 |
Cyclone | diameter 1500mm | 1 |
Duster | 9 cloth bags | 1 |
Duster | 36 cloth bags | 1 |
Unloader | 1.1kW | 1 |
Unloader | 1.5kW | 1 |
Conveyor belt | PSJ500-8 | 8 meters |
Feeding screw conveyor | ZS—4000/diameter 219mm | 3 |
Wood pellet press machine | MZLH520 | 1 |
Wood pellet making machine | MZLH420 | 2 |
Silo | / | 2 |
Silo unloader | 1.1kW | 3 |
Loader | / | 1 |
Hand forklift | / | 1 |
Trolley | / | 3 |
Composition of 4T/H wood pellet processing plant
The project mainly includes main works, auxiliary works, public works, environmental protection works and storage and transportation works.
- Production Workshop: The production workshop is an elevated color steel structure, covering an area of 250m², with crushing, crushing, feeding, extrusion molding, packaging and other production processes. Relying on the original factory building for equipment installation;
- Office: Located in the west of the factory building, it is a 1-story color steel tile and brick-concrete building with a construction area of 160 m², mainly for offices and lounges. Relying on the original;
- Toilet: Located in the east of the factory building, a toilet is flush, with a building area of 1.5 m². Relying on the original vacant land to build a new building;
- Raw material storage yard: The stacking room of the raw material workshop is located in the east of the production workshop, which is used for stacking raw materials in broken form (wood chips, small wood blocks, etc., covering an area of 200m².
The open-air raw material storage yard is located in the northeast of the factory area, covering an area of 240 m². The storage room of the raw material factory building is rebuilt based on the original factory building, and the open-air raw material storage yard is based on the original open space planning; - Finished product storage room: Located in the west of the production workshop, connected to the production workshop, covering an area of 120m², used for stacking finished products. Relying on the original.
4T/H wood pellet Production Process
Biomass pellet fuel is a new type of clean fuel that uses wood and straw agricultural solid waste as raw materials and undergoes crushing, crushing, transmission, extrusion molding, packaging and other processes to make briquettes such as blocks and granules, which can be directly burned.
- Raw materials are transported by vehicles into the raw material yard for storage.
- Chipping of raw materials: Use trolleys and other tools to transport raw materials to the production workshop, and put large pieces of wood raw materials into crushers for chipping and crushing.
- Crushing of raw materials: Broken raw materials such as sawdust, wood blocks and crushed materials can be directly put into the crusher for crushing. Dust and noise will be generated during the crushing process.
- Powder transmission: After the raw material is crushed, the powder falls into the silo and then is transported to the granulator by the feeding auger through the unloader.
- Extrusion (granulation): The powder is extruded in a wood pelletizer machine.
- Packaging: The granulated products are put into packaging bags through the finished product silo of the wood granulator.
- Stacking of finished products: After the finished products are packaged, they are uniformly stacked in the finished product stacking room.
General layout
The 4t/h wood pellet processing plant project leases the existing factory building for decoration and reconstruction according to the project design. The area is divided into raw material areas, finished product storage areas and production workshops.
The project land is irregular rectangle. The open-air raw material storage yard is arranged in the northeast of the project factory area, which is used to stack some wood raw materials.
The production workshop is located in the north of the middle area of the factory area. The production workshop is equipped with production equipment for raw material crushing, transmission, compression molding, packaging and other processes.
The finished product stacking room is connected to it on the west side of production workshop, and the raw material plant stacking room is located on the south side of the production workshop and is connected to the production workshop.
Office and rest rooms are located in the west of the factory area, adjacent to the finished product stacking room. The domestic wastewater is treated in the septic tank and then discharged into the temporary wastewater storage tank located in the southeast corner of the plant area.
The plant area and its surroundings are well greened. Lubricating oil is required for the operation, maintenance and maintenance of machinery and equipment in this project, and a small amount of waste lubricating oil will be generated. A hazardous waste temporary storage room is set up for the storage of waste lubricating oil, which has little impact on the environment.
Generally speaking, the construction of the project factory area meets the technological
【Case 2】: 4T/H wood pellet processing plant System
Based on the prospects of biomass pellets, the customer invested 250,000 US dollars to build a new biomass pellet production line project with an annual output of 9600t. The area where the customer is located is a treasure trove of biological genes, with rich plant species, which also means that the customer has a very sufficient source of raw materials.
Number of employees and working system
The project labor quota is 10 people, and the annual working days are 300 days, with one shift per day and 8 hours of work per day. No board and lodging will be provided in the project.
Construction scale and product plan
Product name | Design production capacity | Yearly run hours |
---|---|---|
Biomass pellets | 9600t | 2400 |
Consumption of main raw and auxiliary materials
Category | Name | Physical Form | Annual consumption | Source | Storage method | Remarks |
---|---|---|---|---|---|---|
Raw materials | Wood | Solid state | 9601t | Outsourcing | Stored in the factory area, transported by car | The furniture factory recycles wood scraps, shavings, etc. |
Energy consumption
Category | Annual usage | Source |
---|---|---|
Water | 120t | Municipal water supply network |
Electricity | 100,000 kWh | Municipal power grid |
- The power required for production is supplied by municipal power, and generators are not used for equipment.
- All water used in the project is supplied by the municipal waterworks.
Construction Content
The 4t/h wood pellet processing plant project is mainly equipped with crushing area, granulation area, warehouse and office, etc.
- Crushing Zone:Mainly used as a wood crushing area, with an area of about 600m², equipped with 1 wood grabber, 1 shredder, and 2 conveyor belts;
- Granulation area:Mainly used as a granulation forming area, with an area of about 200m², equipped with 4 granulators and 2 conveyor belts;
- Office:Approximately 200m²
- Dust treatment facility:Bag dust removal with a treatment efficiency of 99%
- Integrated sewage treatment facilities:Biochemical treatment, 1 unit
- Warehouse:The area is about 1000m²
4T/H wood pellet processing equipment list
Name | QTY |
---|---|
Conveyor belt | 4 |
Grinder | 1 |
logger | 1 |
MZLH420 wood pellet press | 4 |
Air compressor | 1 |
Dust treatment facility | 1 |
Integrated sewage treatment facilities | 1 |
4T/H wood pellet processing plant Process Design
The project puts the recovered wood into the funnel through the wood grabber, and transports it to the pulverizer through the conveyor belt for pulverization (the particle size after pulverization is less than 5mm). The granulator compresses the wood powder into granules with a compression ratio of 5.5:1, and then after natural drying, it can be packaged and shipped.
The raw material of the project is the leftover material of the furniture factory, and the moisture content of the wood is about 8%-15%, which meets the requirements of granulation and molding, so there is no need to dry during the wood pellet production process.
[Case 3] : 5 t/h wood pellet processing plant construction project
- Project name: Production line construction project with an annual output of 12,000 tons of wood pellets
- Nature of construction: newly built
- Project investment: total investment 330,000 USD,
- Labor capacity: 10 people
- Working system: 300 working days per year, one shift system, 8 hours per shift
Project construction scale and content
The total land area of this project is 2,653 square meters, and the existing plant is leased for biomass pellet production. The project plant is divided into raw material area, granulation area, and finished product area.
- Granulation area: 1F, with an area of about 400m², mainly for the granulation process, located in the east of the plant, with 2 wood pellet machines.
- Office building: 1F, covering an area of 60m² for office.
- Raw material area: 1F, with an area of about 700m², is mainly used for raw material stacking, located in the north of the plant.
- Warehouse: 1F, with an area of about 300m², mainly used for stacking finished products, located in the west of the factory building.
Product solutions
The product of this 5t/h wood pellet processing plant project is mainly shaped biomass pellet fuel, and the annual output of shaped wood pellets is expected to be 12,000 tons.
Formed wood pellet specifications:
- Raw material: sawdust;
- Formed biomass particle diameter: 8mm;
- Length: 8cm;
- Ash content≦8.0%;
- Density≧1.1t/m3;
- Low calorific value 3200kg/kcal;
- The moisture content of the finished product is less than 8%, about 7.5%.
Main raw materials and energy consumption
The main raw material of this project is wood chips, which have been crushed before entering the factory, with a moisture content of about 8%, which meets the requirements of granulation and molding, so we do not need to configure drying cylinders for customers.
Name | Annual Consumption | Remarks |
---|---|---|
Sawdust | 12030t | Purchased crushed sawdust, with a moisture content of about 8%, does not need to be dried during the production process, and is stored in the raw material area, with a maximum storage capacity of 30t |
Water | 150m³ | Plant self-provided well |
Electricity | 30000 KW·h | Powered by the local power supply system |
Equipment for 5 t/h wood pellet processing plant
Name | QTY |
---|---|
Wood pellet machine | 2 |
conveyor belt | 2 |
bucket elevator | 1 |
Forklift | 1 |
Exhaust gas treatment equipment | 1 set |
5 ton per hour wood pellet production process flow
The production process of this 5t/h wood pellet processing plant project is relatively simple, and all processes are physical processes.
(1) Raw materials
The raw materials of the project are transported by car to the raw material workshop for standby.
(2) Granulation
The sawdust raw material of this project has been crushed before entering the factory, and can be directly entered into the wood granulator machine for granulation. The raw material for granulation is only wood chips without any additives. The principle of the wood pellet press is that fine materials are rolled and extruded by rollers.
The granulation process adopts electric heating, and the granulation temperature is 80℃-120℃. Sawdust is deformed and extruded into granules under high temperature and high pressure. Transported to the next process by belt conveyor.
(Water vapor is the evaporation of water in raw materials due to high temperature and high pressure in the granulation process. The moisture content of raw materials for this project is about 8%, and the moisture content of finished products is 7.8%. The water vapor generated by this project is about 24t/a.)
(3) Packaging
The temperature of compressed wood pellets is generally 40-50℃, and they need to be cooled during packaging. The finished products after granulation are transported to the finished product yard by the conveyor belt for natural cooling.
And then packaged after cooling. In order to save costs, and the customer’s local labor cost is low, we design a manual packaging section for the customer.
Public works
(1) Water supply
The water supply of this 5t/h wood pellet processing plant project comes from the self-provided well in the factory area. During the operation period of this project, no water is needed for production, and the water used is mainly domestic water for employees.
There are a total of 10 employees in this project, and the annual working hours are about 300 days, and none of them have board and lodging in the factory area.
(2) Power supply
The project is powered by the power supply system, and the annual power consumption is about 30,000 KWh. There is no backup diesel generator in the site.
General layout
This project leases the completed factory building, the site is roughly rectangular, and an entrance and exit is set on the south side. According to the site provided by the customer, RICHI Engineering will carry out the whole wood pellet plant layout for the customer:
- The factory area is composed of raw material workshop, granulation workshop, finished product workshop, office area, etc. The granulation workshop is located on the east side of the factory area;
- The finished product area and the raw material area are located on the west and north sides of the factory respectively.
Each functional area of this wood pellet processing plant project is clearly divided, relatively independent and organically connected, and the client is quite satisfied with this.
[Case 4] : 5 t/h wood pellet processing plant project
- Project nature: newly built
- Annual output: 12,000 tons
- Raw materials: waste wood, waste wooden furniture
- Power consumption: 200000 kw h
- Number of employees: 10 people, all of whom do not have board and lodging in the factory.
- Work system: 8 hours per shift, one shift per day, 300 working days per year, 2400 hours per year.
- Project investment: 390,000 USD
Construction Content
This customer leased 2 workshops to build a new 5 ton wood pellet processing plant.
- Chipping area: mainly for the crushing process, located in the northwest of plant 1, with an area of about 400m², and 1 wood chipper;
- Crushing area: mainly for the crushing process, located in the northeast of Plant 1, with an area of about 400m² and 3 sets of wood hammer mill crushing machines;
- Pelleting area: mainly for the granulation process, located in the west of plant building 2, with an area of about 300m², equipped with 5 wood pellet machines and 1 air compressor;
- Raw material area: mainly used for raw material stacking, located in the south of workshop 1, with an area of about 700m²;
- Warehouse: mainly used for stacking finished products, located in the east of plant 2, with an area of about 1400m²;
- Reserved workshop: Mainly used for raw materials or finished product check-out reserved space, located in the northeast of plant 1, with an area of about 300m².
Product plan of 5 t/h wood pellet processing plant
Product Name | Design Capacity | Yearly run hours |
---|---|---|
Biomass wood pellets | 12,000 t/a | 2400 hours |
Consumption of raw materials
Name | Status | Annual Consumption |
---|---|---|
Scrap | Solid state | 6000t |
Waste wood furniture | Solid state | 6000t |
Energy consumption
Name | Annual Consumption |
---|---|
Electricity | 200,000 kw h |
Office and domestic water | 120m³ |
Main wood pellet processing equipment
Name | QTY | Remarks |
---|---|---|
wood pellet extruder machine | 2 | Granulation process |
Wood chipper | 1 | Crushing process |
Wood hammer mill crusher | 1 | Crushing process |
Air compressor | 1 | Transport Aids |
Screw conveyor | 3 | Transport Aids |
Conveyor belt | 3 | Transport Aids |
Bucket elevator | 1 | Transport Aids |
Forklift | 2 | Transport Aids |
Forklift | 2 | Transport Aids |
Catch firewood truck | 2 | Transport Aids |
Line Hanging | 1 | Transport Aids |
Exhaust gas treatment equipment | 2 | Air volume: 10000m³/h |
5 t/h wood pellet processing plant design
- Crushing: The new design wood pellet processing plant project will manually sieve the purchased waste wood, waste wooden furniture and other materials that do not contain toxic and harmful substances such as paint and glue, and place large pieces (pieces) of raw materials through forklifts or forklifts. Crushing is carried out on the machine.
- Grinding: small pieces (pieces) of raw materials are crushed together with the crushed materials through a grinder (the particle size after crushing is less than 5mm), and the crushed wood powder is transported to the wood pellet machine.
- Granulation: Through the high-speed rotation of the ring die, the sawdust raw material begins to heat up and become soft (the pressure of the high-speed rotating roller can reach 300T, and the temperature of the sawdust can reach 100℃ to 130℃).
The softened and heated sawdust raw material is extruded through the holes of the ring die under strong pressure. During this process, the wood chip has increased compactness, reduced moisture content, and a compression ratio of 5.5:1. - Cooling & Sieving & Packaging: Then cool and dry naturally, and then sieve through the drum sieve in the conveyor belt. After the biomass particles are screened, they are transported to the finished product warehouse, where they can be packaged and shipped.
Note:
- The moisture content of the raw materials of the 5t/h wood pellet processing plant project is 8%-15%, which meets the requirements of granulation and molding, so there is no need to dry or add water during the production process;
- All wood raw materials are pure wood materials. It is strictly forbidden to recycle waste furniture with paint, glue, etc. On the one hand, it can improve product quality, and on the other hand, it can avoid the impact of introducing organic waste gas pollutants.
- The crushing, pulverizing and granulating process of the raw materials of the project are respectively carried out in the closed cavity of the crusher, pulverizer and granulator, and the pulverizer and the granulator are connected and transported through the closed pipeline.
General layout
The 5t/h wood pellet processing plant project building includes 2 workshops:
- Plant 1: The northwest is the crushing area, the northeast area is the crushing area and reserved workshop, and the south is the raw material area;
- Plant 2: The western area is the granulation area, and the eastern area is the warehouse.
Richi Machinery
start your wood pellet processing business
With the popularization of environmental protection concepts and the strengthening of environmental protection in countries around the world, the demand for wood pellet processing market is gradually increasing. Wood pellets are a green and environmentally friendly renewable energy with the advantages of low cost, high combustion efficiency and harmless emissions, so they are favored by more and more people.
RICHI is committed to the R&D and manufacturing of pellet mills and supporting equipment, and can provide customers with wood pellet production engineering services from land construction planning, process design, automation control, equipment manufacturing, installation and commissioning, personnel training to after-sales service.
If you also want to build a low investment high return wood pellet processing plant, feel free to contact Richi Machinery!
What raw materials can be used?
All agricultural and forestry wastes and some industrial wastes can be used for wood pellet processing. Most of the processed wood pellets are used as fuel, some are used as cat litter and animal bedding, and very few customers use them as feed.
No matter what your raw materials are, whether the raw materials have a lot of impurities, whether the raw materials have high moisture content, and no matter the size of the raw materials, we can help you process and design and manufacture a high-quality wood pellet processing plant that meets your expectations and needs.
wood log
wood chips
wood sawdust
yard waste
wooden pallets
wood waste
Frequently Ask Question
Frequently Ask Question
How to invest in the construction of awood pellet processing plant?
Developing a wood pellet processing plant requires comprehensive consideration of multiple aspects such as raw material supply, equipment selection, production process, market positioning, policies and regulations, etc.
- Regarding investing in building a factory, first you need to purchase the entire production line. The equipment required depends on your feedstock, the smaller the physical size of the feedstock, the less equipment is required.
For example, if you use fresh logs, you need not only coarse crushing and fine crushing equipment, but also a dryer to process the raw materials. In this case, the investment will obviously be relatively high;
If you use dry wood chips, shavings (generally easy to obtain from sawdust mills, furniture factories, board factories), all you need are screening machines, pellet machines, cooling machines, and packaging machines.
Therefore, you need to fully consider the factors of raw materials to choose a wood pellet processing plant construction plan, or you can also consult us, and RICHI engineers will tailor a solution for you to help you succeed!
- In addition, the quality of the equipment cannot be ignored. Excellent and precise workmanship, high standard quality control means low machine failure rate and high pellet yield rate.
Selecting equipment for a wood pellet production line requires comprehensive consideration of factors such as raw material characteristics, production capacity requirements, process requirements, budget, and post-maintenance. The following are key steps and precautions:
- Clarify production requirements
- Raw material types: wood chips, sawdust, shavings, branches, etc. (the particle size, moisture, and hardness of the raw materials affect the equipment selection).
- Production capacity requirements: hourly output (such as 0.5 tons, 1 ton, 5 tons, etc.) determines the scale of the equipment.
- Particle specifications: diameter (6-10mm is common), length, density (usually ≥1.0g/cm³).
- Finished product use: home heating, industrial fuel, animal bedding, etc. (different uses have different requirements for particle quality).
- Core equipment selection
(1) Crushing equipment (raw material pretreatment)
- Coarse crushing: branches and wood blocks must first be processed with a chipper (such as a drum chipper) or a wood crusher.
- Fine crushing: hammer mill (suitable for raw materials with moisture <15%) or blade mill (more efficient for fiber raw materials).
- Key parameters: discharge particle size (generally ≤3mm), power matching capacity.
(2) Drying equipment
- Rotary dryer: suitable for large-scale production, heat source can be natural gas, biomass or steam.
- Airflow dryer: suitable for small-scale or low-humidity raw materials.
- Key parameters: reduce the humidity of raw materials to 10-15% (too high affects molding, too low increases energy consumption).
(3) Pellet mill (core equipment)
- Flat die wood pellet mill: Suitable for small-scale (<0.5 ton/hour) or fiber raw materials. Simple structure, easy maintenance, but low output.
- Ring die wood pellet mill: Suitable for large-scale production (0.2-10 tons/hour), high particle density. The ring die aperture and compression ratio need to be selected according to the raw material (4:1-6:1 is commonly used for wood chips).
- Key parameters: motor power (such as a capacity of 1 ton/hour requires about 90kW), ring die material (alloy steel has high durability).
(4) Cooling and screening
- Counterflow cooler: reduce pellet temperature (< ambient temperature + 5°C) and humidity.
- Vibrating screen: remove debris and ensure uniformity of finished pellets.
(5) Packaging equipment
Semi-automatic packaging machines are optional for small lines, and fully automatic weighing and packaging lines are used for large lines.
- Auxiliary equipment and systems
- Dust removal system: cyclone separator + pulse dust collector (in line with environmental protection requirements).
- Conveying equipment: belt conveyor (dry raw materials), screw conveyor (wet materials).
- Automation control: PLC system can optimize energy consumption and stability (optional).
RICHI wood pellet processing plant and equipment has been tested by the market and customers, the quality of the equipment and our service are worthy of your trust!
What are the raw materials that can be used in wood pellet processing plant?
The wood pellet processing plant is suitable for a wide range of raw materials, mainly including forestry residues, agricultural waste, energy crops and other biomass materials.
- Forestry Residues
- Wood processing waste: sawdust, wood chips, shavings, off-cuts
- Forest harvesting residues: branches, tops, bark, small-diameter logs
- Secondary forest/economic forest: fast-growing tree species such as eucalyptus, pine, fir, and poplar
- Agricultural Residues
- Straw: corn straw, wheat straw, rice straw, cotton stalk, etc.
- Fruit shells/kernels: coconut shells, palm kernel shells, olive pits, apricot shells, etc.
- Other agricultural waste: Bagasse, Peanut Shell, Sunflower Husk, etc.
- Energy Crops
- Herbaceous Energy Crops: Switchgrass, Miscanthus, Reed Canary Grass, etc.
- Wooden Energy Crops: Short Rotation Trees (such as Willow, Poplar), etc.
- Other Biomass Materials
- Waste Wood: Building Formwork, Waste Furniture, Pallets, etc.
- Industrial By-products: Paper Mill Black Liquor (Special Treatment Required), Distillers Grains, etc.
- Bamboo, etc.
How to choose the raw materials for the wood pellet processing plant?
When choosing the raw materials for the wood pellet processing plant, the following key factors need to be considered:
Moisture content: The ideal range is 10%~20%, and if it is too high, it needs to be dried.
Ash content: Agricultural waste (such as straw) has a high ash content, which may affect combustion efficiency.
Binder requirements: Some raw materials (such as fruit shells) may need to be added with natural binders (such as lignin).
Economical: Obtaining raw materials nearby can reduce transportation costs (such as forestry waste in Northern Europe and palm waste in Southeast Asia). If you have a timber mill, furniture factory, sawdust mill, or palm oil mill, it also means you have ready-made raw materials to use.
Solutions for different production volumes
We customize wood pellet production lines with different processes and designs for different production scales of wood pellet processing. You can use our production lines and equipment to process any fuel pellets, cat litter pellets, animal bedding pellets and other special types of pellet products, such as carbon pellets, rat poison pellets, snail poison, air purifier pellets, etc.
small wood pellet plant
Mainly for small wood pellet processing, the production output is between 200-1000 kg per hour.
complete wood pellet line
We have many projects for reference for the processing of 1-2 tons per hour of wood pellets.
wood pellet processing equipment
The wood pellet business with 2-4 tons per hour is already a production scale that can generate profits.
wood pellet processing plant
Based on customer needs and actual working conditions, we provide a more reliable 4-5t/h wood pellet processing plant with professional technology.
wood pellet production plant
RICHI is committed to global complete 6-7t/h wood pellet production plant solutions, including chippers, crushers, dryers, granulators, coolers, screeners, etc.
wood pellet making equipment
7-8T/H wood pellet making plant includes a series of equipment such as crushing and pelleting, forming a complete closed industrial chain of pelleting.
wood pellet manufacturing equipment
RICHI’s 8-10t/h wood pellet manufacturing plant solution truly realizes a complete set of sustainable products in the field of wood pellet processing.
wood pellet factory
12-15T/H biomass wood pellet actory solution covers sawdust, wood chip, log pellet line, etc., targeting the global wood pellet market.
wood pellet manufacturing plant
The 15-20t/h pellet plantl can meet the wood pellet processing needs of various scales, various raw materials, and various plant spaces. The equipment has high efficiency, safety and stability.
wood pellet making line
RICHI is committed to creating complete sets of 20-30t/h wood pellet making line solutions for customers, with projects covering major markets such as Indonesia, the United States, Canada, and Germany.
turnkey wood pellet mill
In response to global energy demand, RICHI provides 30-40t/h turnkey wood pellet mill plant solutions, and can flexibly configure a series of equipment according to customers’ actual conditions.
large wood pellet mill
40-50T/H large wood pellet mill plant meets the wood pellet production needs of different fields such as biomass fuel pellet factories, lumber factories, sawdust factories, and furniture factories, etc.
● RICHI MACHINERY
service for wood pellet processing plant
Any Problem, Please Contact Richi Machinery. The Exclusive Customer Service Manager Will Provide One-Stop Worry-Free Solutions.
● Consulting
Customer Consultation
We want to have a deep understanding of your industrial process, to know your exact needs of feed, wood, biomass, fertilizer or other pellet processing.
● Design
wood Pellet Plant Design
Based on your unique situation and industrial process, we will tailor complete wood pellet processing plant you need, and inform you of every additional detail that could facilitate operation, minimize total cost.
● Manufacturing
Equipment Manufacturing
The critical components of the of the complete wood pellet processing plant equipment are built in our own workshops in Asia. Additional equipment is manufactured by our worldwide network of reliable partners.
● Testing
Quality Inspection & Testing
Before leaving the factory, all equipment will be inspected by the quality inspection department. We can also provide customers with testing services from a single machine to a complete pellet plant system, and provide you with real actual data for “worry-free use.”
● Delivery
Equipment Delivery
In equipment boxing and packaging, we adopt professional packaging and modular solutions to ensure the safe and non-destructive delivery of wood pellet equipment.
● Installation
Installation & Commissioning
Whether you choose your own subcontractor for the erection phase or you want to install everything together with us, a Richi supervisor will be around to make sure everything is mounted in a safe and thorough way.
● Training
Staff Training
We provide comprehensive training for the technicians of each wood pellet processing plant project. We can also continue to provide support for the technicians during latter project operation.
● After-sales
Project Follow-Up
When everything is up and running our Richiers will help you further whenever needed. We are ready to answer your call 24/7.We’ll also visit you regularly to learn about your needs.
Who We Are
RICHI Machinery is one of the world’s leading suppliers of technology and services for the animal feed, aqua feed and pet food industries, also the largest pellet production line manufacturer in China.
Since 1995, RICHI’s vision to build a first-class enterprise, to foster first-class employees, and to make first-class contributions to society has never wavered.
In the past three decades, we have expanded our business to a wide range of areas, including animal feed mill equipment, aqua feed equipment, pet feed equipment, biomass pellet equipment, fertilizer equipment, cat litter equipment, municipal solid waste pellets equipment, etc.
1995
RICHI Established
2000+
Serving More Than 2000 Customers
120+
RICHI Employees
140+
Exported To 140 Countries