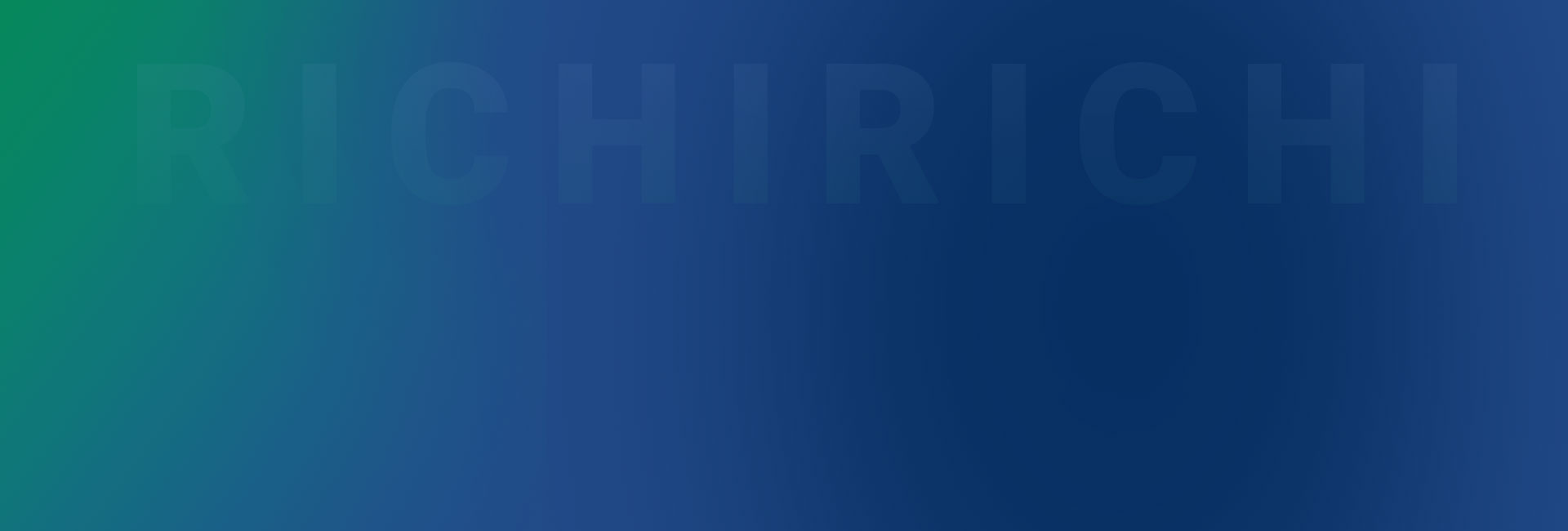
PET FEED MILL
The pet feed mill is a processing system specialized in manufacturing dog, cat, ornamental fish and other types of pet animal feed. The pet feed mill plant usually includes a series of processes from silo, raw material cleaning, crushing, mixing, extrusion, drying, cooling, screening, packaging, etc.
Pet food made by RICHI pet feed processing technology has the advantages of comprehensive nutrition, high digestion and absorption rate, scientific formula, quality standards, convenient feeding and use, and can prevent certain diseases.
In addition, we customize pet feed production line design plans with different outputs and specifications according to the needs of different customers, and optimize the configuration of the plan, simplify the process, save costs, and improve the market competitiveness of pet feed factories.
- Capacity: 1-60 T/H
- Pet feed mill cost: 100,000-5,000,000 USD
- Feed Type: extruded feed
- Applicable customers: pet feed factories, aquatic feed factories, puffed grain processing factories, livestock and poultry feed factories
- Business type: New construction, expansion and renovation
Types of pet feed mill plants
According to different types of feed products, pet feed mill factories are mainly divided into:
- dog feed mill
- Cat feed mill
- bird feed factory
- Ornamental fish feed mill
- pet pig feed mill
- rabbit feed mill
- fox feed mill
- snake feed mill
- pet rat feed mill
- Pet horse feed mill
- . . .
Advantages of pet feed mill
The pet feed milling plant has the following unique advantages:
- Multiple models, with various configurations according to different outputs.
- The pet feed mill equipment can adjust the raw materials, temperature, moisture and other process parameters to make the product have the characteristics of novel shape, taste, rich nutrition and delicate structure, suitable for the tastes of different pets.
- RICHI can provide pet feed mills with various configurations and outputs, which are widely used in the production of dog food, cat food, bird food, rabbits, pet pigs, foxes, minks, monkey food, puffed corn, puffed soybeans, etc. It is ideal for different manufacturers s Choice.
- The pet feed mill has strong production capacity. The bone paste and meat paste made from animal offal and chicken racks can be added to directly expand the dog food, which solves the problem of dehydration and crushing of fresh meat, fresh bones and slaughterhouse scraps.
- The pet food production line uses flour, corn flour, soybean meal, meat meal, fish meal, bone meal, etc. as raw materials, and uses an automatic mixing system to achieve fully automatic scientific proportioning and mixing.
- The pet feed extruder extrudes various shapes, and then dries and sprays them to produce formula pet food of various shapes, balanced nutrition, and good palatability.
- Using twin-screw extrusion technology to produce pet food, the nutrients in the formula raw materials can be intact, easy to digest and absorb, and the shape of the formula is easy to change;
- The entire assembly line has optimized configuration, high degree of automation, precise control of the production process, stable product quality, high production efficiency, hygiene and environmental protection;
- Pet foods of different shapes and sizes can be replaced with molds and the expansion degree can be adjusted (Pet food shapes: heart-shaped, bone-shaped, round, triangle, small fish-shaped, square, etc. Cat food shapes: heart-shaped, bone-shaped, round, triangle , small fish shape, square, etc.).
RICHI pet feed production equipment can be customized according to customer needs. By adjusting pet feed mill process parameters such as raw materials, temperature, and moisture, the products can have novel shapes, unique tastes, rich nutrients, and delicate textures, suitable for the tastes of different pets.
pet feed mill process flow
Pet food processing technology is an important condition to ensure the quality of pet feed. Only with reliable processing equipment and scientific technological processes can high-quality compound feed be produced.
Therefore, the adoption of perfect, reasonable and flexible processes and the selection of advanced, efficient and high-quality pet food making machines will always be the standards pursued in pet feed mill design.
Nowadays, most pet feed factories adopt the process of crushing first and then batching. The process flow of pet feed mill plant mainly includes eight parts: raw material receiving, pellet crushing, batching mixing, granulation and puffing, liquid spraying, finished product discharging, electrical control and dust removal system.
The complete process flow of the pet feed factory mainly includes the following:
Raw material reception
The raw material receiving process includes conveying equipment, magnetic separation equipment, primary cleaning screens, metering equipment and vertical silos. The most commonly used raw material measuring equipment at present is the floor scale.
Small and medium-sized pet feed mill factories generally do not have two feeding ports for pellets and powder. Large pet feed mill plants should be equipped with one feeding port for pellets and 2 to 3 auxiliary materials. Cereal raw materials first enter the silo, and then are sent to the workshop by the conveying equipment at the bottom of the silo, while the powder is directly put into the discharge port and enters the batching bin.
Raw material crushing
The crushing process can be divided into primary crushing process and secondary crushing process according to the number of raw material crushing times.
The primary crushing process is simple and has low equipment investment, but its disadvantages are uneven particle size of the crushed materials and high power consumption; the secondary crushing process makes up for the shortcomings of the primary crushing process, with consistent particle size of the finished product, high output, and low energy consumption. But its equipment investment is large.
Ingredients mixing
Although with the extensive application of liquid spray technology, the saying “batching is the core and mixing is the key” will gradually become outdated, at this stage, batching and mixing are still key steps to ensure formula and feed quality, and are also the most automated steps in pet feed mill factories.
The system generally includes a batching warehouse, various batching scales, hand feeding, mixers and subsequent conveying equipment. Its core is the batching scale (including feeder) and mixer. In order to improve the accuracy of ingredients, a microscale should be used to weigh various trace elements.
But for small and medium-sized pet feed mills, in order to save investment, people often use manual feeding ports instead of microscales. The liquid addition system (scale) should be used alone for liquid addition, but with the application of post-spraying technology, the liquid scale has a tendency to be gradually replaced. Mixing uniformity and throughput are the main considerations in selecting a mixer.
Pelleting and extrusion
The pelleting and puffing system is the system with the largest investment in pet feed factories. It mainly consists of feeders, conditioners, extruders, coolers, crushers, grading screens and conveying equipment. The appearance quality and intrinsic quality of finished feed products mainly depend on the condition of this system.
In terms of technology, people often arrange the pet food extruder side by side, so that the conditioned materials can be expanded and granulated. The feeder speed must be adjustable to suit the process and the specific requirements of each piece of equipment operating.
Liquid spraying
The liquid post-spraying process is to spray various heat-sensitive elements into pet food in the form of liquid after puffing. This process is divided into two methods: “online spraying” and “offline spraying”. Online spraying means that the spraying system is located in the middle of the process. Generally rarely used. Offline spraying is to install the spraying system in the finished product discharging section of the pet feed factory.
The advantage is that it can be sprayed and sold immediately, always providing users with fresh products; in addition, using this configuration, the pet feed mill factory can only produce several kinds of standard feed, which can reduce the number of finished product warehouses. At the same time, the production flexibility of the pet feed mill has also been greatly improved, and cross-contamination has been significantly reduced.
Finished product discharging
There are two forms of finished product discharging: packaging and bulk. Advanced countries in Europe and the United States use a large number of feed bulk trucks due to their relatively developed transportation.
Packaging is divided into two types: manual and automatic. Most small and medium-sized pet feed mill factories use manual packaging. When choosing an automatic packaging system, you should pay attention to the accuracy and stability of the packaging scale and the working reliability of the automatic bag sewing machine.
Electrical control
The electrical control system is a concentrated expression of the automation level of the pet feed mill. Due to differences in production scale, labor costs and investment capabilities, the degree of automation of each pet feed mill factory shows great differences.
At this stage, most of them have computer-controlled batching systems, and there are few feed factories that use computer automatic control for the entire factory. As far as the batching system is concerned, its control function is also relatively monotonous.
Dust removal system
Pet feed mills tend to produce a large amount of dust during the production process. In order to control dust pollution, protect the health of operators, and maintain the normal operation of equipment, it is essential to set up a reasonable dust removal system.
The dust removal system mostly adopts single-point suction dust removal and centralized air network combination dust removal. The specific dust removal method to be used should be determined according to the specific situation.
Since its establishment, RICHI Machinery has been committed to developing and producing high-quality pet feed machinery and equipment to meet the needs of agriculture and animal husbandry. RICHI has researched and developed various types of pet food production lines, and configured different types of pet feed mills according to different outputs.
pet feed mill plant projects
At present, pet feed factory projects undertaken by RICHI have appeared in many countries around the world, such as the United States, Canada, Australia, Italy, New Zealand, etc. Different outputs, different process designs, different levels of equipment configurations, and different degrees of automation will ultimately determine the investment cost of a pet feed factory. Even with the same output, project investment will vary greatly depending on equipment configuration and silo system size.
If you are interested in investing in pet feed processing business, you may wish to contact us to design a pet feed factory that suits your needs. We will provide you with customized services based on your budget, factory building, and product type.
10 T/H pet feed mill plant in Russia
- project date: 2020.09.03
- Feed Type: Pet & Aqua Feed
- Equipped with silo system
- pet feed mill cost: 1,580,000 USD
5 T/H pet feed mill plant in Canada
- project date: 2021.9.27
- Feed Type: Dog & Cat Food
- No silo system configured
- pet feed mill cost: 570,000 USD
2 T/H pet feed milling Plant in iran
- project date: 2020.10.11
- Feed Type: Dog & Cat & fish Food
- No silo system configured
- pet feed mill cost: 340,000 USD
8 T/H pet feed mill in united states
- project date: 2020.06.15
- Feed Type: Various pet food
- No silo system configured
- pet feed mill cost: 930,000 USD
6 T/H pet feed mill in australia
- project date: 2023.06.11
- Feed Type: Pet & Fish Feed
- Equipped with silo system
- pet feed mill cost: 1,210,000 USD
4-5 T/H pet feed plant in india
- project date: 2020.07.28
- Feed Type: Pet & Aqua Feed
- Equipped with silo system
- pet feed mill cost: 920,000 USD
3.5-5 T/H pet feed mill in thailand
- project date: 2019.05.07
- Feed Type: Dog & Cat & Fish Food
- Equipped with silo system
- pet feed mill cost: 790,000 USD
3 T/H pet feed mill in singapore
- project date: 2022.07.12
- Feed Type: Dog & Cat Food
- Equipped with silo system
- pet feed mill cost: 460,000 USD
Below, RICHI will show you several pet feed processing plant projects we have done from the aspects of construction cost, construction content, raw materials, energy consumption, process design and other dimensions.
2 T/H pet feed mill plant project in new Zealand
—— RICHI MACHINERY ——
- Annual output: 10,000 tons
- Pet feed mill project investment: 480,000 USD
- Degree of automation: fully automatic
- Number of employees: 30 people
- Work system: 2 shifts, 8 hours per shift, 300 days a year
- Raw materials: corn 6000 t/a, meat 2000 t/a, oil 500 t/a, rice 1000 t/a, protein powder 500t/a
- Water 960t/a, natural gas 750,000 Nm3/a newly added, electricity 2.2 million Kwh/a
- Main equipment: crusher, meat grinder, mixer, packaging machine, 2-ton alcohol-based fuel boiler, extruder, drying box, spraying machine, etc.
2T/H pet feed mill process design
- Ingredients: The purchased raw materials are all clean and impurity-free raw materials, so the raw materials do not need to be cleaned. Corn and rice are directly transported to the ingredients warehouse through the elevator and weighed according to a certain ratio.
- Feeding and crushing: Send the proportioned materials into the crusher for crushing. Dust will be generated during the process. Then enter the mixing process. Chicken, beef liver, fish and other meats are sent to the meat grinder to be crushed, and then sent to the reactor for steaming aging.
- Mixing: Put the various crushed raw materials, meat powder, and protein powder into the mixer through the gate for uniform mixing.
- Puffing: The material is crushed and expanded to form columnar feed. As the die rotates, it is cut into granular feed by a cutter fixed outside the die.
- Drying: After the material is extruded by the extruder, it forms wet and soft particles (moisture content is 25% to 30%), and then enters the oven for drying to reduce the moisture content of the material dropped to about 13%.
- Cooling: Cooling is to reduce the temperature of the material to the safe range of the product.
- Oil spraying: In order to enhance the palatability and flavor of the product, put the oil into the selected cylindrical turntable and spray mist liquid on the surface of the product.
- Packaging: After the material is sprayed and cooled, it becomes the finished product. The finished product enters the packaging scale by opening the pneumatic door. After automatic measurement and discharge, the bag is automatically loosened and ready for packaging on the truck.
4T/H pet feed mill project in italy
—— RICHI MACHINERY ——
- Annual output: 30,000 t/a
- Pet feed mill investment: 870,000 USD
- Number of employees: 30
- Work system: Implement three shifts, each shift works 8 hours, and works 300 days a year.
- Raw materials: corn 10150t/a, meat meal 7250t/a, rice 2900t/a, sub-flour 2900t/a, animal fat 2900t/a, protein powder 2900t/a, chicken liver 950t/a, monosodium glutamate, salt 13t/a, vitamin 12.5 t/a, amino acid 12.5t/a
- Pet food equipment configuration level: medium.
- Main equipment: conveyor, mixer, ultrafine pulverizer, extruder, cooler, pulse dust collector, belt dryer, packaging scale, fully automatic batching scale, etc.
4T/H pet feed mill process design
- Pour the raw and auxiliary materials into the hopper, and then rush them to the impurity removal screen through the conveying auger.
- After screening, the powder is put into the batching bin. According to the requirements of the formula, the raw and auxiliary materials are automatically weighed in proportion through the batching auger.
- After it is finished, it enters the mixer. After mixing and stirring, it is transported to the permanent magnet cylinder through the spiral auger.
- After removing iron impurities, it enters the bin to be crushed.
- Then it is crushed by the pulverizer and passes through the powder inspection screen before entering the mixer again, and then stirs evenly.
- The final material is extruded into pellet pet feed, and then dried in a drying box, and then enters the linear vibrating screen for screening.
- The qualified feed enters the sprayer, sprays grease and meat slurry onto its surface, and passes through the conveyor after spraying.
- After the feed is fully mixed, it is cooled to normal temperature and then enters the mixer.
- The mixed feed passes through the feeder and enters the linear vibrating screen for screening and then enters the finished product bin. Then it is packaged by the packaging scale to become the finished product.
10-11 t/h pet feed mill factory in united states
—— RICHI MACHINERY ——
- Annual output: 80,000 t/a
- Project investment: US$3.2 million (Contains multiple large silos, fully automatic palletizing system, and vacuum spraying system)
- Construction content: Mainly build independent production workshops, laboratories, raw material warehouses, premix workshops, packaging workshops, office buildings, cold storage, finished product warehouses, security rooms, grease warehouses, and silos and other buildings and structures.
- Work system: 82 employees, implement three shifts, each shift works 8 hours, and works 300 days a year
- Main raw materials: wheat 7000t/a, corn 35000t/a, soybean meal 2000t/a, rice 4000t/a, meat meal 11500t/a, animal fat 8000t/a, corn gluten meal 5000t/a, fish meal 1500t/a, sugar beet meal 500t /a, fresh meat 3500t/a, salt 450t/a, citric acid 300t/a, amino acids 280t/a, etc.
10-11 t/h pet feed plant process design:
- First, the purchased raw and auxiliary materials such as corn, wheat, and rice are added in a certain proportion and then crushed through a grinder, and then the auxiliary materials are added and stirred evenly.
- The mixed material enters the puffing process. The material is suddenly decompressed when heated and pressurized.
- The moisture in the material vaporizes and expands, resulting in many small holes and becoming brittle, forming puffed feed.
- After the material is extruded by the pet food extruder, it is dried in an oven to remove most of the moisture in the material.
- The dried pet food pellets enter the spraying machine, and the grease and meat slurry are sprayed onto the surface.
- The sprayed pet feed pellets enter the cooler to be cooled to normal temperature, and then are screened and selected before being put into the warehouse and packaged for sale.
- Qualified products are returned to the crushing process and reused in production.
equipment needed to start pet feed mill plant
As a leading company in the field of pet feed mill machinery and equipment, we have advanced production equipment and technical teams. Our products include crushers, mixers, pet feed extruders, vacuum spraying machines, pet feed dryers, coolers, screening machines and other main equipment as well as lifting and conveying equipment, dust and iron removal cleaning equipment, puffing drying and spraying equipment, intelligent chemical control equipment, etc.
These equipment for pet food production have the characteristics of high efficiency, energy saving, durability, etc., and can meet the needs of pet feed processing enterprises of different sizes.
pet Food Grinder
Capacity:
3-25T/H
Main Power:
30-160KW
pet Food Extruder machine
Capacity:
1-12T/H
Main Power:
0.75-355KW
The selection of pet feed mill equipment should meet the requirements of pet feed factory technology, be safe and reliable, easy to use and maintain, energy-saving and efficient, and meet environmental protection requirements. Use standardized, serialized and universal parts and components equipment as much as possible.
pet feed mill equipment layout design
The principles of pet feed mill equipment layout should first be to ensure the smooth flow of the production process, and secondly to facilitate installation, maintenance and operation, ensure safety and be economical and reasonable. Generally, multi-story buildings should be used for the construction of large and medium-sized pet food factories. The structure can be a steel structure or a reinforced concrete structure.
- Ensure smooth production process flow. The arrangement of equipment should be carried out in accordance with the process sequence, and the building height should be used as much as possible to keep the logistics, reduce the number of liftings, and save land and building area.
- Easy to install and maintain. Equipment should be arranged neatly, with sufficient safe walkways and operating and maintenance distances. Maintenance hooks should be installed above large equipment. The load and height of the hooks should be determined according to the maximum load and minimum lifting requirements of the equipment.
- Easy to operate and ensure safety. The operating points of the pet feed equipment should be within human reach and easy to operate. Safety railings must be installed on stairs, walkways, roofs, roofs and operating surfaces. All rotating equipment parts must be equipped with protective covers.
The Prospects of Pet Feed Processing Business
Population growth and urbanization have led to a surge in pet ownership around the world. Pets such as dogs and cats are now considered important members of many households, driving the demand for pet food. Likewise, demand for meat and dairy products from livestock such as poultry, cattle and pigs has also increased due to global population growth and changing dietary preferences.
As the population grows, so does the demand for animal-derived products such as meat, milk, and eggs. The intensification of livestock production has led to higher requirements for animal feed to meet this demand. Livestock animals require a balanced and nutritious diet to ensure their health, growth and productivity, which drives the demand for animal feed.
Therefore, the increasing number of pets and domestication of animals require high feed rates to ensure hygienic growth of farm animals, which is expected to drive the growth of the global pet feed processing market.
FAQs of pet feed mill construction
What are the main production costs of a 1-20 T/H pet feed mill plant?
The production cost of pet food is the same as that of feed production, but the proportion of costs in various aspects is different, especially in some areas (such as drying, energy, equipment maintenance fees, etc.). In addition, the processing costs of pet food factory products are very considerable. Therefore, the cost of each product is evaluated independently.
(1) Product shrinkage rate
The moisture content of the raw materials when entering the pet feed mill production workshop is between 10% and 13%, and the moisture content of the dry and expanded pet food for sale is between 8% and 10%. Therefore, the direct shrinkage in weight will cause corresponding economic losses.
The waste, powder and residue caused by the starting, stopping and continuous operation of the pet feed mill equipment also cause the shrinkage of the products. The shrinkage rate of the products produced by the dry puffed pet food factory is generally 3% to 5%.
The crumb generated during processing can be recycled as part of the formulation after drying and grinding. The recycling level is between 5% and 20%, depending on the actual situation.
(2) Energy
Energy utilization is to generate steam and electricity in the form of fuel. Compared with the production of ordinary feed, the production of dry extruded pet food requires more energy. Energy requirements will vary depending on the process and method. A 3-year study compared the total energy consumption of two types of feed processing, and the latter required approximately 7 times the energy of the former.
(3) Energy consumption
The energy consumption in the pet feed mill production process is critical to the economic benefits of the puffing workshop. A typical workshop can use electricity, natural gas, and oil as energy sources. Electricity is used to start all engines, and natural gas or oil is used to heat water and provide steam for expansion and drying.
Although energy costs are related to profits, compared with a 1% to 2% change in recipe cost and a 1% to 2% change in public procedure cost, the former has a benefit impact that is 16 to 32 times greater than the latter. A 2% reduction in puffing and drying costs will save $4,700 per year, while a 1% reduction in raw material costs will save $70,000 per year.
The above data are based on pet feed mill equipment operating 5 760 hours per year with an average net production capacity of 7 t/h.
(4) Maintenance
During the expansion process, energy is transferred from the surface of the expansion machine to the product, which results in high wear rates and high maintenance and replacement costs. Comparing the maintenance and repair costs of a puffing workshop and a dry puffed pet food production workshop, the latter is about 2 to 3 times that of the former.
(5) Labor
For the puffing/drying production department, the labor cost is smaller. 1 worker can control 2 complete pet food production lines from the extruder inlet to the dryer outlet, or if a 2nd operator controls the dryer, 1 worker can effectively manage 4 extruders per section. Labor costs are certainly lower than equipment maintenance fees.
I want to enter the pet feed industry and invest in a pet feed mill factory in the United States. What issues should I consider?
Individuals or companies that decide to enter the pet food industry should consider today’s pet food industry from the following aspects.
(1) Market
A comprehensive market analysis is a must before deciding to enter the market. The pet food industry in the United States is a mature industry with an astonishing growth rate over the past 20 to 30 years, which is very attractive to investors. However, in recent years, competition has become increasingly fierce and the growth rate has stabilized. In most markets, new entrants must crowd out some of the existing suppliers’ markets.
(2) Early investment
Compared with animal feed mills, extruded pet food manufacturers require complex and expensive equipment. Therefore, there must be enough sales volume to cover the maintenance costs and low-cost production. Extruding and/or packaging equipment needs to be purchased and installed first.
(3) Total production cost
In addition to fixed production costs, there are variable costs for producing extruded pet food (such as labor, use and maintenance costs), which may be 2 to 3 times that of feed production, especially if all or most of the products require packaging.
(4) Environmental sanitation and good production operation regulations
Feed manufacturers who want to enter the pet food market must understand factory hygiene standards and the U.S. FDA’s Good Manufacturing Practices. And the food industry chain will have its own hygiene and infection standards, which suppliers must meet.
Changing consumer demands and launching new products have created a completely competitive market. But those producers who are committed to producing nutritionally reliable, high-quality products continue to capture more of the market, and new producers are constantly joining.
What should be considered in pet feed mill layout design?
Things that need to be considered when designing the pet feed mill layout are as follows:
Pet feed factory layout design requires reasonable arrangements for various production and living buildings, roads, docks, utility pipelines, and greening in the factory area.
- Whether the investment intensity can meet the requirements of various local industrial parks.
- Determine the location and direction of the pet feed mill factory gate according to the red line map provided in the industrial park.
- The spacing between factories should consider the relevant requirements of the fire protection law and the convenience of logistics vehicles passing through.
- When designing the elevation of the building, the overhead engineering pipe network and the underground laying construction plan, the local climate environment and geology and landforms should be considered.
- The design of logistics in the factory should prevent the intersection of human flow and logistics as much as possible, and the operational safety of the enterprise should be taken into consideration during the pet feed mill design.
- Understand the latest regulations, specifications and standards in the pet feed industry.
- Multiple options should be compared and the best option should be selected.
How to design the process of pet feed mill?
The process design of a pet feed factory is a relatively complex task. A good process design not only guarantees the quality of the product, but also reduces investment and use costs, and is both aesthetic and practical. At the same time, process design also needs to be quite flexible and adaptable to meet the needs of producing various products.
Things to consider in pet feed mill process design:
- Based on the description of the product line and raw materials in the early preparation stage, select the process specifications and determine the process.
- According to the description of the pet food production process, calculate the process parameters and select the process equipment.
- Based on the determined production process, determine the power, dust removal, odor removal, and noise reduction plans required for the process.
- With reference to ergonomics, formulate process operation procedures and determine program control methods.
- Do a good job in designing and determining the enterprise information network.
Before we design the pet feed mill process for you, we need to know the following information:
- The expected scale of the pet food factory, the commercial radius of the product, and the customer’s product usage habits.
- Product varieties, specifications and classification of product lines as required by regulations.
- Types, quality specifications, physical properties (including density, fluidity, storage conditions, etc.) and receiving methods of raw materials.
- Product formula composition and expected dosage of raw materials.
- Specific indicators of process design, such as requirements for mixing, liquid addition, granulation, extrusion and puffing, etc.
- Equipment that can be purchased or customized to meet relevant parameters.
Here is some information that customers can provide to us, but for customers who are entering the pet feed processing industry for the first time, we need to provide it to them. If you have any questions about this, please contact us directly online, and our technical consultants will provide you with free consulting services in order to provide detailed suggestions and plans for pet feed mill factory construction!
What does the scope and content of pet feed mill process design include?
The scope of pet food factory process design mainly includes the process design of direct and indirect production parts such as production workshops (main and auxiliary material processing workshops), vertical cylinder warehouses, auxiliary material warehouses, and finished product warehouses. Process design is a comprehensive and comprehensive work, which is not only technical and economical, but also a highly artistic work.
The task of pet feed mill process design is to prepare process design documents and design process drawings.
1. Pet feed mill process design documents
- Overview of product types and output, description of types, quality and annual use of main and auxiliary raw materials.
- Description of the contact between each production department.
- Process flow description (with pet feed mill flow chart).
- Process equipment selection calculation and animal feed mill equipment list.
- Calculation of requirements for water, electricity, steam, coal (oil), etc.
- Equipment, materials, and power cost estimates.
- Overview of labor organizations and work systems in factory workshops and warehouses.
2. Pet feed mill process design drawings
- Pet food manufacturing plant process flow chart.
- Main workshop, vertical cylinder warehouse, auxiliary material warehouse, equipment floor plan, longitudinal and transverse sections.
- Diagram of pre-embedded and overhead footing holes on the floor where the equipment is installed.
- Equipment layout and installation drawings.
- Ventilation and dust removal air net.
- System diagram of steam, compressed air and liquid addition system for production.
- Non-standard and referenced standard equipment diagrams for various types of supporting process equipment.
3. Basis for process design and materials to be mastered
- The proposed scale of the pet feed mill.
- Product varieties and specifications and development requirements.
- Pet food formulas and varieties and physical properties of commonly used pet food raw materials.
- Collection and distribution methods of raw materials and finished products.
- Investment scale and implementation steps.
- Process design indicators and personnel quality of the proposed factory.
- Comprehensive overview of domestic and foreign pet feed mill factories of the same scale.
- The technical level, performance and quotation of relevant processing techniques and equipment at home and abroad.
I want to open a 10 t/h pet feed mill. How to develop cat and dog pet feed?
1. Nutritional needs of cats and dogs
(1) Cat
Cats are omnivorous animals that eat mainly carnivores. They are lively and active and have a strong metabolism. They need sufficient nutrition to grow normally. Protein is the basis of life. It is an essential substance to maintain the healthy growth and muscle activity of animals, so comprehensive and balanced protein is needed. Taurine (aminocaproic acid) promotes the normal growth of the cat’s retina and ensures the cat’s sharp vision. Fat is the solvent for fat-soluble vitamins and also provides the body with unsaturated fatty acids that cannot be synthesized or are insufficiently synthesized in the body. Linoleic acid makes the cat’s fur shiny. Vitamins are necessary to maintain normal physiological activities. Cats can synthesize vitamin K, vitamin D, vitamin C, vitamin B12, etc. Vitamin A is particularly important for cats’ vision, but excessive intake can be toxic. Carbohydrates and moderate amounts of fiber can provide energy and improve digestion. Calcium is the main component of bones and teeth, and plays a supporting and protective role in bones and teeth.
(2) Dog
Dogs and cats have very similar living habits and nutritional requirements. Dogs are omnivorous animals that eat mainly carnivores. Because dogs are active, are usually larger than cats, and have a strong metabolism, their nutritional needs are greater than that of cats. Dogs can synthesize vitamin C but cannot digest cellulose. Cats and dogs of different breeds, ages, and physiological stages have slightly different nutritional needs and dietary characteristics.
2. Development ideas for cat and dog pet feed mills
(1) Development principles:
For a pet feed mill, according to the nutritional needs and eating habits of cats and dogs, four principles for developing pet feed for cats and dogs can be drawn up:
- Staple food nutrition should be comprehensive;
- The variety of various types of feed should be varied;
- Treat differently, and prepare different types of feed according to the nutritional needs and dietary characteristics of different breeds, different ages, and different physiological stages. Domestic cats can mainly eat plant food, while foreign cats should mainly eat animal food. During the development period, During pregnancy and lactation, protein, vitamins, minerals, etc. should be increased;
- Hygienic, non-toxic, and good palatability.
(2) Develop raw materials:
Cats and dogs are omnivorous animals that mainly eat meat. Their staple food is meat, fish and their by-products. Slaughter leftovers such as blood clots, offal, and bone meal are all good staple food raw materials. Milk, eggs, grains, potatoes, vegetables, etc. are good auxiliary raw materials for cat and dog food. In particular, the by-products of various raw materials are also good feed ingredients, which provides cheap and abundant raw materials for the production of pet feed.
(3) Pet feed variety development:
If you want to build a pet feed mill, the following products are recommended for you to develop.
Utilizing the technology of developing human food and learning from foreign successful experiences in developing pet feed, we can consider developing main feed (cat food, dog food), auxiliary feed, health feed, etc. The colors and varieties of each type of feed should be varied.
The main feed requires comprehensive nutrition, richness, good palatability, easy digestion and utilization, easy preservation, and easy portability. Cat food is mostly made into granular, bread-like, and biscuit-like dry food. Dog food is mostly made into dry, semi-moist and wet types. The main ingredients of powdery, biscuit, granular and puffed dry foods are starch, meat meal, fish meal, germ, etc.
- Semi-moist dog food is mostly meat, dairy products, soybeans, oils, minerals, etc. It is very suitable for newly weaned puppies and can be made into pastries, pies, sausages and other shapes.
- Wet dog feed is characterized by very good palatability and is generally made into cans. The leftovers from meat factories are often processed into canned dog food.
- Supplementary feeds are feeds with relatively single nutrients and bright colors. Its main function is to regulate appetite, and some are used by animals to grind their teeth or lick plates.
- Health care feed is a type of feed that adds specific nutrients to meet the special nutritional needs of animals and promote body functions. Such as taurine-fortified feed, calcium-fortified feed, dietary fiber, linoleic acid-fortified feed, etc.
(4) Examples of staple food recipes for cats and dogs:
Below, we show you several pet feed formulas, which have been used in some pet feed mill products on sale.
- (Example 1) Cat feed formula (in kilograms): 300 grams of rice, 300 grams of cornmeal, 390 grams of meat, 10 grams of salt.
- (Example 2) Cat food formula (in kilograms): 100 grams of casein, 200 grams of milk powder, 350 grams of beef liver, 300 grams of oats, 50 grams of edible oil.
- (Example 3) Dog food formula (in kilograms): 250 grams of meat, 150 grams of rice, 150 grams of noodles, 300 grams of vegetables, 70 grams of milk, 10 grams of lard, 10 grams of cod liver oil, 6 grams of yeast, 30 grams of carrots, 14 grams of bone meal and 10 grams of salt.
- (Example 4) Cat food ingredients: cereal grains and their by-products, fish and meat and their by-products, sugar, vegetable oil, iron oxide red, vitamins, antioxidants. Finished product standards: protein ≥ 22.0%, fat ≥ 5.0%, cellulose ≤ 5.0%, salt ≤ 2.0%.
- (Example 5) Ingredients of dry puppy food: corn by-products, meat and its by-products, vegetable oil, iodized salt, vitamin A, vitamin E, vitamin B, riboflavin, antioxidants. Finished product standards: natural protein ≥ 28%, natural fat ≥ 10%, calcium ≥ 0.6%, minerals ≥ 1.5%, cellulose ≤ 5.0%, salt ≤ 1.3%.
- (Example 6) The characteristics of cat food are: 100% comprehensive and balanced nutrition, special taurine formula, ensuring an appropriate amount of vitamin A, ensuring an appropriate amount of calcium, adding linoleic acid, adding fiber, and comprehensive and balanced various proteins.
If you want to process cat and dog food, please contact us to get a full set of customized solutions and equipment quotations for cat and dog pet feed factory processes!
I want to build a 2 t/h cage bird pet feed mill. How to develop cage bird pet feed products?
Cage birds kept at home are mostly omnivorous and herbivorous birds. Their main feed is mostly plant food. Birds digest quickly and are very sensitive to hunger, but they eat less food per meal, and their feed is mostly made of pellets or powder.
- Daily feed for cage birds can be divided into main feed, auxiliary feed, health feed, special feed, mineral feed and insect feed.
- The main feed is starchy food, and the raw materials that can be used include rice, millet, millet, corn, and sorghum.
- Supplementary feeds are generally fat-containing feeds, such as perilla seeds, hemp seeds, rapeseeds, pine seeds, and sunflower seeds, which are suitable for consumption before moulting and nesting.
- The raw materials of health-care feed are mainly green vegetables and wild vegetables. The powdered feed can increase appetite, increase vitality, and is beneficial to health and reproduction. Birds should eat health feed every day.
- Special feeds include estrus feed, aphrodisiac feed, and pigment feed. During the estrus period in spring, birds need more protein, especially animal nutrients. The feed prepared for this is estrus feed, using eggs and millet as the main raw materials. The main purpose of aphrodisiac feed is to increase the proportion of egg yolk in bird food. Pigment feed is mainly aimed at birds during the moulting season. Feed them with food containing carrots and peanut oil to make their feathers red and bright. Mineral feed is mainly formulated from shell powder, feather meal, eggshell powder, cuttlefish meal, salt and gravel. Insect feed is indispensable for cage birds. Without feeding live insects to the birds, it will be difficult to raise the birds well.
Therefore, bird-eating insects can be specially cultivated and sold live, or they can be freeze-dried to maintain their original shape or sold into powder. Commonly used insect raw materials include skinworms, mealworms, locusts, silkworm pupae, etc. If you want to start bird feed processing, contact us to get a professional bird feed production line solution and a complete set of caged bird pet feed mill factory equipment quotations!
I want to build a 1 t/h ornamental fish pet feed mill, how should I develop the product?
Ornamental fish, like several other pets, require six balanced and comprehensive nutrients. The difference is that fish live in water, like to eat bait, and their food intake is small. Their food is relatively simple, and only the main feed can meet their needs. Bait can be divided into natural bait and synthetic bait.
- The development of ornamental fish pet feed can, on the one hand, breed animals and plants that fish like to eat and sell them directly; on the other hand, it can be artificially synthesized and produced into micro-granular products.
- Natural feed is nutritious, easy to digest, and is especially helpful in promoting the development of gonads. Commonly used natural baits include animal baits such as water fleas, water earthworms, and paramecium, as well as plant-based baits such as fresh vegetables and duckweed.
- Artificial synthesis is the main method. Micro-granular fish pet food is convenient, hygienic and easy to preserve.
Here is an example of a recipe: 30% silkworm chrysalis powder (skimmed), 10% fish meal, 60% barley flour or bread flour, a little baking powder, a small amount of salt and multivitamins.
Other pets such as beetles, frogs, rabbits, etc., as well as piglets that are becoming new favorites, have similar feed development ideas and methods to the above.
If you want to process pet feed pellets, no matter what kind of pet food it is, welcome to contact us to get professional family support and build your pet feed mill plant!
Since the development of pet feed in many countries is still in its infancy, pet feed mills and pet feed companies can use the following methods to develop the market.
- Enter joint ventures and cooperation with other pet feed mills and pet food companies in the world;
- Cooperate with domestic animal research institutions or animal protection institutions to develop own products;
- Food production companies can take advantage of technology and equipment to develop novel pet feeds such as pet staple food, beverages, snacks, health products, etc.;
- Since “palatability” is the highest principle when choosing food for pets, if it is difficult to surpass those products of foreign companies, they can also be used as “supplements” to adapt to different health states such as cubs, pregnant animals, and birthing animals. Need, ride sales;
- First expand the company’s reputation in the pet field by providing pet services such as medical care, leasing, marriage, foster care, training and development of toys, appliances and clothing for cats and dogs, and then enter the pet feed market.
About RICHI Machinery—— Pet Feed mill supplier
RICHI was founded in 1995. After nearly 30 years of development and growth, it has grown into a company that integrates R&D and manufacturing of pet feed factory machinery and engineering, grain machinery and engineering, conveying equipment and engineering, steel structure engineering, automation control technology and engineering, etc. , a modern enterprise integrating engineering design and installation.
The company has fully passed ISO9001 quality management system certification; electrical appliance manufacturing 3C system certification; feed industry standardization committee unit; feed processing equipment engineering technology research center; high-tech enterprise.
RICHI has invested heavily in software and hardware, including SOLIDWORKS PDM design platform, SAPERP system, and FPD process information management system. Investment in high-power laser cutting machines, CNC bending machines, CNC processing machine tools, CNC welding machines, slide tube bending forming production lines, spray baking production lines and other high-precision equipment.
RICHI has strong and efficient operational capabilities in market development and services, product R&D and manufacturing, project management and delivery. The company has developed more than 80 series and more than 400 varieties of various superior-performance feed machinery products, and can undertake turnkey projects from various pet feed mill factories, animal feed mill plants, poultry feed plants, fully automatic cattle feed plant, floating fish feed mills, shrimp feed mills, etc..
Careful design, exquisite manufacturing, meticulous construction, all-round services and RICHI’s long-term philosophy of “continuously creating great value for customers” have enabled RICHI to win long-term recognition and good social reputation from many pet feed mill factories around the world.