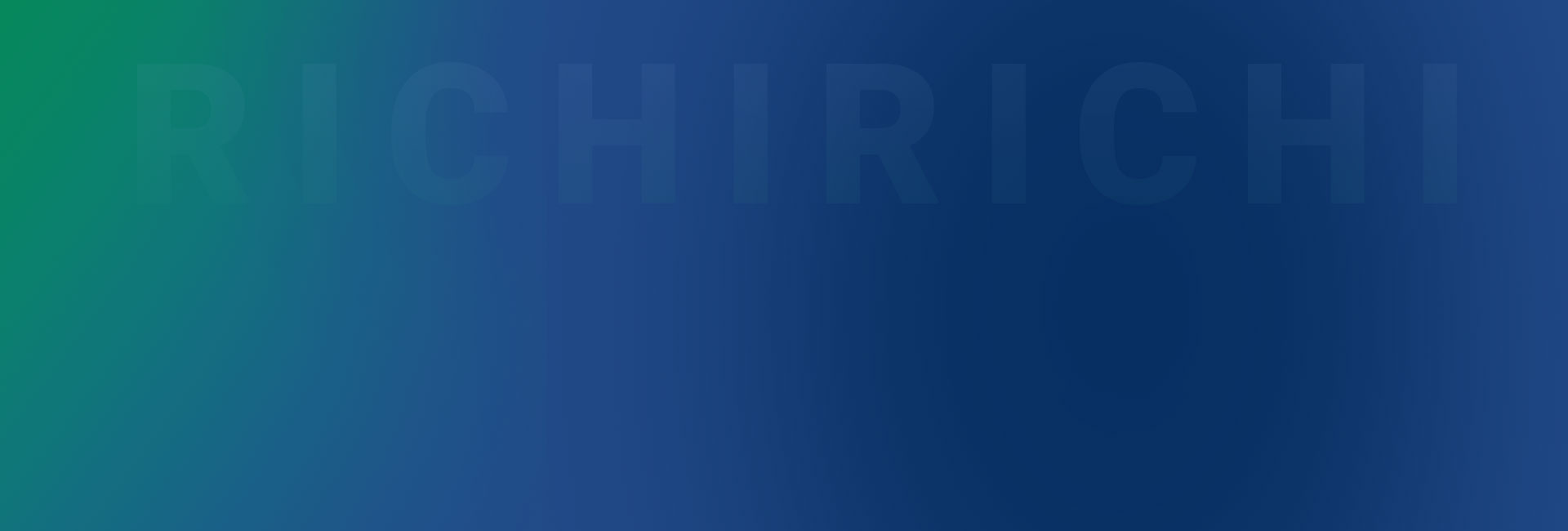
Feed Mill Engineering
Feed mill engineering is a feed processing system built through civil engineering, process design, equipment installation, etc.
According to customer needs, land area, feed type, we can provide customers with customized whole-plant layout design, equipment manufacturing and installation, operation training and other services.
- capacity: 100-120T/H
- cost: 2,300,000-3,500,000 USD
- Total project power: 1450-2400KW
- Land use suggestion: 8000-30000m²
- Estimated installation period: 200 -300Days
designer & manufacturer
Our extensive experience and depth of expertise allow us to anticipate your needs regardless of the project.
We don’t just assume we have the finest engineers, designers, construction personnel, and support staff to provide you with the most innovative solutions available, we are constantly providing training to add to our teams depth of understanding.
turnkey solution supplier
We have a professional technical team to tailor personalized system solutions for you, providing one-stop services from early design, manufacturing to later construction, maintenance, etc. We are committed to customizing personalized solutions for the entire feed mill engineering such as animal energy feed, bio-fermented feed, ruminant feed, aquatic feed, pet feed, etc.
RICHI MACHINERY
types of feed mill engineering
Feed mill engineering can cover the processing of livestock and poultry feed, aquatic feed, and pet feed of various sizes and types.
poultry Feed Mill Engineering
The feed mills we offer can process a variety of poultry feeds, which can meet the high nutritional requirements needed to optimize poultry’s growth and development.
cattle Feed Mill Engineering
Partner with RICHI Machinery to navigate the complexities of cattle feed production and drive your operations towards a sustainable and prosperous future.
pig Feed Mill Engineering
The feed mills and equipment we provide ensure that swine feeds are manufactured from the highest quality ingredients with a stringent quality control program.
livestock Feed Mill Engineering
The feed mills can be used to process nutritionally balanced feeds for cattle, sheep, pigs, and more, which can nourish livestock and enhance their well-being.
fish Feed Mill Engineering
As one of the most reliable fish feed mill manufacturers, we have worked on a number of projects involving aqua feed and have always achieved the results that our customers expected.
shrimp Feed Mill Engineering
RICHI Machinery designs and manufactures all the key processing technology and equipment necessary for complete shrimp feed mill engineering solutions for the shrimp feed industry.
pet Feed Mill Engineering
We are strongly committed to excellent performance and the quality of our pet feed mill solutions and production machines, making us a strong partner for our pet feed producer customers.
premix Feed Mill Engineering
Our deep roots in the traditions for green, yet efficient premix feed mill technology commit us to safe, sufficient and sustainable food production for all generations to come.
broiler Feed Mill Engineering
RICHI’s chicken broiler feed mill engineerings can be used to process many varieties of broiler food including mixed corn, feed pellets, grits, mash and blocks.
hen Feed Mill Engineering
Our hen feed mills can be used to process hen feeds, which can cover hen’s nutritional requirements needed to maximize hen health and egg production.
horse Feed Mill Engineering
Whether you’re considering modernizing your existing facility, or need expert guidance for planning and establishing a new horse feed mill, RICHI is your trusted partner.
bird Feed Mill Engineering
Our bird feed mill engineerings can process turkey feed, which can meet the dynamic and changing nutritional demands of your growing birds, pigeons, quail.
Different feed sizes and forms
With our feed mill engineering solutions and equipment, the following feed types can be processed:
pellet feed
grass feed
aqua feed
pet food
premix feed
RICHI MACHINERY
process design of feed mill engineering
Feed processing technology is the entire production process from the receipt of raw materials to the delivery of finished products (compounded powder or pellet feed). The complete feed mill engineering technology includes: raw material receipt, cleaning, crushing, batching, mixing, granulation, cooling, crushing, screening, finished product weighing and packaging and other main processes, as well as ventilation and dust removal, oil and fat addition, enzyme addition, raw material storage and other auxiliary processes.
100-120T
High automation and intelligence
100-120T
High return on investment
100-120T
Customizable design
100-120T
Service life of more than 20 years
1
Grinding System
The process of processing raw materials into the desired size. The finer the raw material, the more surface area is exposed to heat and moisture to achieve gelatinization in conditioning. Finely textured material can transfer its energy to the animal compared to ground material. This is a very energy intensive process in feed mill engineering.
2
batching system
Batching is the process of putting each material in proportional ratio called feed formulation, which is a very important process for every feed mill. Accurate material rationing will provide better quality and complete nutritional feed. This batch process can be computer controlled or can have a manual control room to reduce the cost of the mill.
3
Mixing System
Mixing as the name implies is a process of mixing micro ingredients together. Proper mixing can be defined by a unit called coefficient of variation. The smaller the coefficient of variation, the higher the quality of the mix. The mixing machine should have a design to mix liquids into it as it is necessary to add oil or molasses to the feed.
4
Granulation System
Granulation is the main step in almost any feed mill engineering. It is a process that converts any powder into a solid shape called pellets with ring die pellet machine. In this process, the powdered material is extruded through a well-designed die with the help of rollers, which converts it into granules.
5
Cooling System
Cooling is a process of removing heat. As we know, during conditioning, we generate heat and moisture through the extrusion process and heat through the tray process. But the feed pellets should have standard moisture and heat to reach its storage life and keep it free from bacteria.
6
Crumbling System
Crumbling is the process of breaking the cooled pellets into small particles to make them suitable for chicks or hens. When crumbling is not required, we bypass the feed directly onto the screen with the help of a bypass mechanism. A well-designed one should have the ability to break the pellets without becoming finer.
7
Screening System
Screening is required to remove fine particles and oversized particles. Screening machines are used to remove powder and oversized particles. Qualified animal pellets enter the packaging section, and the screened large feed pellets will be re-crumbled and powder will be re-granulated.
8
packaging section
The end of the process in each factory is bagging, also known as packaging. After screening, the finished product is filled into bags. It is a good choice for electronic bagging machines. We can also configure finished product warehouses for customers to realize the process of bulk truck loading finished feed.
advantage of feed mill engineering
high degree of automationn
The feed mill engineering has a very high degree of automation, and can realize functions such as automatic metering, automatic mixing, and automatic transportation, which greatly reduces the burden of manual operation.
high productivity
The feed mill engineering has very high production efficiency, which can meet the needs of different feed projects and improve production efficiency. The production line is usually well laid out and planned, and the handover between each process is orderly, thus speeding up the production of products.
Stable feed quality
The large feed plant engineering can ensure the stable quality of feed, reducing the defective rate and quality problems. The production process can be strictly monitored and controlled to ensure that each product meets certain quality standards.
energy saving
The feed mill adopts advanced environmental protection technology, which reduces the emission of waste gas and waste water, and also reduces energy consumption. The animal feed production line can also achieve the rational allocation and utilization of materials, tools and labor, thereby reducing waste and losses.
Flexible equipment configuration
Understand the customer’s needs for feed processing in detail and select relevant equipment. Different types and forms of feed require different processing equipment. The production line configured by our company has a novel and scientific equipment combination, a more reasonable and compact on-site layout, and a small on-site area of the production line, saving investment.
CustomizationLow production cost
Feed mill engineering technology can help companies significantly reduce costs, especially in large-scale production, by effectively reducing raw material costs, production and management expenses, etc. Through standardization and mass production, the production line can reduce the cost of materials, labor and equipment, while also saving time and manpower expenses.
equipment for feed mill engineering
Common equipment in feed mill engineerings include crushers, mixers, granulators, coolants, extruders, screeners, balers, silos, cleaning equipment, control cabinets, environmental protection equipment, sprayers, feed dryers, etc. Explore our range of equipment and solutions tailored to your animal feed needs. We’re here to help you achieve the best results for your feed production. Let’s work together to optimize your animal feed process and elevate your business.
hammer mill feed grinder
Used to crush granular raw materials.
feed mixer machine
Used for mixing raw materials and additives.
feed mill pellet machine
Used to process powdery materials into pellets.
pellet cooler machine
Used to cool pressed feed pellets.
vibrating screening machine
Used to screen out qualified feed pellets.
Automatic Bagging Machine
Used for packaging various types of feed products.
twin screw extruder
Used in feed mills using extrusion technology.
belt dryer machine
Used for drying raw materials or granular products.
storage silos
Used to store bulk raw materials such as corn.
Electric control cabinet
Used to control the automated production and operation of the entire feed mill.
screw conveyor machine
Used for horizontal or short distance material and product transportation.
bucket elevator conveyor
Used for vertical material and product transportation.
RICHI MACHINERY
equipment Configuration
Here is the main equipment list of 120t/h large scale feed mill engineering:
In our cutting-edge animal feed mill plant, we integrate the latest technological and equipment to consistently achieve optimal performance in animal feed production.
Our dedication to innovation ensures our feed mill stands as a cornerstone of efficiency and reliability in the industry, redefining the standards of excellence in animal feed production.
NAME | MODEL | QTY |
Drum type precleaner | SCY80 | 4 |
Powder cleaning sieve | SCQZ90*80*110 | 8 |
feed grinder | SFSP66*100 | 4 |
feed grinder | SFSP138*50E | 4 |
Single-shaft mixer | SLHJ6.0A | 4 |
animal feed Pellet machine | SZLH508 | 8 |
Cooling Machine | SKLN24x24 | 8 |
Crumbler | SSLG20*170 | 8 |
Rotary screener | SFJZ150*2C | 8 |
Packing machine | DCS-50 | 8 |
Sewing machine and conveyor belt | 8 | |
Heating oil storage tank | SYTZ200 | 4 |
Add oil line | 4 | |
Weight oil system | 4 | |
MCC Control Center ;Mimic control panel (power range from 22 kw for star triangle start, main electric components are delixi brand) | ||
CPP Computer System | ||
Batching System: fully automatic, controled by computer | ||
Cables & Cable Bridge Tube and (From the MCC to equipment) |
Construction plan of different capacity feed mill engineering
RICHI recognizes the diversity of our customer’s needs. Our 1-120 t/h feed mill engineering is designed for both entry-level and established feed producers, ensuring seamless and efficient feed production with cutting-edge technology and expert services.
Perhaps you are interested in the construction of feed mills with these outputs.
animal feed production plant
3-4T/H feed production
animal feed pellet plant
5-7T/H feed production
animal feed processing plant
8-10T/H feed production
feed preparation plant
12-20T/H feed production
feed pellet production line
25-40T/H feed production
commercial feed mill
50-60T/H feed production
complete feed mill plant
60-80T/H feed production
Design and Build for Growth and Innovation
Meet global product demands and quality standards with industry-leading feed mill engineering design, engineering, equipment, and construction services for agricultural processors.
RICHI MACHINERY
Construction process of feed mill engineering
- First, at the beginning of the feed mill engineering project, it is necessary to prepare and approve the project proposal.
- Through in-depth market research and technical analysis, the economic, technical and social feasibility of the project is evaluated to provide a basis for decision-making. After the feasibility study report is evaluated and approved, a design plan task book will be prepared.
- Enter the design stage, and carry out surveys, designs and other work according to the approved design plan task book. This stage needs to fully consider factors such as the layout of the factory, process flow, equipment selection, etc. to ensure the rationality and feasibility of the design plan.
- Then enter the construction stage, carry out construction, installation and other work according to the design plan, and strengthen the management and supervision of the construction site to ensure the quality and safety of construction.
- Carry out trial production and acceptance. After the construction of the feed factory engineering is completed, trial production and commissioning will be carried out to test the operation of the equipment and the quality of the product. After acceptance, the factory can be officially put into operation.
featured feed mill engineering project
Below we will introduce to you a featured 100-120t/h large scale animal feed mill engineering projects we have participated in.
110-115T/H feed mill engineering project
The customer of invest in this feed mill engineering project with an annual output of 360,000 tons, with a total investment of 2,850,000 USD. It will be constructed in two phases. The current compound and concentrated feed factory project is a phase 1 project with an annual output of 240,000 tons. The development model of the livestock industry cluster integrating processing, feed production, breeding chicken breeding, chicken hatching, and commercial chicken breeding is introduced into the local area.
The big feed mill engineeringproject covers an area of 23083m² and a building area of 17,160m². The planned construction period of the project was 200 days, and it was put into production in the same year.
- Work system: The labor quota is 30 people, the project produces 260 days a year, each shift is 8 hours, and the system is one shift. It can be calculated that the output of the project is 110-115 tons per hour, 20000 tons per month, and 923 tons per day.
- Construction Content:The industrial animal feed mill factory project covers an area of 23083m² and a building area of 17,160m2. It mainly includes 1 production workshop, 2 silos, 1 raw material warehouse, 1 finished product warehouse, 1 boiler room, 1 office building and 1 guard room.
- Raw And Auxiliary Materials And Consumption (t/a): Corn*36,000, Barley*12,000, Soybean meal*112,500, DDGS*19,300, Puffed corn*19,200, Stone powder*4,900, Bran*19,600, Rice bran powder*15,200, Additives*0.21 million, etc.
- Energy Consumption: electricity consumption500,000 kw•h, fresh water consumption is 5614t/a
120-125T/H feed mill engineering project
The large scale feed mill engineering project covers an area of 26,600m², with a total investment of 2,420,000 USD. The project adopts the most cutting-edge technology in the world’s feed processing industry and adopts RICHI modern feed equipment, which can greatly improve the level of intelligence.
After the large animal poultry duck chicken pig fish feed mill engineering project reaches its production capacity, it will produce 300,000 tons of refined feed per year, with an annual output value of 157,100,000 USD, tax payment of nearly 3,267,680 USD, and employment of about 80 people, which will help promote the modernization and upgrading of the local agriculture and animal husbandry and improve quality.
- Work system: work 300 days a year, 1 shift per day, 8 hours per shift
- Project output: According to the work system, it can be calculated that the output is 120-125 tons per hour, 1000 tons per day, 25000 tons per month.
- Construction Content: Production workshop, Raw material warehouse,Finished product warehouse, Silos, Living, Office, Water supply system, Drainage system, Power supply system, etc.
- Raw And Auxiliary Materials And Consumption (t/a): Corn*100,000, Wheat bran*10,000, Wheat middling and red dog*10,000, Rapeseed meal*21,000, Flour*0.5, Premix*45000, Vegetable oil*30,000, etc.
- Energy Consumption: electricity 540,000kw, annual steam requirement is 4800t, water consumption is 4320m3/a.
RICHI MACHINERY
Feed ingredients for feed mill engineering
Raw materials used in feed mill engineering project include soybeans, corn, soybean meal, amino acids, fish meal, oils, grains, whey powder, feed additives, etc., and feed can be classified into roughage, silage, mineral feed, vitamin feed, green feed, protein supplements and additives according to the raw materials. In addition to the above conventional raw materials, unconventional feeds such as crop straw, bagasse, peanut shells, rice husks, food factory residues, slaughterhouse waste, and livestock and poultry manure can also be used.
RICHI MACHINERY
video Of feed mill engineering
RICHI MACHINERY
FAQ of feed mill engineering
How to design a raw material warehouse for a feed mill engineering?
- Area determination: Determined based on comprehensive factors such as whether there are silos, bulk silos, seasonal raw material storage, storage cycle, and the difficulty of raw material procurement.
- Structural design: Light steel structure is generally used, with a span of 22~24 m, which is more economical, and a column spacing of about 7 m; the height of the raw material warehouse eaves is determined according to the size of the warehouse area. The larger the warehouse area, the larger the eaves height. It is generally designed to be 7.0~8.0 m, which is more practical.
- Roof design: Roof materials generally use galvanized colored tiles + insulation layer or sandwich colored panels. The ridge should be designed with ventilation skylights. It is recommended to avoid setting up internal gutters for roof drainage, especially in the north where snow cannot be removed and snow water will penetrate into the warehouse. If there is an internal gutter, the diameter of the drainage pipe must be enlarged. The drainage pipe should be arranged from the air, not from the ground, to ensure that rainwater does not enter the warehouse and avoid raw material loss.
- Wall design: Galvanized colored tiles are generally used as wall materials. Whether to design an insulation layer depends on the climate of the feed mill engineering area. It can also be designed as a brick wall structure. It is recommended not to design windows on the wall. A ventilation belt can be designed at the junction of the wall and the roof, and a bird-proof net can be added. Lighting tiles can be installed on the side facade of the skylight to meet the lighting requirements of the warehouse.
- Ground design: In order to facilitate the unloading of bagged raw materials into the warehouse and shorten the transportation distance of raw materials, the ground should be able to carry 80 t of vehicles. In order to ensure that the raw materials are stored and deteriorated due to moisture, the ground should be designed to be moisture-proof.
- Gate design: In order to facilitate the passage of raw material vehicles, the warehouse gate should be designed to be larger. Generally, the gate is 5.0 m high and 5.0 m wide. In order to take into account the strength and lightness of the gate at the same time, it is recommended to design the gate structure of the warehouse as a sliding door in the form of a hanging, and use lightweight materials.
How to plan a reasonable environment for feed mill engineering?
Reasonable factory planning is the first step of a good feed factory engineering project.
From the site selection of the feed mill engineering to the environmental protection and safety supervision design, the functional division of the factory area determined by the process must meet the production process requirements, architectural feng shui requirements, fire protection and environmental protection requirements, and urban planning requirements.
- For the waste gas emission problem of the feed factory, the dust odor discharged from the crushing pulse fan, the odor discharged from the cooling fan, and the odor of the drying tail gas emission must be centrally cooled, and then purified by activated carbon and UV photolysis waste gas purification to meet European and American emission standards.
- In terms of noise treatment, sound insulation and vibration isolation materials are used; silencers are installed on the inlet and outlet pipe sections of the ventilator to control the noise radiated from the inlet and outlet.
- The separation of rainwater from production and domestic sewage in the feed mill engineering, as well as the separation of production sewage and domestic sewage, should be planned and designed in advance, and separate sedimentation tanks should be set up to divert the production wastewater and the wastewater and rainwater generated by the office canteen to their respective sedimentation tanks, and then discharged separately after sedimentation.
“Details determine success or failure”, RICHI strives for perfection in engineering details, from wear-resistant measures for equipment and pipelines, noise treatment measures for feed mill engineerings, airflow, dust and odor treatment, precise measures for dust and explosion prevention, energy-saving fine buckle, quick disposal of tailings and miscellaneous materials and waste, equipment lifting, startup operation, human-machine safety, and humanized ergonomic design, so that the majority of companies using RICHI feed mill equipment and engineering can reap an environmentally friendly, clean, beautiful factory that creates wealth, and create a great future for harvest production lines!
We want to build a turnkey feed mill engineering. How do you control the progress of the project?
Rigorous engineering construction WBS node control, RICHI pays attention to the technical details of the feed mill engineering project, and strives to make every section, every equipment, and every component so fine that it can be measured, so as to maximize the avoidance of waste and improve production quality.
RICHI feed engineering control has a total of 255 nodes, which comprehensively control the progress, safety, and quality of project construction. The total construction period of on-site construction is accurately controlled. The company leaders can understand the progress of the project in real time, and make accurate decisions on safety and quality at the first time.
The project progress is reported on the work WPS nodes every day in the form of real scenes, and horizontal comparisons can be made between various engineering projects to compare progress, quality, and safety.
The achievement rate of each project and department is displayed in the form of bar charts, wave charts, and pie charts, providing intuitive data basis for the management and control of senior leaders, so as to ensure the timely delivery of good projects. (Find RICHI on youtube)
What does the overall plan of a feed mill engineering include?
After completing a series of preliminary preparations such as investment feasibility analysis, land inspection and purchase, land red line demarcation, raw material packaging and transportation methods, product capacity positioning, investment plan, government design planning, etc., the overall plan will be carried out.
It is the basis for process design, equipment selection and architectural design. It needs to reasonably arrange and organically connect the relevant single building facilities.
A good design should reflect the production characteristics, production functions and planning goals of the feed mill engineering, and the focus of the planning is the reception and storage of raw materials and the packaging and distribution of finished products.
How to divide the production functional areas of the feed mill engineering?
- Production area: mainly raw material reception and cleaning, raw material storage, production workshop, finished product storage and distribution, boiler, power supply, machine repair, hardware, woven bags and drug room.
- Office area: mainly includes general manager, finance, raw materials, quality control and testing, production, sales, reception, meeting and door guard departments, as well as facilities such as weighing scales.
- Living area: mainly includes dormitories, canteens, bathrooms, bathhouses, entertainment, etc.
Any Question?
You can ask anything you want to know about Feedback
● RICHI MACHINERY
service for feed mill engineering
Any Problem, Please Contact Richi Machinery. The Exclusive Customer Service Manager Will Provide One-Stop Worry-Free Solutions.
● Consulting
Customer Consultation
We want to have a deep understanding of your industrial process, to know your exact needs of feed, wood, biomass, fertilizer or other pellet processing.
● Design
Pellet Plant Design
Based on your unique situation and industrial process, we will tailor complete pellet plant you need, and inform you of every additional detail that could facilitate operation, minimize total cost.
● Manufacturing
Equipment Manufacturing
The critical components of the of the complete pellet production line equipment are built in our own workshops in Asia. Additional equipment is manufactured by our worldwide network of reliable partners.
● Testing
Quality Inspection & Testing
Before leaving the factory, all equipment will be inspected by the quality inspection department. We can also provide customers with testing services from a single machine to a complete pellet plant system, and provide you with real actual data for “worry-free use.”
● Delivery
Equipment Delivery
In equipment boxing and packaging, we adopt professional packaging and modular solutions to ensure the safe and non-destructive delivery of pellet plant equipment.
● Installation
Installation & Commissioning
Whether you choose your own subcontractor for the erection phase or you want to install everything together with us, a Richi supervisor will be around to make sure everything is mounted in a safe and thorough way.
● Training
Staff Training
We provide comprehensive training for the technicians of each project. We can also continue to provide support for the technicians during latter project operation.
● After-sales
Project Follow-Up
When everything is up and running our Richiers will help you further whenever needed. We are ready to answer your call 24/7.We’ll also visit you regularly to learn about your needs.
Who We Are
RICHI Machinery is one of the world’s leading suppliers of technology and services for the animal feed, aqua feed and pet food industries, also the largest pellet production line manufacturer in China.
Since 1995, RICHI’s vision to build a first-class enterprise, to foster first-class employees, and to make first-class contributions to society has never wavered.
In the past three decades, we have expanded our business to a wide range of areas, including animal feed mill equipment, aqua feed equipment, pet feed equipment, biomass pellet equipment, fertilizer equipment, cat litter equipment, municipal solid waste pellets equipment, etc.
1995
RICHI Established
2000+
Serving More Than 2000 Customers
120+
RICHI Employees
140+
Exported To 140 Countries
RICHI MACHINERY
Customer Reviews
Our service territory is slowly expanding; in our interactions with tens of millions of customers, whether it is a small scale feed mill or a large feed mill engineering, we have received sincere suggestions and genuine praise… allowing you to see real animal feed factory project sites, gain an in-depth understanding of our products and services, and achieve value doubling and sharing.
15-25T/H feed mill engineering in Uganda
The whole feed mill engineering project was built quickly, put into production stably, and the equipment has been running smoothly without any failure. It has become a benchmark project here. Many companies in Africa have come to visit and began to consult RICHI. RICHI’s feed equipment is of good quality and the service is timely. We are also happy to welcome more visitors.
30-40T/H feed mill engineering in Mexico
Our production line is a renovation of an old production line. The previous production line had a large number of equipment, high energy consumption, and troublesome maintenance, so we decided to upgrade the old equipment. After comparing many options, we finally chose RICHI’s feed equipment, and the results also made us very satisfied. RICHI’s equipment has low energy consumption and high output, which has greatly improved our efficiency!
8-10T/H feed mill engineering in brazil
Our company has been cooperating with RICHI Machinery for a long time. This production line is now in the second phase of the project. The first and second phases are installed together. It has been officially put into production for more than two years. Last year, we purchased equipment from RICHI for the third time. The site is not far away and is currently under construction. We trust RICHI’s quality!
60T/H feed mill engineering in russia
We heard that this project is RICHI’s largest feed production line in Russia, and we are very honored to cooperate with it. The entire production line process is not complicated, and it uses two very mature systems of RICHI – poultry pelleting line and aquatic product extrusion line. After the project was established, RICHI sent engineers to provide guidance on site planning and leveling, equipment installation and non-standard parts production, all of which were in place.